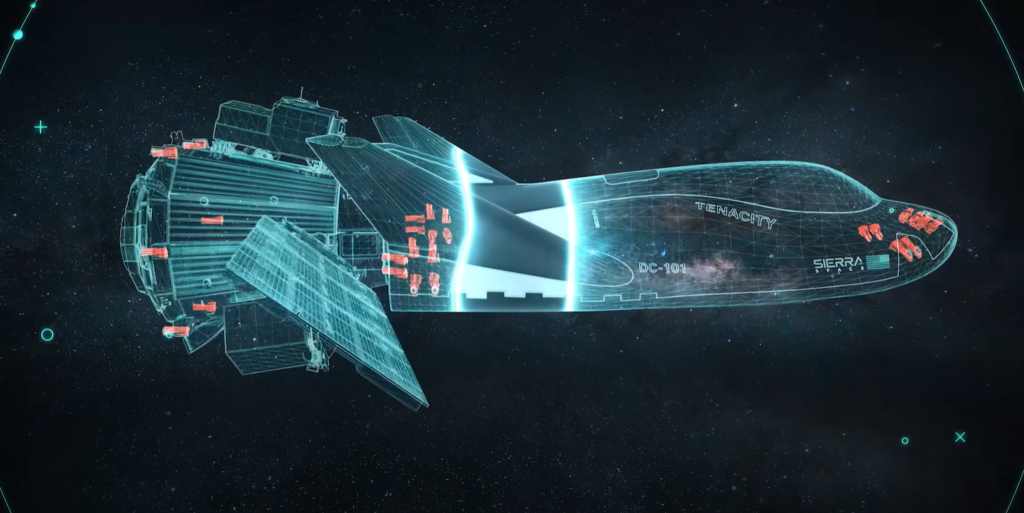
The Small Thrusters Controlling The Dream Chaser Spaceplane
Dream Chaser has gone through many different design changes and plans throughout its 2 plus decade development. For a while, the company wasn’t sure whether or not they would make a crewed or uncrewed variant or combine the two. By now Sierra Space has a set plan and with this outlined designs for specific Dream Chaser variants and features.
The first launch and subsequent launches will all be with an uncrewed Dream Chaser. In order for this spacecraft to move around and orient itself, it will rely on 24 Reaction Control System thrusters located at the front and back of the spacecraft in addition to the Shooting Star module. Other than these thrusters, there will be no main engine on this spacecraft.
Instead, the only Dream Chaser variant so far that features larger primary engines is the crewed version which is still very early in development. These design choices are based on the mission profile and needs of each Dream Chaser variant. Here I will go more in-depth into these propulsion systems, their application in space, what to expect in the coming months, and more.
Tenacity’s Propulsion
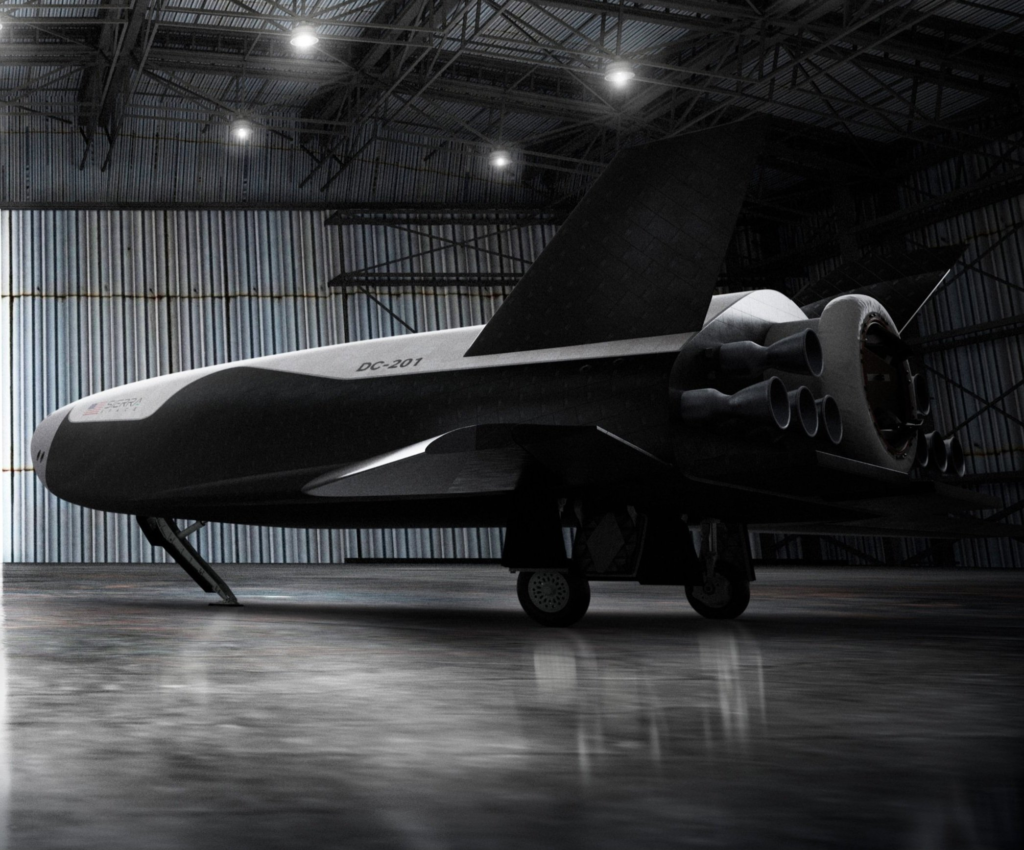
Tenacity is the name of the Dream Chaser test article scheduled to lift off late this year in December. Looking at footage of this spaceplane while being assembled by Sierra Space highlights the lack of main engines. At the back of the spacecraft, all you can see is the main access port where it will attach to Shooting Star.
All this being said, animations of Dream Chaser provided by Sierra Space show off a similar design with two large rear engines providing thrust after separation from its launch vehicle. This is because Dream Chaser was originally designed as a crewed spaceplane, in part under NASA’s Commercial Crew Program, capable of carrying up to seven astronauts to and from the space station and other low Earth orbit (LEO) destinations.
On-orbit propulsion of the Dream Chaser was originally proposed to be provided by twin hybrid rocket engines capable of repeated starts and throttling. At the time, SNC Space Systems was also developing a similar hybrid rocket for Virgin Galactic’s SpaceShipTwo. In May 2014, SNC involvement in the SpaceShipTwo program ended. After the acquisition of Orbitec LLC in July 2014, Sierra Nevada Corporation announced a major change to the propulsion system. The hybrid rocket engine design was dropped in favor of a cluster of Orbitec’s Vortex engines. The new engines would use propane and nitrous oxide as propellants.
In addition, the large engines were needed with the first crew design in case of an anomaly during lift off. Dream Chaser needed the capability to light its engines and separate from the exploding first and second stages in case of an emergency. While this is still a modern concern and factor, the way Sierra Space is approaching it has changed. The most up to date information we have on this future propulsion system came in the form of a picture posted by the company. The image showed both an uncrewed and crewed Dream Chaser variant. The crewed variant featured 8 engines on the back.
By now we know that Sierra Space is working on both thrusters for the current uncrewed variant and main engines for the future crewed variant. The company highlights that the Vortex engine thrust chamber assembly confines propellant mixing and burning to the core region of a coaxial vortex flow field. This is intended to enable dramatic cost savings through robust design margins and also lead to extremely high durability, reliability, and reusability in engines that are inexpensive to manufacture and maintain. This is an important feature considering a single uncrewed Dream Chaser launch requires 24 of them.
The coaxial vortex flow field is also applicable to hybrid rocket engine systems to produce fuel regression rates significantly higher than conventional hybrid configurations. This increase in fuel regression rate enables the use of a simple circular grain port, conferring significant gains in performance, reliability, and durability of hybrid systems.
As of 2020, the Sierra Nevada Corporation says it still plans to produce a crewed version of the spacecraft within the next 5 years. The company says it “never stopped working” on the crewed version and fully intends to launch it after the cargo version, and is still committed to the crewed version as of 2021. In November 2021, Sierra Nevada Corporation reported that it received a $1.4 billion investment in Series A funding, which it will use to develop a crewed version of Dream Chaser and fly astronauts by 2025. Assuming initial flights with the uncrewed variant go well, the crewed version should start launching not too long after.
Engines & Thrusters
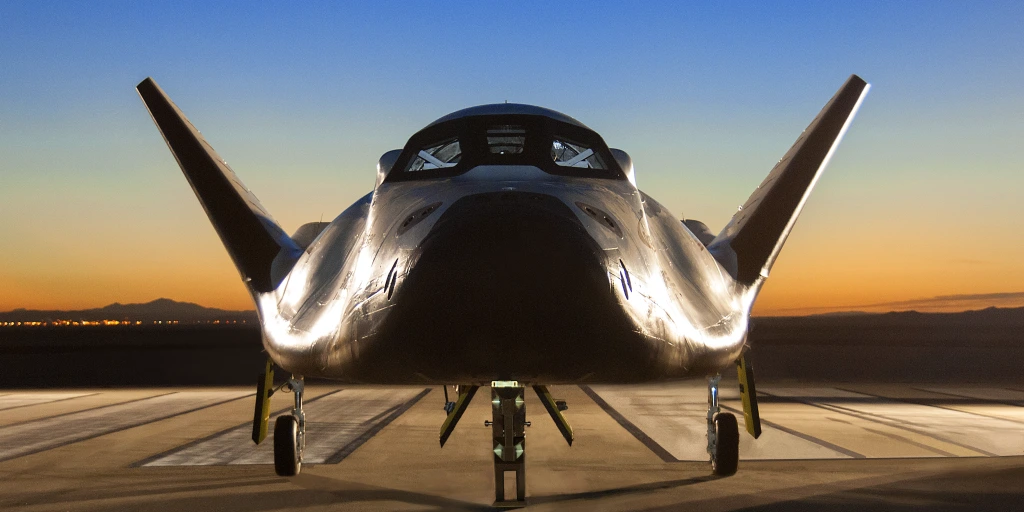
Sierra Nevada Corporation has been working on both the main engines and thrusters of the Dream Chaser Spaceplane for a very long time now. Back in 2014, SNC announced it completed a major Main Propulsion System (MPS) and Reaction Control System (RCS) risk reduction milestone for the Dream Chaser, maturing the design of each system close to Critical Design Review (CDR).
Here, SNC completed the work for milestone 9a under its Commercial Crew Integrated Capability (CCiCap) agreement with NASA. The Main Propulsion System is based on SNC’s patented rocket motor technology. To date, SNC has performed hundreds of rocket motor test firings at its Poway, California, facility advancing the motor technology with each test. The Dream Chaser MPS was not only planned to power the spacecraft in orbit, but also offer a unique abort capability while on the launch pad and throughout the flight trajectory, unlike human space transportation capsules. The MPS technology used on the Dream Chaser results in a safe runway landing during an abort scenario, further reducing risk to the crew, spacecraft, and payload.
The RCS on the other hand, which was being designed by Orbital Technologies Corporation (ORBITEC), will provide precise on-orbit control of the Dream Chaser spacecraft. The RCS will provide maneuvering capability to allow for the accurate docking of the Dream Chaser to destinations in low-Earth orbit. Dream Chaser is a multi-mission capable spacecraft that has the ability to operate as an independent science platform or as a logistics vehicle to retrieve, repair, replace, assemble or deploy items in space.
“Safety is paramount in the design of the Dream Chaser Space System,” said the corporate vice president of SNC’s Space Systems. “It is driven by reliability, rigorous quality assurance, consistent performance, and extensive testing and analysis. In passing this milestone we are able to validate our safety and performance, while decreasing the risk for each of these systems. Completing this milestone moves the Dream Chaser closer to the Critical Design Review of our complete system” he said.
A reaction control system is a spacecraft system that uses thrusters to provide attitude control and translation. Reaction control systems are capable of providing small amounts of thrust in any desired direction or combination of directions. An RCS is also capable of providing torque to allow control of rotation. They often use combinations of large and small thrusters, to allow different levels of response. Because spacecraft only contain a finite amount of fuel and there is little chance to refill them, alternative reaction control systems have been developed so that fuel can be conserved. For stationkeeping, some spacecraft (particularly those in geosynchronous orbit) use high-specific impulse engines such as arcjets, ion thrusters, or Hall effect thrusters.
The Space Shuttle for example had many thrusters, which were required to control vehicle attitude in both orbital flight and during the early part of atmospheric entry, as well as carry out rendezvous and docking maneuvers in orbit. Shuttle thrusters were grouped in the nose of the vehicle and on each of the two aft Orbital Maneuvering System pods. No nozzles interrupted the heat shield on the underside of the craft; instead, the nose RCS nozzles that control positive pitch were mounted on the side of the vehicle, and were canted downward. The downward-facing negative pitch thrusters were located in the OMS pods mounted in the tail/afterbody.
To put in perspective the importance of these thrusters, the failure or degradation of the aerodynamics or flight control system of the shuttle could result in loss of vehicle control during this phase of flight. Some possible failure scenarios are debris impact or wing damage that could cause large aerodynamic asymmetries that produce large torques.
Approximately four hours prior to deorbit, the crew began preparing the orbiter vehicle for reentry by closing the payload doors, radiating excess heat, and retracting the Ku band antenna. The orbiter vehicle maneuvered to an upside-down, tail-first orientation and began a 2–4 minute OMS burn approximately 20 minutes before it reentered the atmosphere. The orbiter vehicle reoriented itself to a nose-forward position with a 40° angle-of-attack, and the forward reaction control system (RCS) jets were emptied of fuel and disabled prior to re-entry. Some patterns we could see in the future as Dream Chaser continues to develop.
Conclusion
Dream Chaser has gone through a host of different designs over the last few decades. The current Dream Chaser expected to fly in only months doesn’t feature any large main engines as it only needs thrusters to maneuver once in space. In the future, however, this will change with different variants and requirements. We will have to wait and see how it progresses and the impact it has on the space industry.