
The Environments Within Firefly Aerospace’s Alpha Launch Vehicle
Firefly Aerospace has been hard at work on their small-lift launch vehicle named Alpha. While the company was only founded a few years ago, they have managed to make very consistent and impressive progress not only on Alpha but other aspects of the business as well. Alpha is working out to become a very high-quality and realistic competitor in the future of small-lift launches.
Firefly Aerospace has managed to create a unique design throughout the launch vehicle including the environments as well. Some of the main environments that play an important role include acoustics, shock, vibration, and thermal and cleanliness. All of which need to be tested and accounted for when developing a rocket of any kind. Launches are a very violent process that can easily damage the payload if ignored.
While a lot of focus goes on other components of a rocket such as the engines and main structure, there is practically an endless list of additional factors to consider. Earth’s atmosphere presents a major problem for not only getting out of it but doing it in a safe and controlled manner. The environments of a rocket play into this in a big way and are responsible for keeping the payload, rocket, and more, stable among other things.
Loads & Environments

Alpha is a small-lift launch vehicle currently being developed and tested by Firefly Aerospace. The company is working to create a very cost-effective and efficient launch vehicle that can compete in the market. Taking a closer look at Alpha, the loads and environments play an important role and Firefly Aerospace has worked to improve each aspect. Specifically, Alpha launch vehicle loads and environments are less than those historically produced by small to medium-class launch vehicles. This limits the need for payloads to use critical resources for additional isolation systems or other mitigation techniques. Meaning Firefly can achieve a higher payload capacity and more thanks to the reduction in environments and loads.
One of the key design elements to reduce environmental levels include eliminating the use of pyrotechnic devices near the payload. Another is near full coverage acoustic panels in the fairing. Then there are pad-based water suppression and advanced composite structures that mitigate transmission of LV-produced loads and environments. In addition, Firefly worked on precise sizing and design of each launch vehicle stage and combined that with exceptional engine performance. Together, this significantly limits exposure of the payload to excessive loads. Prior to launching, the payload must be tested and checked within each environment to ensure it will hold up to the forces applied.
Alpha Environments
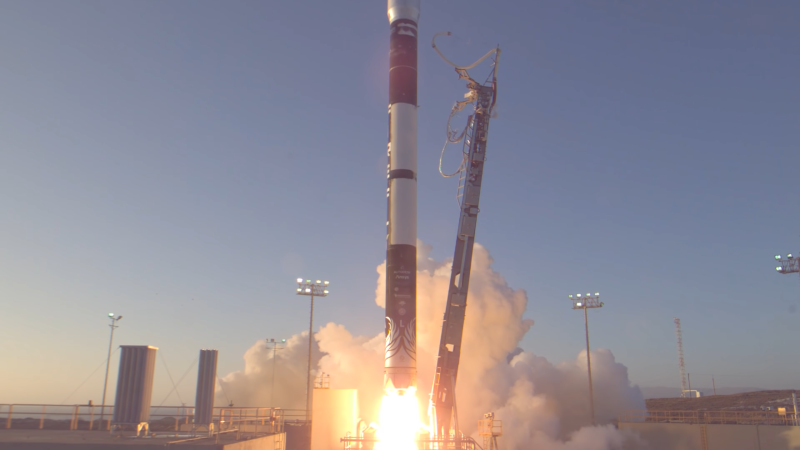
Acoustics – The first important aspect of Alpha’s environments has to do with acoustics. Rockets are not only very powerful, but loud as well. So loud it could easily damage a payload if not tested and reduced within the fairings of the launch vehicle. The Alpha launch vehicle acoustic protection is intended to provide an Overall Sound Pressure Level or DASPL, well below 139 dB. Firefly Aerospace’s current predicted sound pressure levels within the Payload Fairing and insulative foam are well below this value without the use of a water deluge. A chart provided by Firefly shows the decibels never getting above 130 and going as low as around 116. This is the maximum predicted acoustic environment of the Alpha launch vehicle without water suppression. Firefly plans on adding a water deluge system which will further reduce the predicted values well under 139 dB.
Shock – The next feature of Alpha’s environments that play a necessary role in the safety of the payload and rocket has to do with shock. When launching, the maximum shock environment at the payload interface occurs during payload separation from the vehicle’s second stage and is dependent on the payload separation system configuration. Shock levels at the payload separation interface due to stage separation, engine ignition and cutoff, and payload fairing separation are all maintained below a maximum acceleration of 1,000 g’s at 1000 Hz. Firefly provides multiple tables and graphs depicting the Alpha launch vehicle shock environment, but does not include the mission-specific payload separation system. Taking a closer look at the relation between the two, at 100 Hz of frequency, acceleration is at 30 g. At 100-1000 Hz the acceleration gradually increases up until 1000 gs at 1000 Hz. Finally, between 1,000 and 10,000 Hz of frequency, the acceleration stays at 1000 g.
Vibration – Another important aspect of Firefly’s Alpha launch vehicle environments focuses on vibration throughout the launch process. A payload sitting on top of a rocket during a launch is bound to be put through very intense and powerful vibrations. Firefly has worked to improve and ensure the vibrations within the payload fairings are kept to a minimum so the cargo or anything else does not break. Specifically, payloads are subjected to a combination of engine vibrations, vehicle structural modes, acoustics, and aerodynamic forces transmitted through the launch vehicle and into the spacecraft interface. The intensity of these vibrations is highly dependent on the payload mass, stiffness, and the interface between the payload and the launch vehicle. Firefly provides multiple charts and tables highlighting the predicted maximum random vibration PSD for a payload mass of 90 kg or greater. Starting at a frequency of 20 Hz, the PSD level is 0.003. PSD stands for power spectral density and refers to vibrations and vibration analysis. Between 100 and 700 Hz, it rises to a PSD of 0.02. Finally, at 2000 Hz it falls back down to a PSD of 0.003.
Thermal & Cleanliness – The last feature of Alpha’s environments that I wanted to mention has to do with thermal and cleanliness. The Alpha launch vehicle provides the payload with standard thermal, humidity, and high-efficiency particular air all the way from encapsulation through liftoff. The payload protection encompasses liftoff until an adequate free molecular heating rate is achieved for fairing separation. Alpha is designed to accommodate contamination-sensitive payloads from integration in the PPF, roll-out to the launch pad, and through launch. Alpha’s standard service will accommodate most payload cleanliness requirements. In cases where payloads require extensive cleanliness environments, Firefly can provide additional cleaning, filtration, contamination mitigation protocol, and verification services. Taking a look inside the fairings, all major surfaces including the PLF, Acoustic Blankets, and PAF, are visibly cleaned to a very high standard. When it comes to air cleanliness there are a lot of systems in place to ensure an incredibly clean environment. This includes an air diffuser preventing high-velocity air impingement directly onto the payload, air ventilates out through ports on the PLF, and much more. Lastly, you have the temperature within which is controlled to a very specific number ensuring it is not an issue throughout the entire launch process and time leading up to it.
Conclusion
Firefly Aerospace has been expanding and developing at a very fast pace. This especially is the case with their small-lift launch vehicle Alpha. A very important part of this rocket and the payload within has to do with environments and loads. Some of the main environments that play a big role include acoustics, shock, vibration, and thermal and cleanliness. All of which need to be considered and tested prior to launching any payload into space. Due to the violent nature of a rocket, these different environments can cause a lot of stress on the payload and easily damage it if not controlled. Firefly Aerospace however has put a lot of time and effort into improving the quality and effectiveness of each environment. With Alpha continuing to be tested and launched, we will have to hope for its success and wait to see its impact on the space industry.