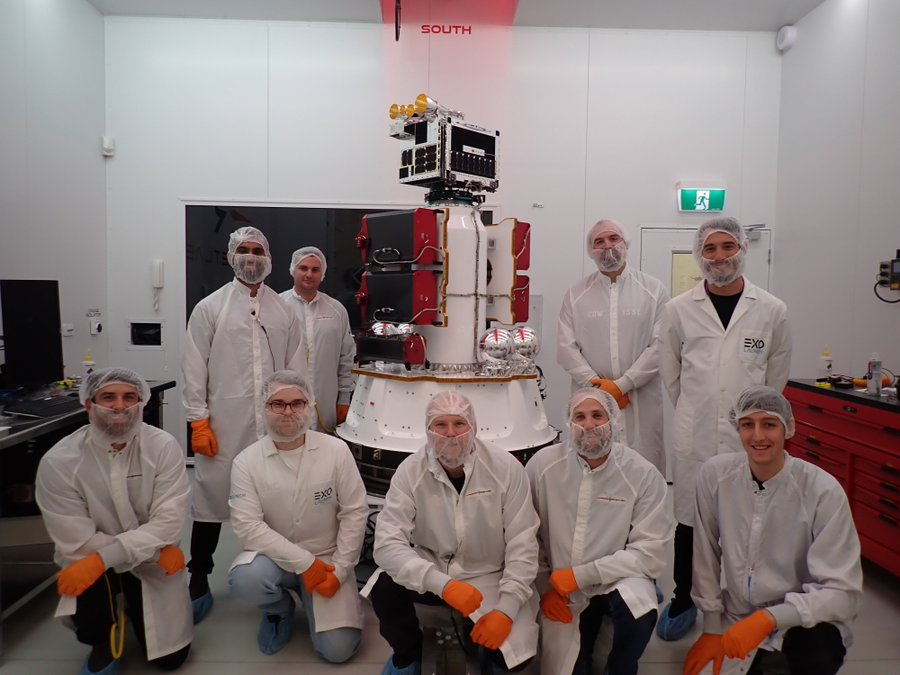
Why Rocket Lab’s Upcoming Launch Is So Important
Tonight Rocket Lab’s Electron rocket is scheduled to lift off and has quite a unique mission profile planned. As the 39th Electron launch, the rocket is not only carrying multiple payloads in a rideshare configuration, but it will also test partial reusability. Something Rocket Lab has been working on for years now as they try and figure out the best method.
Reusability with rockets is already an extremely complex process, with small launch vehicles however there are additional challenges as you have very little fuel margins left over. This in combination with a few other factors limits the options to recover even just the booster. Despite this, Rocket Lab has tried a few different methods and is confident they found the best one.
This involves letting the booster slowly parachute into the ocean where with the help of some water proofing and a fast recovery, they can refurbish it in a short period of time. Here I will go more in-depth into the exact mission profile, the payloads being launched, what to expect in the next few days, and more.
Mission Profile
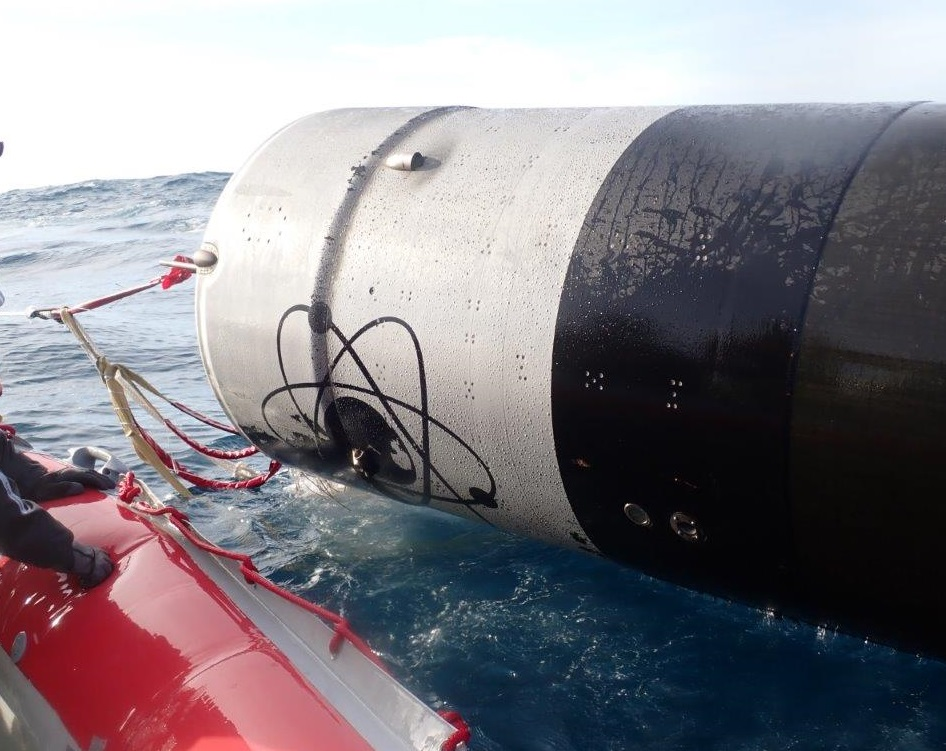
The mission, called “Baby Come Back” will deploy seven satellites to space and include an attempt to recover the rocket’s first stage after it splashes down in the ocean. The launch is scheduled to happen tonight from Pad B at Launch Complex 1 in Mahia, New Zealand.
Since deciding to focus solely on marine recovery operations, the Recovery team has made significant alterations to Electron that will progressively iterate marine salvage solutions. Recovery Electrons are now specifically designed to spend time in the ocean. This means including improved sealing solutions for the interstage, powerpack, and some internal components on the Rutherford engines to improve saltwater resilience. The expectations for these modifications and upgrades is that the engines will be fully resilient.
For this mission, the Recovery team is using a new, lighter parachute system on the booster, and will be the first mission to use a two-point lifting method to retrieve Electron’s first stage from the water. The recovery vessel has been fitted with new equipment including twin davits and deck platforms designed by Rocket Lab. Once aboard, the crews will begin immediate work to flush the saltwater from Electron and send it on its way back to the factory. Later this year, Rocket Lab will refly a recovered Rutherford engine for the first time, bringing the company even closer to reusability.
On this launch, the company is putting a lot of focus on getting to Electron’s booster as fast as possible, and removing it from the water quickly as well. Even with efforts to waterproof the stage, the less time it’s in the ocean the better off Rocket Lab is. This likely will correlate to how much of it can be refurbished and how long that process takes.
“There are some internal vehicle changes to improve its ability to keep water out of the areas where we don’t want it,” said Peter Beck, chief executive of Rocket Lab, in an interview. “We’ve taken this next opportunity to improve the watertightness of the vehicle.” He also commented that the new method of getting Electron out of the water “makes it much simpler to recover and much less likely to damage the stage during recovery.”
Beck said the company is taking a “methodical” approach to reusability, making incremental steps that get it closer to full reuse. “I’m sure we’ll learn something from this mission and we’ll probably make some tweaks again to the next one. We’re methodically walking step-by-step and taking the opportunity to get it right.” Rocket Lab does have a timeline to get to reusing an Electron booster, but Beck declined to disclose it. He added that while reusability was an “important economic lever” for the company, it was not an urgent requirement. The company has previously emphasized that reusability would allow it to increase launch activity without having to scale up its factory.
“From a production standpoint, the factory can keep up,” he said. “It’s not an existential requirement that we have to have it, hence why we’re being pretty methodical about it.” The company thought that catching the stage out of mid-air would be the future of Electron recovery. Unfortunately, after a partial catch during the first mission that had to be dropped, and a missed opportunity on the second, they decided to go this route. A change that could pay off depending on this mission’s results.
Payloads & Plan
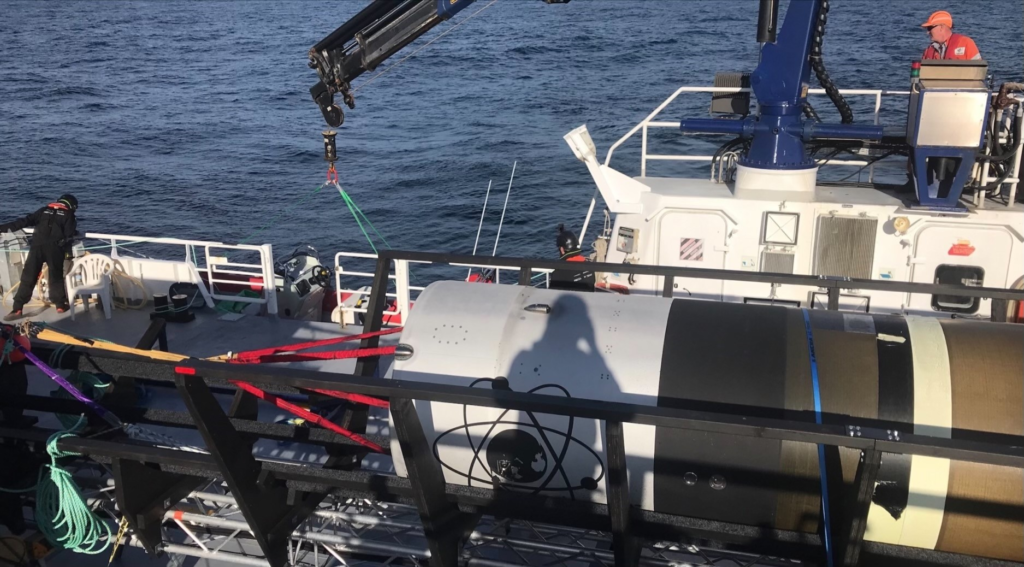
Besides the booster recovery attempt, this mission has a few different important payloads that need to be deployed precisely. First, you have NASA’s Starling mission which features four CubeSats designed to test technologies to enable future “swarm” missions. Spacecraft swarms refer to multiple spacecraft autonomously coordinating their activities to achieve certain goals. Starling will demonstrate technologies for in-space network communications, onboard relative navigation between spacecraft, autonomous maneuver planning and execution, and distributed spacecraft autonomy. An experiment for small spacecraft to autonomously react to observations, paving the way for future science missions.
Next, Space Flight Laboratory (SFL) selected Rocket Lab to launch Telesat’s LEO 3 demonstration satellite that will provide continuity for customer and ecosystem vendor testing campaigns following the decommissioning of Telesat’s Phase 1 LEO satellite.
Finally, Spire will launch two 3U satellites carrying Global Navigation Satellite System Radio Occultation (GNSS-RO) payloads to replenish its fully deployed constellation of more than 100 multipurpose satellites. Spire’s satellites observe the Earth in real time using radio frequency technology. The data acquired by Spire’s GNSS-RO payloads provide global weather intelligence that can be assimilated into weather models to improve the accuracy of forecasts. Spire is the largest producer of GNSS-RO weather data, collecting over 20,000 RO profiles a day.
What’s really cool about the mission is the addition of the Kick stage and how it helps deploy these three sets of payloads. Looking at the mission profile just after 9 minutes into launch the kick stage will separate from the upper stage. 46 minutes in and the kick stage will ignite its curie engine for about two minutes before cutting it off. At this point, the four NASA CubeSats will deploy and Spire’s two satellites. The kick stage will then ignite its engines again for around two minutes before cutting it off. It will then wait around 50 minutes before igniting the kick stage Curie engine one last time for around a minute before deploying SFL payload.
Rocket Lab’s Kick Stage offers its customers extra flexibility for orbital deployment. The Kick Stage is a third stage of the Electron launch vehicle used to circularize and raise orbits to deploy payloads to unique and precise orbital destinations. The Kick Stage is powered by Rocket Lab’s in-house designed and built Curie engine. In its simplest form, the Kick Stage serves as in-space propulsion to deploy payloads to orbit. In its most advanced configuration the Kick Stage becomes Photon, Rocket Lab’s satellite bus that supports several-year duration missions to LEO, MEO, Lunar, and interplanetary destinations.
The Kick Stage has deployed many satellites to standard 500 km altitudes but is also capable of transferring payloads to much higher altitudes. During Rocket Lab’s Electron mission, ‘As The Crow Flies’, the Kick Stage successfully raised the payload’s orbit to 1,200 km, before Curie performed a final burn to lower the stage’s perigee by more than 700 km to rapidly accelerate the de-orbit process to avoid the used stage becoming orbital debris. While this component is not reused and burns up upon reentry, Rocket Lab can manufacture them relatively fast.
The booster, on the other hand, takes time. Electron’s first stage consists of nine sea-level Rutherford engines, linerless common bulkhead tanks for LOx and RP-1, and an interstage. Rocket Lab’s flagship engine, the 5,600 lbf (24 kN) Rutherford, is an electric pumped LOx/ kerosene engine specifically designed for the Electron launch vehicle. Rutherford adopts an entirely new electric propulsion cycle, making use of brushless DC electric motors and high-performance lithium polymer batteries to drive its propellant pumps. This cuts down on much of the complex turbomachinery typically required for gas generator cycle engines, meaning that the Rutherford is simpler to build than a traditional engine but can achieve 90% efficiency. All the way back in 2020 130 Rutherford engines had already flown.
Rutherford is also the first oxygen/ hydrocarbon engine to use additive manufacturing for all primary components, including the regen cooled thrust chamber, injector pumps, and main propellant valves. The Stage 1 and Stage 2 Rutherford engines are identical, with the exception of a larger expansion ratio nozzle for Stage 2 for improved performance in near-vacuum conditions. All aspects of the Rutherford engines are completely designed in-house and are manufactured directly at Rocket Lab’s Long Beach headquarters in California, USA.
Conclusion
Rocket Lab is set to launch very soon and attempt the first booster splashdown with extra waterproofing and a few other changes. All of which are meant to keep the booster in the best condition possible and improve the refurbishment process. We will have to wait and see how it progresses and the impact it has on the space industry.