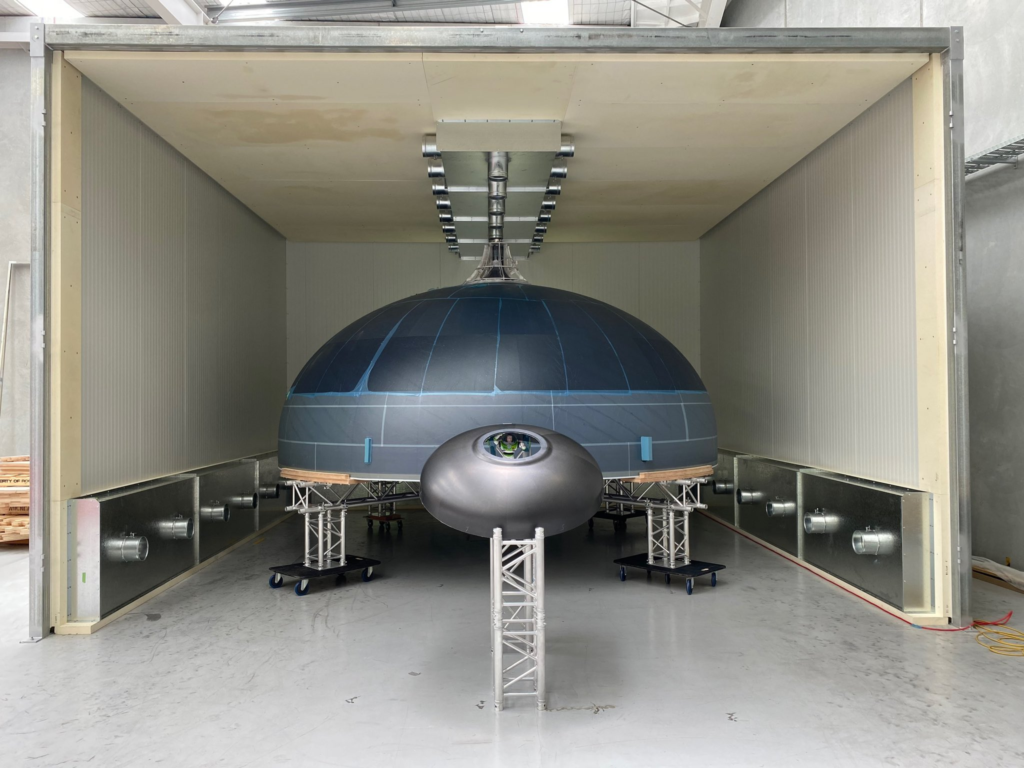
Rocket Lab’s Neutron Rocket Is Beginning To Be Manufactured
The Neutron rocket program is the future of Rocket Lab’s launch plans and features an extremely ambitious design. This medium lift partially reusable rocket wants to save the core stage and fairings. Combine this with its unique design and the company has a lot of work ahead of them. This being said, a decent amount of progress has already been made based on recent updates.
Just two days ago CEO of Rocket Lab Peter Beck hinted at the rocket’s progress with an image of a fully manufactured Neutron tank dome. Not to mention even more developments related to this next generation launch vehicle’s launch and production site in Virginia. All of which is a great sign as Neutron development has been somewhat quiet since the big update months ago.
If successful Rocket Lab will have significantly increased access to space with both Neutron and the Electron launch vehicle. However, before they get to this point, an immense amount of work still has to be made on both the rocket itself and its infrastructure. Here I will go more in-depth into the recent Neutron tank update, Virginia construction developments, what to expect in the future, and more.
Neutron Updates
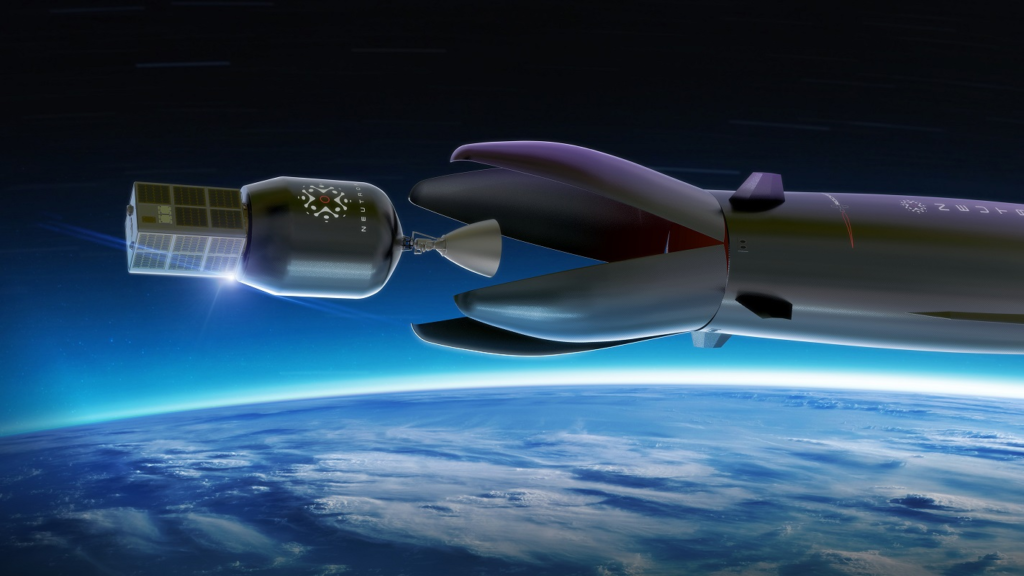
While Neutron updates are rare they are starting to become more common. Only two days ago on the 21st Peter Beck tweeted saying, “Neutron tank dome beside an Electron tank dome with a Buzz Lightyear for scale” This included an image of the two tanks lined up to better put the size difference in perspective. This Neutron dome already looks good however it is likely just a pathfinder as the company begins to manufacture the massive structure of Neutron.
Months ago during the Investor Day Presentation, Peter Beck highlighted that if done right, carbon composite like the one they are using can be very cost effective and strong by utilizing technology and strategies that the aerospace industry uses. Here, complete tanks are manufactured in days with minimal human labor and less material and waste than metallics. This is what Rocket Lab is aiming for with Neutron and its construction. In addition, he went on to talk about the difficulty of creating the molds and the initial tanks for Neutron. Specifically, tooling and molds are the complex, time-consuming part requiring extensive design work and refinement. However, with these now done, production began ramping up months ago. As Rocket Lab gets more practice and comfortable with the process, the speed and quality of different components such as the dome will only improve.
Taking a look at the image again also emphasizes the size of both these rockets. Electron is 18m (59ft) tall and 1.2m (3.9ft) in diameter with a payload capacity of around 300 kg. Neutron on the other hand is 40m (131ft) tall and 7 meters (23ft) in diameter with a payload capacity ranging from 8 to 15 tons to low Earth orbit. While the company’s history with Electron will most definitely help when developing Neutron, there are also a lot of unknowns with such a big jump in size and power.
Besides the Neutron rocket itself, Rocket Lab has also been working on its launch and production site in Virginia. Just over a week ago on December 14th, Rocket Lab tweeted mentioning, “As Electron waits patiently on the pad at LC-2 for this week’s launch, the first temporary structure for Neutron vertical tank assembly is taking shape at Wallops too. Neutron development is moving at pace and yes, we have roles open now” This included an image of the new temporary structure which is located on a concrete pad that Rocket Lab poured not long ago. Other images of the structure help give a better idea of its size and purpose. While not huge, it’s a good start and a sign that the company is eager to begin work without having complete factories built already.
Earlier this year Rocket Lab broke ground on the construction of a state-of-the-art rocket production complex where the Company’s Neutron launch vehicle will be manufactured. The 250,000 square foot Neutron Production Complex is being constructed on a 28-acre site adjacent to the NASA Wallops Flight Facility and Mid-Atlantic Regional Spaceport on Virginia’s Eastern Shore. As time goes on we can expect to see a lot of progress here as it becomes the backbone of the Neutron program.
Neutron Plan
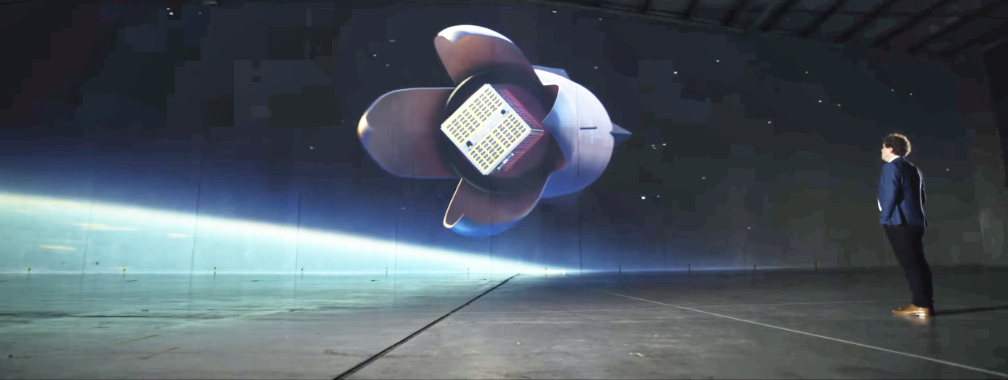
Now that we know more about some of the developments and progress being made on Neutron and its site, we can take a closer look at the plan for both this launch vehicle and its manufacturing process. As I just partially mentioned before, the Neutron Production Complex will be home to a rocket production, assembly, and integration facility, as well as a dedicated launch pad for the Neutron rocket located on the southern end of Wallops Island. This new complex will be Rocket Lab’s fifth global operations center for launch activities and on-orbit operations. To support rapid production of the Neutron rocket, current plans for the complex include automated fiber placement robotic production systems capable of laying up meters of Neutron’s new, specially formulated carbon composite structures in minutes. As a reusable rocket, Neutron is designed to land back on the Launch Complex 3 pad after a mission and from there it would be returned to the production complex for refurbishment and re-flight.
For example, the first stage has a tapered profile and aerodynamic control surfaces, including canards and landing legs that act as rear-lifting surfaces. This allows the first stage to glide back to Earth for landing, reducing the aerothermal load experienced by modern re-entry boosters. Not long ago they went over a render of what the future launch complex could look like. This included a static launch mount surrounded by propellant farms and fluid storage. Not to mention the addition of sea walls that go out and connect to an ocean landing platform. The big structure is what they call the rollover structure, designed to slide over the rocket for stacking and moving operations. Meant to operate all year round through adverse conditions. And in this case, even go all the way out to sea and bring it back to land.
Building on Rocket Lab’s strong heritage as a leader in composite technology, Neutron is trying to be the world’s first carbon composite large launch vehicle. Rocket Lab points out that reusability is at the forefront of Neutron’s design to enable frequent launch, and this new, specially formulated carbon composite material is lightweight, strong, and can withstand the immense heat and forces of launch and re-entry again and again to enable frequent re-flight of the first stage. Neutron’s design is especially unique thanks to its captive ‘Hungry Hippo’ fairing design. This innovative design will see the fairing form part of the first stage structure and remain fixed to the stage. Rather than separating from the stage and falling away to the ocean like traditional fairings, Neutron’s Hungry Hippo fairing jaws will open wide to release the second stage and payload, before closing again ready to return to Earth with the first stage. What lands back on the launch pad is a complete first stage with fairings attached, ready for a new second stage to be integrated and launched.
Even though the rocket has not been under development for a very long time, a lot of changes have already been made. The fairing for example features the same design but will only use two halves instead of four. Specifically, the fairing remains attached to the first stage, opening to deploy the second stage and payload within. The point of this is to eliminate the high cost of expending or capturing and reusing fairings. The downgrade reduces the amount of angle the fairing must open and enables more robust fairing panels.
Also, while the original plan was to have 7 Archimedes engines on the first stage, they decided to go for 9, for a total of 10 engines on the rocket including the second stage. Once operational, this engine is going to be reused again and again and the less stress it goes through the better. This also has to do with the change from a gas generator cycle to oxidizer rich closed cycle. In this case, as Rocket Lab worked through the content of operations and did all the power balances, they found turbine temperatures that were too high, a low amount of margin, and the need for a lot of compromises. Specifically, the oxidizer rich closed cycle provides a higher specific impulse than gas generator, open expander, or tap-off cycles, without the thrust limits or added complexity.
Gas generator cycles are limited in capability and not suited to the deep throttling required for multiple re-lights in orbit, and for landing the first stage. ORSC engines operate at relatively low temperatures and pressures, eliminating the stress and thermal strain experienced by gas generator engines. This improves engine life and reusability, while leaving headroom to increase performance. Most of these changes were announced months ago in September. By now, Rocket Lab has likely made other developments and small or big changes to the rocket and its future. A necessary process in the process of creating a next generation launch vehicle.
Conclusion
Rocket Lab is working hard to develop and manufacture the Neutron launch vehicle. Recently we learned more about its tank dome, size, and construction, in addition to some temporary structures popping up in Virginia. If successful, this rocket could change how we access space and Rocket Lab’s future within the industry. We will have to wait and see how it progresses and the impact it has on the space industry.