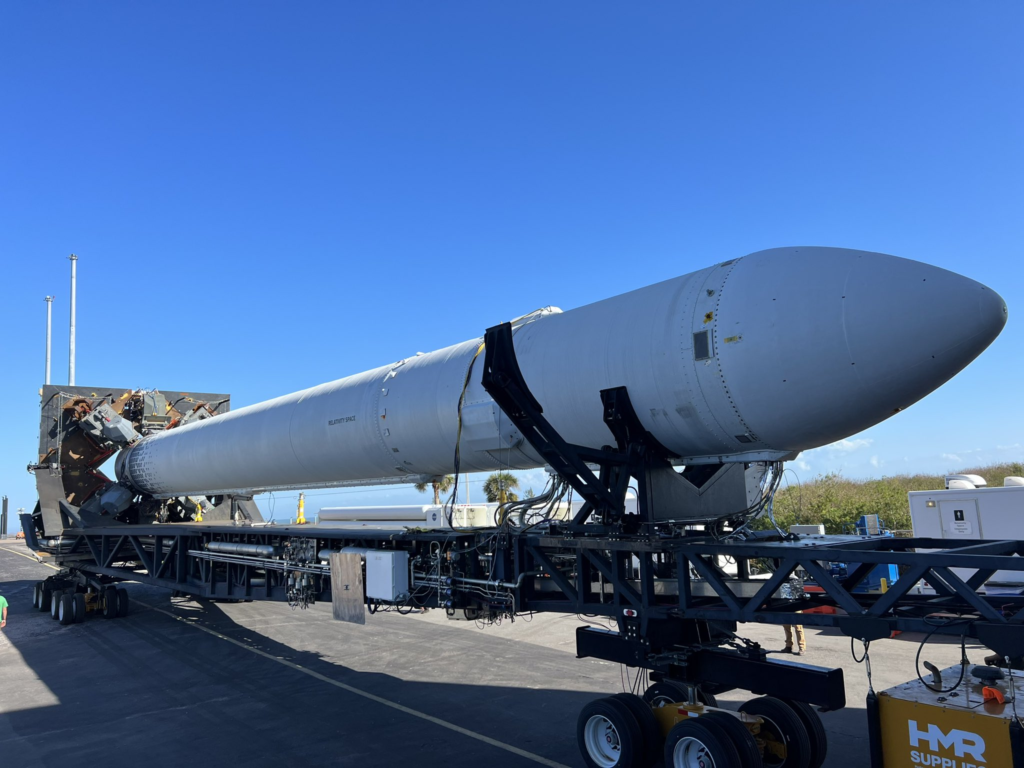
Relativity Space’s Terran 1 Rocket Is Now On The Launch Pad
Relativity Space is trying to change how rockets are manufactured within the space industry with 3D printing. Over the last couple of years, this company has been hard at work trying to prepare for the first orbital class 3D printed rocket launch of Terran 1. Now in early December, the company is only a few small steps away from making history.
Just yesterday Relativity rolled the Terran 1 test article out of its bay and onto the launch pad. From here, the company will need to complete a few tests to ensure everything is ready for launch before the long awaited maiden flight. While many rockets’ first launches are not successful, Relativity is confident and is guaranteed to at least gain a lot of invaluable information.
All of which comes in addition to more progress on the company’s next generation fully reusable and 3D printed rocket Terran R. CEO Tim Ellis also provided some valuable insight into this launch and its value. Here I will go more in-depth into yesterday’s rollout, why this launch is so important, the future of 3D printing rockets, and more.
Terran 1 Rolled Out
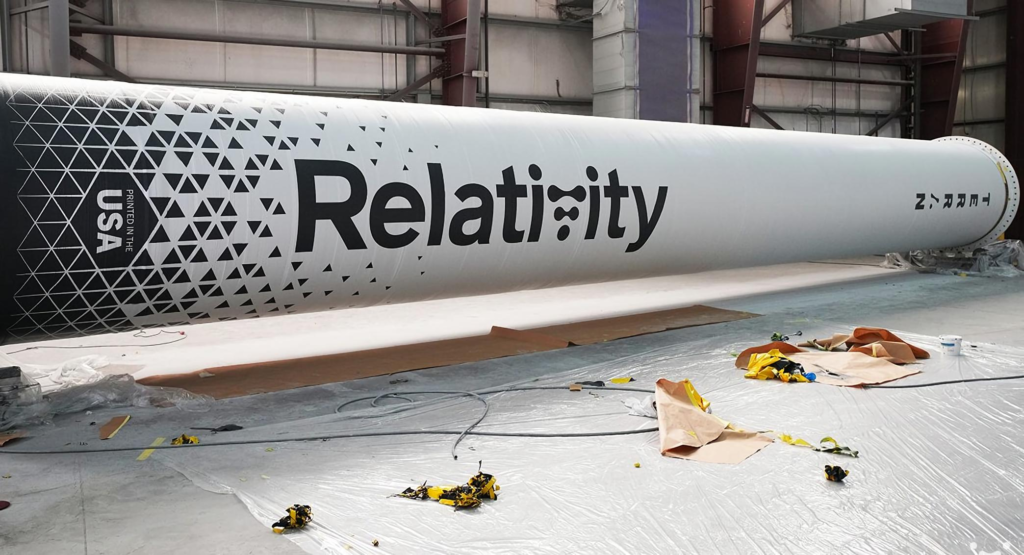
Starting just yesterday Relativity CEO Tim Ellis tweeted saying, “Ready to roll out!” Been waiting 7 years to say that.” This included an image of the Terran 1 test article on its way to the pad. At around the same time, Relativity Space tweeted mentioning, “It’s happening.” Which included a short video of the rocket being rolled out. As of right now Relativity is scheduled for its first launch of Terran 1, called “GLHF” (Good Luck, Have Fun), from Launch Complex 16 (LC-16) in Cape Canaveral in 2022. Based on this estimate is possible that we still see this launch within the next couple of weeks. However, a more realistic estimate is very early next year depending on the results of some final tests and prep.
This launch of Terran 1 is the first orbital attempt by Relativity and will not include a customer payload. As a two-stage, 110ft. tall, 7.5 ft. wide, expendable rocket, Terran 1 is the largest 3D printed object to exist and to attempt orbital flight. Working towards its goal of being 95% 3D printed, Relativity’s first Terran 1 vehicle is 85% 3D printed by mass. Terran 1 has nine Aeon engines on its first stage, and one Aeon Vac on its second stage. Like its structure, all Relativity engines are entirely 3D printed, and use liquid oxygen (LOX) and liquid natural gas (LNG), which are not only one of the best for rocket propulsion, but also for reusability, and the easiest to eventually transition to methane on Mars. As one of the few LOX/LNG fueled rockets in the industry, Terran 1 is racing to be the first LOX/LNG rocket to fly. With its current launch date estimate, it could very well be the first.
Back in October, we watched both the first and upper stages delivered to this launch complex. In the time since then, Relativity has been busy preparing this vehicle for its maiden flight. Since this specific mission is a test and does not include a customer payload, the Terran 1 test article features a nosecone rather than a payload fairing.
Just two days ago on the 5th, Tim Ellis tweeted again pointing out, “Vehicle to Transporter Erector integration complete for Terran 1; next up, final checks and pad rollout. This is ahead of vehicle static fire.” This confirms that once on the pad, Terran 1 will go through a wet dress rehearsal and static fire to ensure all the systems are working properly. If everything goes according to plan the company will be ready to launch in just a few weeks.
3D Printing Rockets
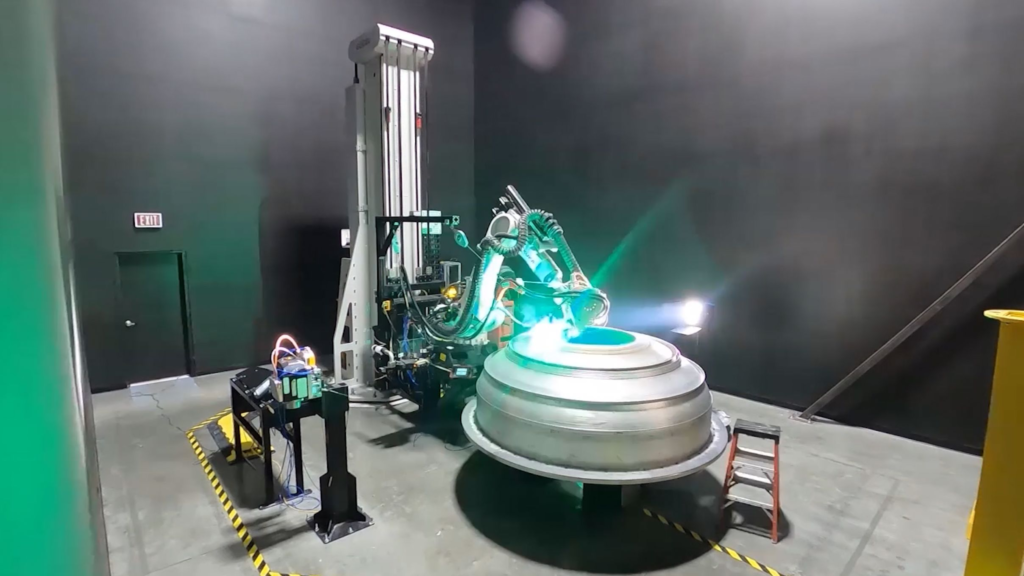
Now that we know more about Terran 1’s progress and its upcoming launch, we can take a closer look at the 3D printing process and this rocket itself. As a next generation launch vehicle, Terran 1 is designed for the future of constellation deployment and resupply. Relativity highlights that its groundbreaking, unique and software-driven architecture is capable of accommodating satellite customers’ evolving needs, while also providing the most agile and affordable launch service on the market. Designed and printed in the USA, they believe Terran 1 is the most innovative product to emerge from the aerospace manufacturing industry since the dawn of privatization of space 20 years ago.
As partially mentioned prior this rocket utilizes 9 Aeon engines on the first stage and one Aeon Vac on the second. These engines, Aeon 1, Aeon R, and Aeon Vac, are 3D-printed, enhancing mission reliability by reducing part count in engine combustion chambers, igniters, turbopumps, reaction control thrusters, and vehicle pressurization systems. Not to mention, to date, Aeon has completed 500+ test fires.
Relativity’s proprietary Factory of the Future centers on Stargate, the world’s largest metal 3D printers, that create Terran 1, the world’s first 3D printed rocket, and the first fully reusable, entirely 3D printed rocket, Terran R, from raw material to flight in 60 days. Relativity’s Stargate printers’ patented technology enables an entirely new value chain and innovative structural designs that make Terran 1 and Terran R possible. By developing its Factory of the Future and rockets together, Relativity accelerates its ability to improve design, production, quality, and speed. The company mentions that for 60 years, aerospace manufacturing has relied on large factories, fixed tooling, complex supply chains, and extensive manual labor to build costly rockets comprised of 100,000+ parts in 2 years or longer.
In addition to the company’s Stargate printers, they recently announced the next generation of this system. Specifically, on October 24th, Relativity unveiled the latest iteration of its first-of-its-kind proprietary manufacturing platform, Stargate 4th Generation metal 3D printers. These printers will underpin both the development and rate production of Terran R, Relativity’s fully reusable, 3D printed rocket that will be capable of launching 20,000 kg to low Earth orbit (LEO). The newest Stargate printer technology defies traditional printing constraints by moving horizontally as it feeds multiple wires into a single print head to print orbital rockets. Relativity is developing customized software and machine learning techniques to allow these printers to print more complex and significantly larger metal products, with improved print speed and reliability. Stargate 4th Generation printers also radically simplify manufacturing supply chains, as they are capable of printing a rocket with 100x fewer parts in a matter of months.
In order to accelerate innovation in the industry, Relativity built its Factory of the Future, the first aerospace platform to automate rocket manufacturing, vertically integrating intelligent robotics, software, and data-driven 3D printing technology. Incorporating Stargate, the world’s largest metal 3D printer with AI-driven controls, our Factory of the Future continuously optimizes production, resulting in greatly compounded quality and time improvements, lower costs, and product designs previously not possible. Relativity is an application-layer 3D printing company that is starting with rockets, and will extend its Factory of the Future to all of aerospace.
As far as the launch site responsible for this upcoming mission, back in early 2019, Relativity was granted a Right of Entry for its own rocket launch facilities at Launch Complex 16 (LC-16) at Cape Canaveral Air Force Station in Florida. The Right of Entry signified the U.S. Air Force’s formal acceptance of Relativity to build and conduct launch operations from Cape Canaveral Air Force Station. This is the first and only direct agreement the U.S. Air Force has completed with a venture-backed orbital launch company at LC-16, and includes on-site vehicle integration and payload processing, with the opportunity to extend to an exclusive 20-year term. Relativity joins SpaceX, ULA, and Blue Origin as only the 4th company with a major operational orbital launch site at Cape Canaveral.
The LC-16 launch facility was historically used for Titan missile launches, the Apollo moon program, the Gemini program, and Pershing missile launches. Launch infrastructure is in limited supply, and LC-16 is one of the few major launch facilities still available at Cape Canaveral. LC-16 is capable of supporting Relativity’s rocket, Terran 1, the first and only fully 3D printed rocket in the world, as well as the company’s future expansions in payload capacity, and comes with substantial existing infrastructure and operational history. Additionally, Relativity has hired a team made up of former senior leadership personnel from top space companies, who have executed over 158 successful launches at Cape Canaveral. This combination will enable Relativity to more quickly build and operate a rocket launch facility. All of which led to this milestone moment for the company and the final tests necessary before history is made. If successful, this launch could have a significant impact on how rockets are manufactured within the industry.
Conclusion
Relativity Space has been working toward Terran 1’s first launch for close to a decade. In the last few months especially we have watched very consistent updates as the first Terran 1 launch vehicle has been prepared. Just yesterday it was rolled out to the pad where it will complete a few final tests before the maiden flight. We will have to wait and see how it progresses and the impact it has on the space industry.