
Relativity Space Has Installed Stage 1 Onto LC-16
Relativity Space has been working in overdrive in preparation for the first orbital test flight of Terran 1. As you can imagine, the work and tests necessary before a flight attempt are very significant. Not long ago we watched Relativity test both the first and second stage of the rocket expected to fly very soon.
By now heading towards late June, the company has moved the first stage and installed it onto LC-16 in Cape Canaveral Florida. Thankfully, Relativity and CEO Tim Ellis have kept us updated on the progress towards this launch. While very exciting, it’s important to remember that a first test flight of a new rocket is often not successful. This being said, it offers the company a lot of invaluable information and more.
Relativity will not only be testing the rocket itself for the first time, but this will also be the first time they launch a 3D printed rocket headed for orbit. This will likely have an impact on the space industry as companies and agencies work to speed up and lower costs for rocket development. Here I will go more in-depth into some of the recent updates and what to expect in the coming months.
Recent Updates
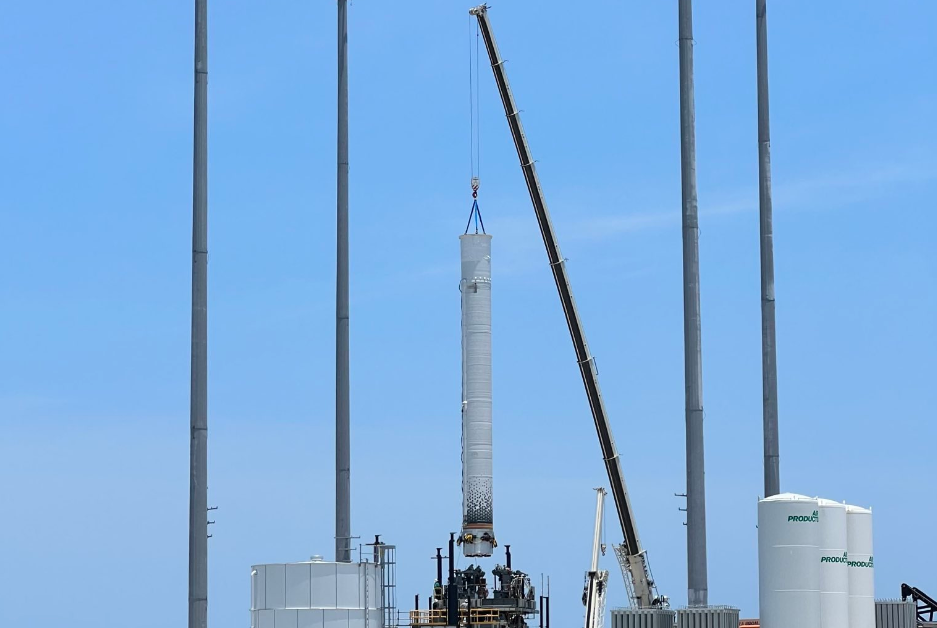
Almost every day Relativity Space is providing some form of update on the launch and current state of Terran 1 at LC-16. Starting on June 20th, Relativity tweeted saying, “Nothing but blue skies and one good-looking launchpad.” This included a photo of LC-16 at Cape Canaveral Florida. Over the past few weeks, the company finished some of the tests of both the first and second stage. From here they transported both stages to the launch pad in preparation for launch. The same day Relativity tweeted again this time mentioning, “Happy #Monday! Check out these awesome photos from when Stage 2 arrived at Cape Canaveral, FL, and our world-class team immediately went to work. Here you could see both the stage arrival as mentioned and also work on an engine. Its been very clear from the consistent updates that everyone at Relativity is working in overdrive trying to launch Terran 1 for the first time. Only a few days later on June 22nd, Relativity retweeted pointing out a, “Close-up of the Aeon Vac engine at the business end of @RelativitySpace’s Terran 1, stage 2. This picture shows a very high quality image of a lot of the plumbing and top of the engine.
This engine will play an important role and will also truly be put to the test. Relativity’s engines, Aeon 1, Aeon R and Aeon Vac, are 3D-printed, intended to enhance mission reliability by reducing part count in engine combustion chambers, igniters, turbopumps, reaction control thrusters, and vehicle pressurization systems. The company mentions that all Aeon engines use propellants of the future, liquid oxygen plus liquid natural gas, which are not only one of the best for rocket propulsion, but also the easiest to eventually make on Mars. To date, Aeon has completed 500+ test fires. Multiple of which happened not long ago as the company prepared. The next day on June 23rd, Relativity tweeted again this time saying, “Terran 1, Flight 2 flight articles are well under way and looking mighty stellar at our #factoryofthefuture in Long Beach, CA.” This included multiple photos of the future stages of the next Terran 1. It’s exciting that the company is continuing to work on the next project and already getting ready for the next launch. Finally, later that same day, Relativity tweeted one final time mentioning, “Sensational angle of stage 1 being installed onto the MDC mount at LC-16 in Cape Canaveral, FL.” At this point, the company is closer than ever to this significant test. The company has a few important tests left, however, if everything goes according to plan, we can expect to see a launch not long from now.
Terran 1 & More
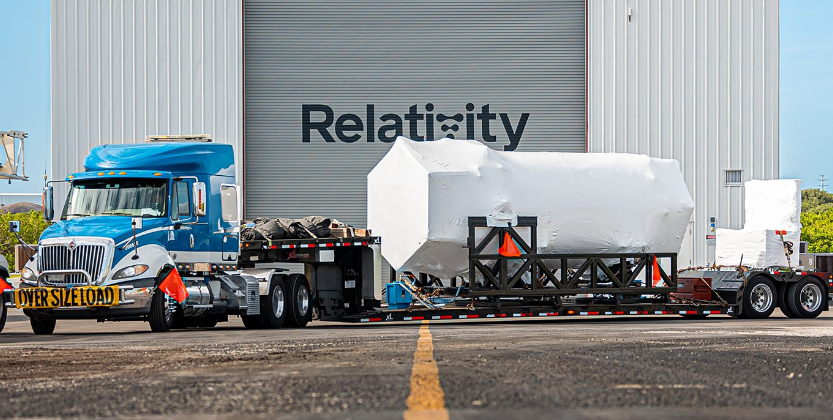
One of the most fascinating parts about Relativity is the combination of the company’s unique manufacturing process and its goals/plans for the future. Together they create very challenging but inspiring opportunities for the company and the rest of the space industry. Relativity Space is trying to offer advanced manufacturing and launch service capabilities that disrupt the economics of space. Their 3D printing platform vertically integrates artificial intelligence, robotics and patented autonomous manufacturing technology to build the world’s first entirely 3D printed rocket, Terran 1, from raw material to flight in less than 60 days. While quite ambitious, the company is very confident in its ability and what 3D printing can offer. As a next-generation space company, one of Relativity’s goals is to improve connectivity and security across the planet by inserting satellites into orbit with industry-defining lead time, flexibility, and cost.
Terran 1 is entirely designed, built, and flown by Relativity in American-based facilities, and offers a 3-meter fairing with a mass-to-orbit capability of up to 1,500 kg to low Earth orbit for dedicated, multi-manifest, and rideshare missions. Terran 1 is attempting to serve a wide range of inclinations from Relativity’s launch sites at Cape Canaveral Air Force Station and Vandenberg Air Force Base. One unique feature Relativity offers are custom, 3D printed payload adapter solutions using the same design, production, and test capabilities as are used for the Terran 1 vehicle itself. Relativity’s design and production approach offers increased reliability thanks to fewer parts than traditional rockets which enables accelerated production rates while also significantly reducing opportunities for human error in the assembly process. As of right now, Relativity is trying to establish a new standard for quality, speed, and cost in aerospace production. Its engineering and production teams are tightly coupled for continuous improvement in quality and printing capabilities.
Taking a closer look at manufacturing, Relativity utilizes two types of 3D printing to produce over 90% of the dry mass of Terran 1. Relativity’s large format, proprietary 3D printing process, known as Stargate, is used to produce primary and secondary structures for Terran 1 from a proprietary aluminum alloy – with printing, inspection, and the little post-processing required occurring all in a single print cell. Stargate can currently print structures up to 3.4 meters (11 feet) diameter by 7.6 meters (25 feet) tall, the world’s largest metallic printed parts. Relativity uses direct to-metal laser sintering (DMLS) to produce geometrically small, high fidelity components for Terran 1. Each Stargate printer includes real time in-situ monitoring, inspection, and post-processing capabilities, which take place layer-by-layer rather than post-print. Video, audio, and thermal sensors enable closed-loop control and in process inspection to mitigate flaw formation. Computer vision and machine learning bring state-of-the-art control techniques to a highly nonlinear, highly coupled process. Relativity evaluates coupons from each print (Stargate prints and DMLS) for traceability, and uses in-house materials and processing capabilities for inspection and characterization of mechanical properties (e.g. microstructure, hardness testing, microscopy). Relativity highlights that through this approach, its technology immediately identifies, characterizes, and adapts to any print anomalies, resulting in fully verifiable printed products. The result is an evolvable aerospace production line using data-driven learning to track and improve every aspect of rocket manufacturing. By fully leveraging 3D printing techniques, Relativity’s team greatly simplifies the supply chain, reduces part count by 100 times across Terran 1’s structure and engines, significantly reduces lead times and overhead, and increases overall vehicle system reliability.
One of the next most fascinating components of the rocket utilizing these manufacturing features are the engines. As partially mentioned prior, Relativity’s Aeon engines are designed, assembled and tested in house. Except for the second-stage nozzle extension, each of Terran 1’s 10 engines is based on a common design, enabling simplified and repeatable manufacturing and acceptance testing. Aeon engines are fueled by liquid natural gas and liquid oxygen and operate using the gas generator engine cycle. Each engine uses two turbopump assemblies for thrust and mixture ratio control: one for liquid natural gas and one for liquid oxygen. The thrust chamber is regeneratively cooled with liquid natural gas, which is then injected into the main combustion chamber and burned with liquid oxygen to produce the required thrust. Not long from now all 10 of these engines will be put to the test and attempt to lift Terran 1 off the ground and into orbit.
Conclusion
For a long time now Relativity Space has been working towards this exact launch. The first orbital test flight of a rocket is a monumental moment that involves a lot of challenges and excitement. While the first launch usually does not go 100% to plan, it is practically guaranteed to provide invaluable information to the company as they work towards the next Terran 1 launch and beyond. We will have to wait and see how it progresses and the impact it has on the space industry.
Relativity Space is leading the way into the next generation of interplanetary travel and has produced two great rockets, the Terran1 and the Terran R, to achieve that goal. It’s going to be great to watch the launch of Terran 1 and see how it’s Rocket science dynamics and excellent 3-D printing technology work together to produce a great rock that will be cutting edge technology for the 21st-century in space travel.