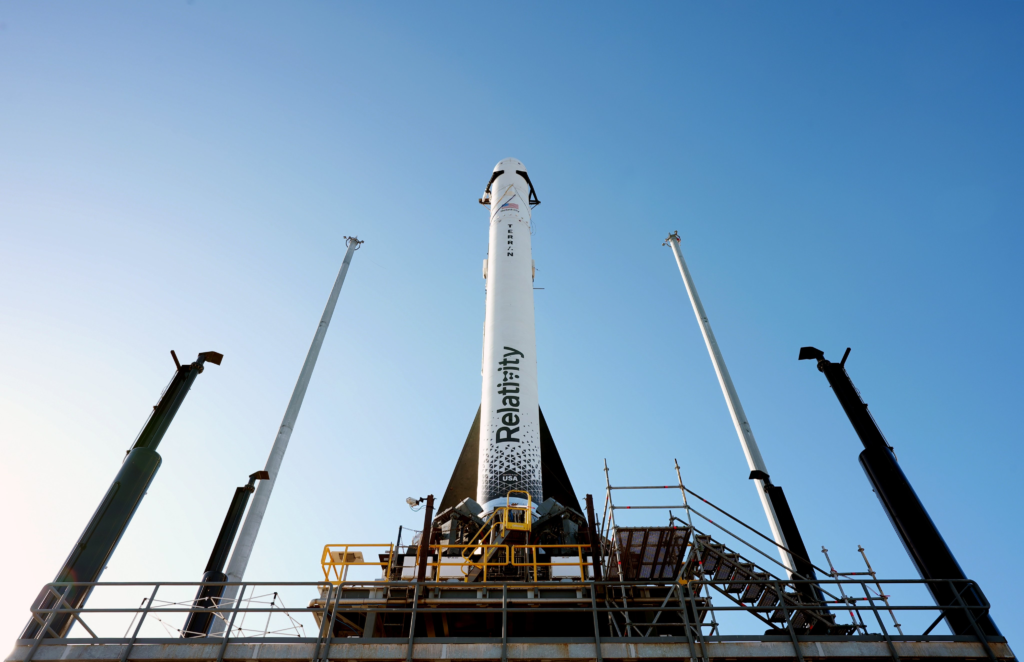
Relativity Just Set A Launch Date For Terran 1’s First Flight
After multiple delays due to various reasons, Relativity Space has finally set an exact launch date for Terran 1’s first test flight. The fully 3D printed small lift launch vehicle has been going through a host of different tests for quite a few months now. All of which in preparation for a historic moment not only for Relativity Space but also for the space industry as a whole.
Just days ago the company announced that Terran 1’s first launch is set to happen just over a week away on March 8th, 2023. The mission, named “GLHF” (Good Luck, Have Fun), will take place at Launch Complex 16 in Cape Canaveral. Between then and now, there are only a couple final tests necessary to make sure everything is ready.
Assuming these results are promising and Relativity is confident, the Terran 1 test article will lift off. No matter the company, initial test flights of new rockets often end with an explosion, a theme Relativity is trying to avoid. Here I will go more in-depth into this upcoming mission, the official launch date, what to expect in the coming weeks, and more.
March 8th
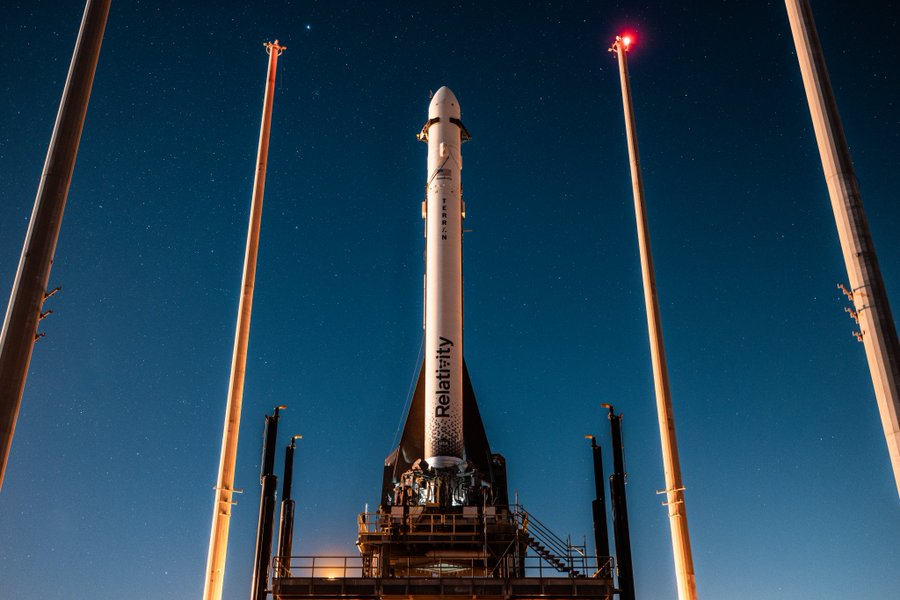
We are officially less than 11 days away from Relativity’s first launch attempt with Terran 1. Only days ago the company tweeted saying, “You’ve asked, “Wen Launch?” and to that, we say… Catch us live at Launch Complex 16 in Cape Canaveral, FL on March 8, 2023 to watch the world’s first 3D printed rocket fly.” Officially, the launch window opens at 11:00 am UTC.
In the past couple of weeks, Relativity has been completing the final prep necessary for this mission. This includes securing the launch license, confirming the specific launch window, and a lot of tests. Specifically, on the 23rd they tweeted mentioning, “Solid data from recent wet dress rehearsals, and extensive Stage 1 + 2 testing, have given us the confidence to move forward with launch. We’re ready to #Sendit” What’s interesting about this approach is that Relativity will not be attempting a static fire before the launch window. In a quote, they said ” we have burned down risk significantly and have the data and insights we’ll need” from previous tests for the upcoming orbital launch attempt.
This launch of Terran 1 is the first orbital attempt by Relativity and will not include a customer payload. At the top of the rocket, the Terran 1 test article features a small nosecone rather than a typical fairing. The typical fairing is 6.8 m (22.2 ft) x 3 m (10 ft) in diameter. In terms of this first mission, there are 3 very significant events we can hope to see. This includes the first 3D printed orbital rocket launch, Relativity’s first launch as a company, and the first orbital launch attempt with this specific propellant combination. As a two-stage, 110ft. tall, 7.5 ft. wide, expendable rocket, Terran 1 is the largest 3D printed object to exist and to attempt orbital flight. Working towards its goal of being 95% 3D printed, Relativity’s first Terran 1 vehicle is 85% 3D printed by mass. Terran 1 has nine Aeon engines on its first stage, and one Aeon Vac on its second stage. Similar to its structure, all Relativity engines are entirely 3D printed, and use liquid oxygen (LOX) and liquid natural gas (LNG), which are not only one of the best for rocket propulsion, but also for reusability, and the easiest to eventually transition to methane on Mars.
Throughout the entire space industry, we are seeing a massive shift toward this propellant combination. A few other important launch vehicles are also months away from a first test flight with this mixture including Vulcan, Starship, and many more.
Focusing back on the upcoming launch, even the launch site will be put to the test for the first time. Before Relativity was competitively awarded the site in 2019, LC-16 was used by the US Air Force for Titan I, Titan II, and Pershing missile launches, and briefly by NASA for Gemini crew processing and static test firing of the Apollo Service Module’s propulsion engine. Relativity is the first and only venture-backed company with a Right of Entry directly with the U.S. Air Force at historic Launch Complex 16. After getting access to the site, Relativity began working hard to transform it into a modern launch complex capable of supporting its ambitious goals. This includes various integration facilities, launch mount, and tower, just to name a few. Something we can look forward to seeing in action for the first time in just over one week.
The Future of Rockets
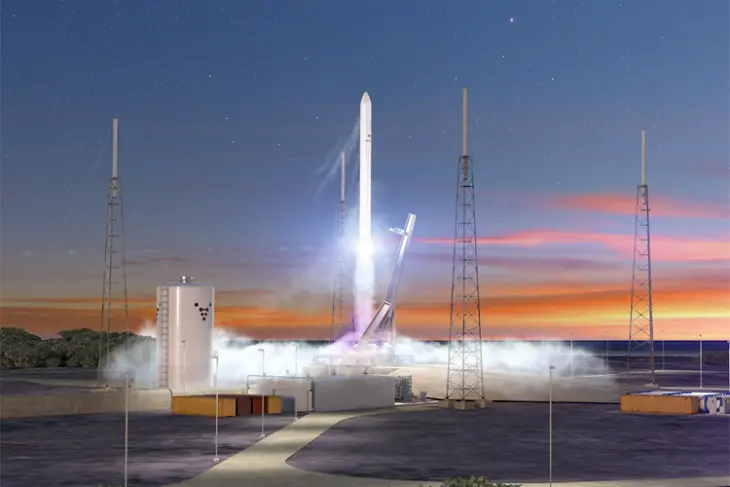
Now that we know more about Terran 1’s recent progress and its upcoming flight, we can take a closer look at the chance of delays, and what makes this rocket so unique. While this launch has been pushed back a lot due to various delays, at this point it seems very likely it will lift off or at least attempt to on the 8th. This mainly comes down to the fact that all the big tests are out of the way such as the wet dress rehearsal and static fire. These are the main processes that can reveal different issues or discrepancies that cause Relativity to delay the mission. In the next week, the company will still be busy but the main preparation has already been completed with flying colors.
In terms of the rocket itself, the results of this mission will have a notable impact on the rest of the industry and what’s possible. Starting at the bottom, the Terran 1 first stage assembly consists of three main components: the thrust structure, the Stage 1 tank, and the interstage. The tanks share a common dome and airframe that is integrally printed as monolithic sections, where a horizontal welding process integrates Stage 1 segments together to achieve the final stage structure. A transfer tube carries LOX through the center of the LNG tank to the engines. Nine Aeon-1 engines power the first stage with up to 23,000 lbf thrust per engine at sea level, for a total thrust of up to 207,000 lbf at liftoff. Terran 1 autogenously pressurizes the tanks with gaseous natural gas and gaseous oxygen via heat exchangers integrated into the Aeon-1 engines, eliminating the need for a separate pressurization system and avoiding the use of helium on the vehicle entirely. Electromechanical actuators gimbal the outer 8 engines, providing thrust vector control. The stage separation system is located at the forward end of the interstage and interfaces with the second stage.
The Terran 1 second stage consists of a monolithic printed tank with an integral common dome, payload attach fitting, and separable fairing. A single Aeon Vacuum engine powers the second stage with up to 28,300 lbf-vac using a fixed 165:1 expansion nozzle and is capable of multiple restarts including provisions for a deorbit burn. Similar to Stage 1, a heat exchanger on the AeonVac engine generates gaseous natural gas and gaseous oxygen that pressurize their respective tanks autogenously. Stage 2’s payload controller offers separation initiation, separation detection, ethernet, and serial in-flight payload telemetry channels. Pitch and yaw control is provided by electro-mechanical thrust vector control actuators affixed to the Aeon Vacuum engine. Roll control and pointing are performed using cold nitrogen gas reaction control thrusters located near the aft end.
On both the first and second stage, Aeon engines are fueled by liquid natural gas and liquid oxygen and operate using the gas generator engine cycle. Each engine uses two turbopump assemblies for thrust and mixture ratio control: one for liquid natural gas and one for liquid oxygen. The thrust chamber is regeneratively cooled with liquid natural gas, which is then injected into the main combustion chamber and burned with liquid oxygen to produce the required thrust.
Looking at performance, Terran 1 provides direct-injection and multi-burn launch services to a variety of target orbits, delivering as much as 1,500 kg into orbit. Relativity selects which launch site supports each mission based on customer-specified orbit requirements. Terran 1 is built for high injection accuracy, and its standard mission design includes trajectory and separation analyses as well as collision avoidance maneuvers and deorbit as required. Typical circular mission design includes four burns: Stage 1 burn through main engine cutoff; Stage 2 burn through stage engine cutoff followed by a coast to apogee; Stage 2 burn to circularize; and Stage 2 burn to deorbit.
As partially mentioned prior, what’s most exciting is the fact that this first Terran 1 test article is 85% 3D printed by mass. Relativity developed multiple proprietary alloys custom designed for 3D printing to meet mission-critical performance. Parts are inspected during and after printing to ensure they meet the highest standards of uniformity and quality. To accelerate innovation in the industry, Relativity built its Factory of the Future, the first aerospace platform to automate rocket manufacturing, vertically integrating intelligent robotics, software, and data-driven 3D printing technology. Incorporating Stargate, the world’s largest metal 3D printer with AI-driven controls, their Factory of the Future continuously optimizes production, resulting in greatly compounded quality and time improvements, lower costs, and product designs previously not possible. This exact system printed Terran 1’s main structure and the majority of its components.
Conclusion
Relativity is just over 10 days away from the biggest moment in the company’s history. Here they will attempt to launch the Terran 1. This will be the first 3D printed orbital rocket attempt, use of LOX and LNG, and general mission for the company. While initial launches have a track record within the industry of not going well, Relativity is doing everything it its power to make this mission a success. We will have to wait and see how it progresses and the impact it has on the space industry.