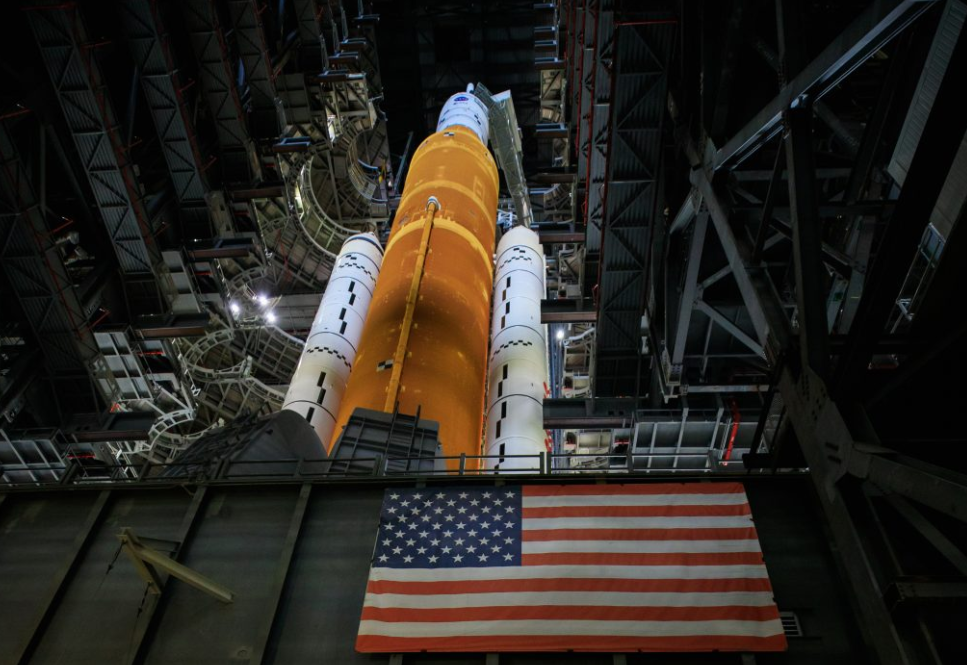
NASA Returns The Space Launch System To The Pad After Repairs
While it has been a long time since humans stepped foot on the Moon, NASA with the help of other agencies and companies is planning on changing that not long from now. Artemis consists of many different key pieces that all need to work together in order for the mission to be a success. The Space Launch System is especially important as it plans to transport both crew and cargo to and from the Moon.
Over the past few months, many of us have kept track of this rocket’s progress during the wet dress rehearsal. What was initially planned to be a multiple day test, has since turned into a multiple month process. This being said, NASA has worked to fix the issues found, and just rolled the launch system back to the pad to finish the test.
Once complete, the next step will be launching the Space Launch System for the first time apart of Artemis 1. This test will be vital for the future of Artemis and returning humans to the surface of the Moon. Here I will go more in-depth into the recent repairs, rollout back to the pad, and what to expect in the future regarding SLS.
Recent News
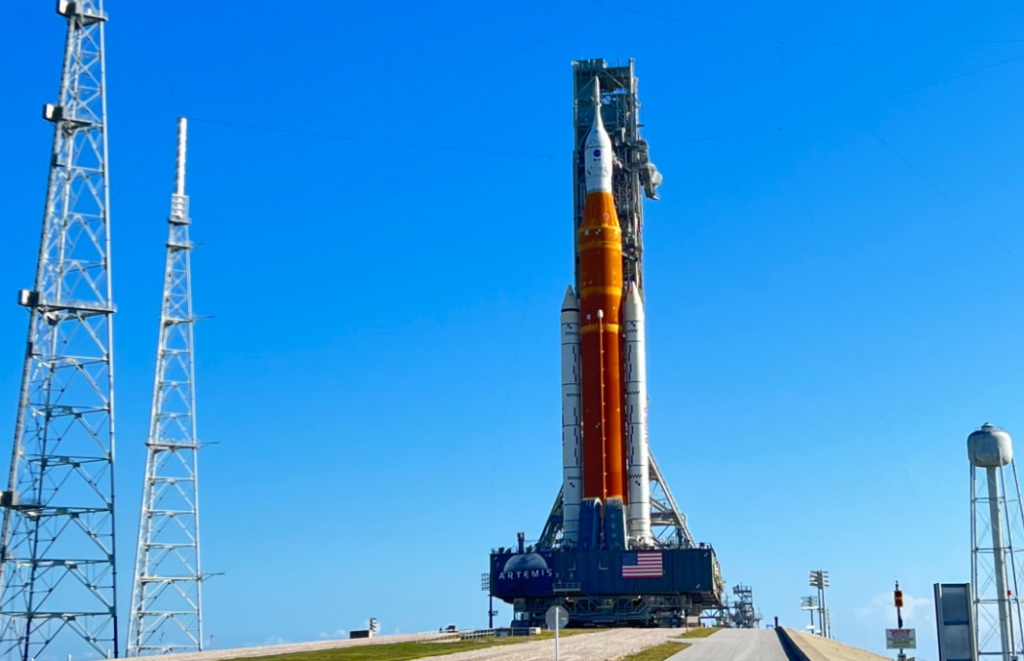
Just a few days ago, engineers and technicians at NASA’s Kennedy Space Center conducted final preparations for the roll out of the Space Launch System Moon rocket and Orion spacecraft. NASA pointed out that during this time in the VAB, teams successfully completed all major planned objectives identified during the previous wet dress rehearsal attempts, as well as some forward work previously planned for after the tanking test. This included assessing the liquid hydrogen system leak at the tail service mast umbilical, replacing the interim cryogenic propulsion stage (ICPS) gaseous helium system check valve and support hardware, and modifying the ICPS umbilical purge boots. The addition of hazardous gas detectors above the upper stage allows for additional visibility into any potential leaks during cryogenic operations. At this point, the removal of the final set of platforms was complete and the crawler transporter sat underneath the massive rocket, spacecraft, and mobile launcher. Here NASA tweeted saying, “All the work platforms are retracted in High Bay 3 of the Vehicle Assembly Building at @NASAKennedy. The SLS and @NASA_Orion atop the mobile launcher will soon be headed to the launch pad on the crawler-transporter for a wet dress rehearsal test.”
A few days later, at approximately 12:10 a.m. EDT on June 6th, NASA’s Artemis I Moon rocket began its journey from Kennedy Space Center’s Vehicle Assembly Building (VAB). Poised atop its crawler transporter, the Space Launch System rocket and Orion spacecraft will make the 4-mile journey to launch pad 39B to undergo the next wet dress rehearsal test attempt. At approximately 8:20 a.m. EDT, SLS arrived at the spaceport’s launch complex 39B after an eight-hour journey ahead of the next wet dress rehearsal attempt. Teams will work to secure the Space Launch System rocket and Orion spacecraft and mobile launcher to ground support equipment at the launch pad and ensure that the rocket is in a safe configuration in preparation for the upcoming tanking test. The upcoming rehearsal will run the Artemis I launch team through operations to load propellant into the rocket’s tanks, conduct a full launch countdown, demonstrate the ability to recycle the countdown clock, and also drain the tanks to give them an opportunity to practice the timelines and procedures they will use for launch. Teams will start by activating the facilities needed for launch and formally beginning the countdown sequence. Team will staff the Launch Control Center at Kennedy and connect with staff in the Mission Control Center at NASA’s Johnson Space Center in Houston, the Space Force Eastern Range, and the SLS Engineering Support Center at the agency’s Marshall Space Flight Center in Huntsville, Alabama. Launch controllers will power on different rocket and spacecraft systems, along with ground support equipment. Teams will then load more than 700,000 gallons of cryogenic, or super cold, propellants including liquid hydrogen and liquid oxygen into the rocket at the launch pad on the mobile launcher according to the detailed timeline they will use on the actual launch day. They will practice every phase of the countdown, including weather briefings, pre-planned holds in the countdown, conditioning and replenishing the propellants as needed, and validation checks.
SLS Complications
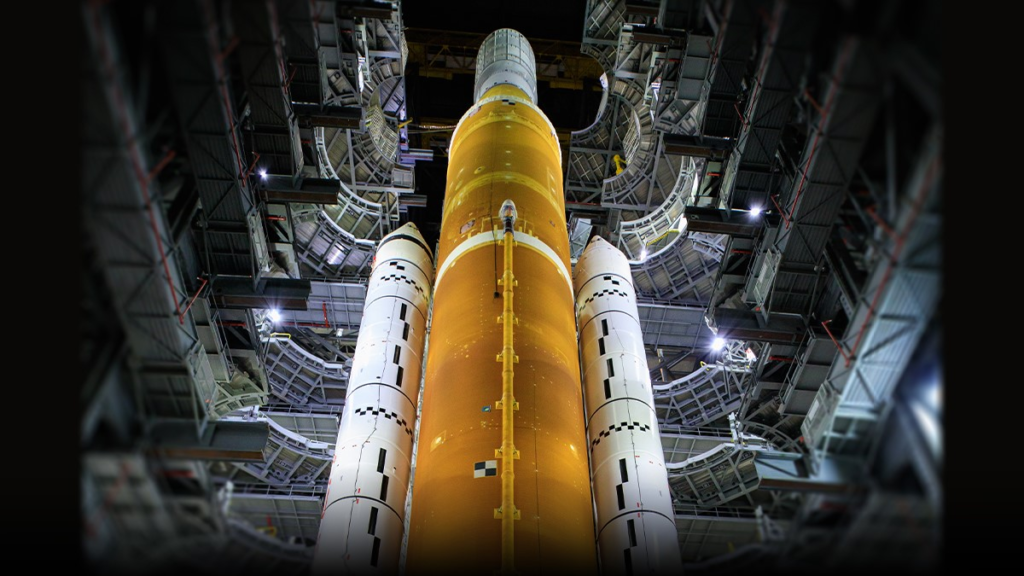
Now that the Space Launch System has been repaired and is about to attempt the wet dress rehearsal again, we can take a closer look at what exactly stopped its progress and forced the return to the VAB. There were three main issues that arose during prior tests that NASA had to work on. The first was revealed in early April. Specifically, engineers identified a helium check valve that was not functioning as expected, requiring changes to ensure the safety of the flight hardware. Helium is used for several different operations, including purging the engine, or clearing the lines, prior to loading propellants during tanking, as well as draining propellant. A check valve is a type of valve that allows liquid or gas to flow in a particular direction and prevents backflow. The helium check valve is about three inches long and prevents the helium from flowing back out of the rocket. Eventually in May, engineers inspected the valve and found a small piece of rubber that prevented the valve from sealing correctly. Teams then looked at possible sources of the debris, but did not see any issues with the valve itself, and continued on from there.
The next issue had to do with hydrogen leaks on the tail service mast umbilical. Specifically, engineers performed tests to address a hydrogen leak on one of two tail service mast umbilicals between the mobile launcher and the rocket. These umbilicals provide liquid oxygen and liquid hydrogen propellants, as well as electrical connections, from the mobile launcher to the rocket’s core stage during the launch countdown. Teams conducted leak checks on all the joints and tightened several flange bolts, or fasteners that act as a washer to increase the compression strength, that can loosen over time and were the most likely source of the leak. Teams re-tightened the flange bolts on the liquid hydrogen, liquid oxygen, and core stage intertank umbilicals. Engineers have not detected leaks in subsequent testing at ambient air temperature, and will continue to monitor for leaks in the future.
After re-tightening the flange bolts on the tail service mast umbilical lines to address a hydrogen leak identified during the previous wet dress rehearsal, engineers determined the seals on the bolts are no longer relaxing, and the system should remain tightly sealed during propellant loading. As a precaution, teams also moved the location of a heavy cantilevered filter on the tail service mast umbilical, which filters out any contaminants in the gaseous helium – a purge gas – that travels through the drain assist purge line. Engineers did not identify any leaks at its previous location, but relocating the filter will ensure it does not contribute to future leaks. Engineers conducted additional leak checks and have not detected any leaks at ambient air temperature. Additionally, after replacing the helium check valve on the interim cryogenic propulsion stage (ICPS), engineers found a damaged rubber O-ring seal in the flight side of the quick disconnect – the area that separates the ICPS from the mobile launcher during launch. The O-ring came loose and entered the valve, preventing the valve from sealing correctly. Teams removed the flight and ground side of the quick disconnect system and replaced support hardware that was downstream of the check valve. Lastly, the supplier that provides gaseous nitrogen for operations during tanking worked to upgrade its facility to meet the requirements for the next wet dress rehearsal attempt and the Artemis I launch. Not long after this initial announcement, NASA pointed out that the supplier for gaseous nitrogen completed upgrades to its facility to meet the requirements for the next wet dress rehearsal attempt. Engineers will test the system soon to ensure it’s ready to support tanking operations. During wet dress rehearsal and launch, teams pump gaseous nitrogen into dry structures to protect avionics during propellant loading. NASA will review data from the rehearsal before setting a specific target launch date for the Artemis I launch. The first in a series of increasingly complex missions, Artemis I will provide a foundation for human deep space exploration and demonstrate our commitment and capability to extend human existence to the Moon and beyond prior to the first flight with crew on Artemis II.
Conclusion
Since the beginning of April, we have watched NASA work on the Space Launch System and wet dress rehearsal. While this test was intended to only take a few days, it has now exceeded multiple months. However, it’s important to point out that NASA should fix and find any errors now before more vital tests like Artemis 1 and beyond. We will have to wait and see how it progresses and the impact it has on the space industry.