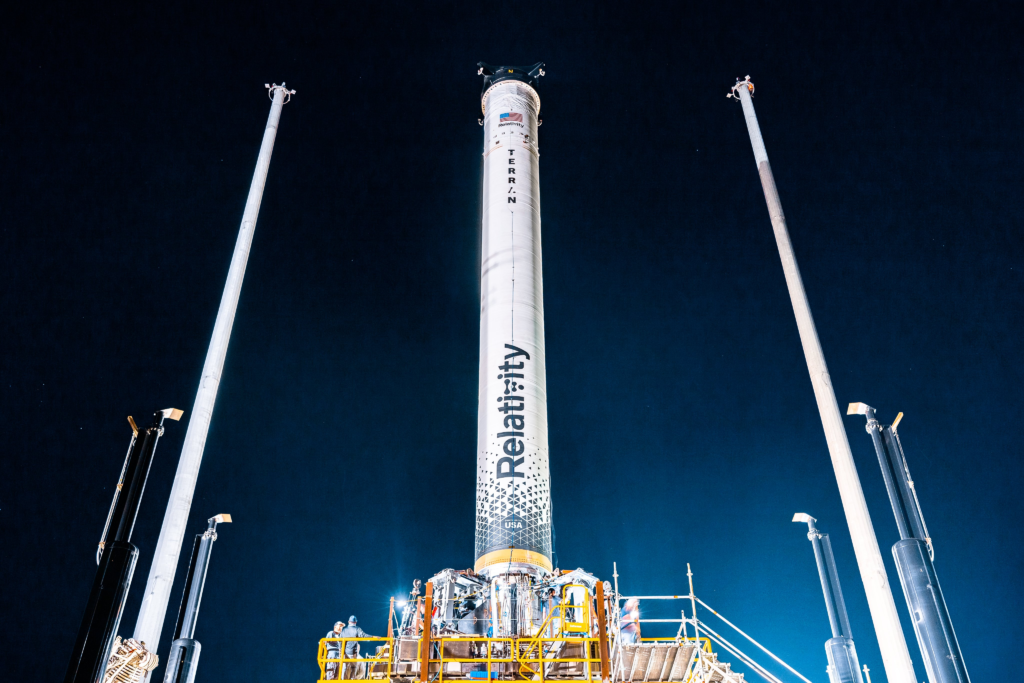
More Updates As Relativity Gets Closer To First Orbital Test Flight
Right now the space industry is extremely busy with different companies and agencies all working on new and ambitious projects. Relativity is no exception with recent news on Terran R contracts and the more present progress towards the company’s first orbital test flight. This will happen with Relativity’s fully 3D printed rocket Terran 1.
Over the last few weeks, Relativity and CEO Tim Ellis have kept us updated on exactly what’s going on in preparation for this milestone. After both stages arrived at the launch complex in Florida, they began mounting the first stage for upcoming tests. Once complete, we can expect only a few tests before the official first launch attempt of the rocket.
A first orbital launch attempt is both a big deal and an immensely difficult task. It is one thing to build a rocket but reaching orbit is an entirely different challenge. This has been shown by many different companies throughout the space industry. Here I will go more in-depth into some of the recent progress Relativity has made, what to expect in the coming weeks, and more.
Recent Updates
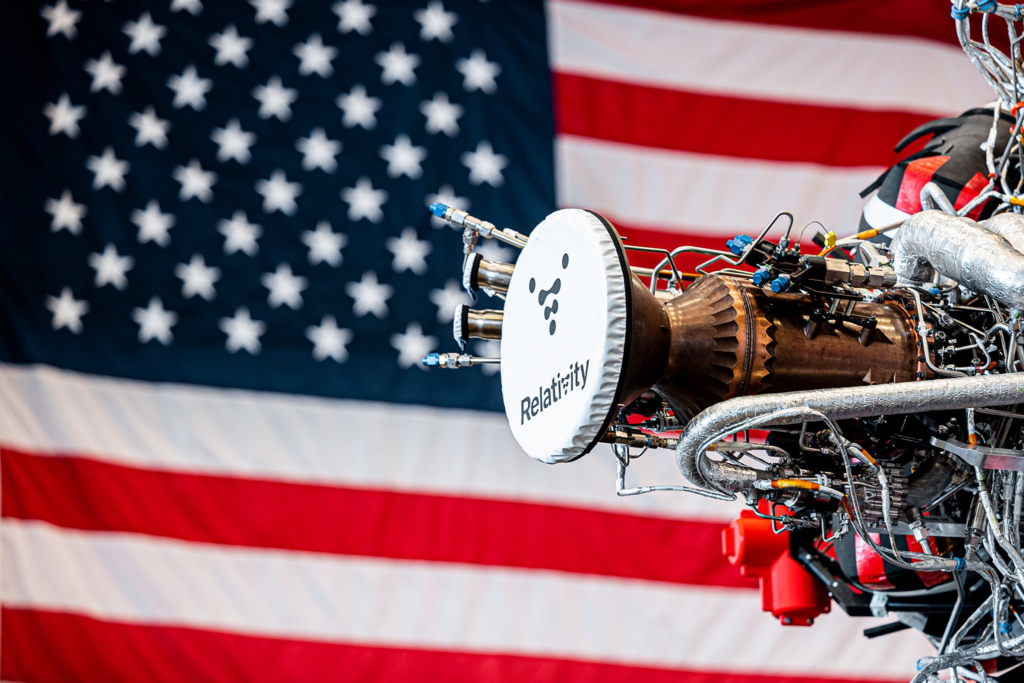
The most recent updates began on June 28th when Relativity tweeted saying, “All 9 Aeon engines up close just before being lifted onto the stand.” Here you could see the bottom of the first stage and the engines expected to provide thrust not long from now. Relativity’s engines, Aeon 1, Aeon R and Aeon Vac, are 3D-printed, with the goal of enhancing mission reliability by reducing part count in engine combustion chambers, igniters, turbopumps, reaction control thrusters, and vehicle pressurization systems. On that same day, CEO Tim Ellis provided a more in depth update mentioning, “First propellant loading and stage pneumatic proof successfully complete last night as we work to stage hot-fire testing.” Only days before these tweets we saw the first stage mounted onto the launch pad. All of which in preparation for these tests and eventually the launch itself.
The next day on the 29th, Tim Ellis tweeted again this time pointing out, “Prop cold-flow test day.” This included an image of the control room in preparation for continued testing of the stage. Next, on July 4th, Relativity showed off a close up of the Aeon engine. They tweeted saying, “red, white and boosted, Wishing you a happy 4th from LC-16.” Here you could see a detailed image of the engine in front of the American flag. Finally, only a few days ago on the 5th, Relativity tweeted one last time mentioning, “Night and day. Swipe to see some new views of Stage 1 on the pad (including the load head as we get ready for testing!)” This included two images of the stage on the pad looking ready for the upcoming orbital test flight. The location and launch site is LC-16 in Cape Canaveral Florida. Back in 2019 Relativity announced that it was granted a Right of Entry for its own rocket launch facilities at Launch Complex 16 (LC-16) at Cape Canaveral Air Force Station in Florida by The 45th Space Wing of the United States Air Force. This will also be the site of the orbital test flight, and future Terran R operations.
Terran 1 First Launch
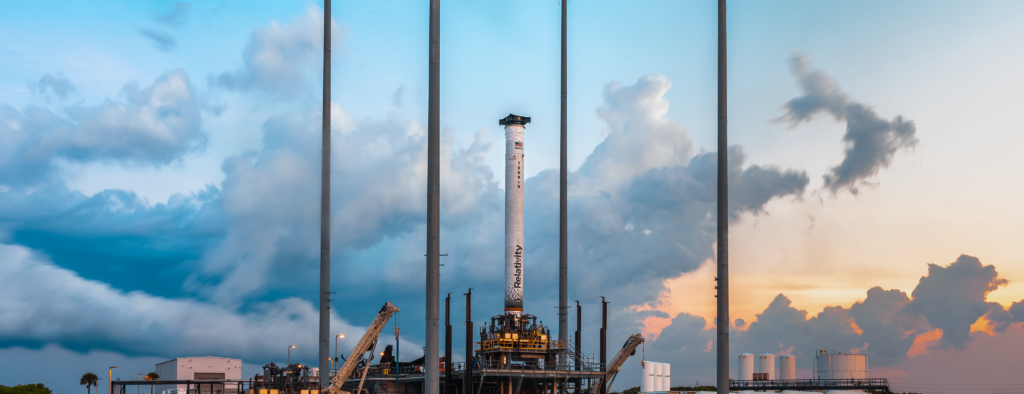
Now that we know more about the progress Relativity is making, we can take a closer look at the rocket and launch complex that will be put to test not long from now. As partially mentioned prior, Relativity received a right of entry in 2019 for launch complex 16. The Right of Entry signifies the U.S. Air Force’s formal acceptance of Relativity to build and conduct launch operations from Cape Canaveral Air Force Station. This is the first and only direct agreement the U.S. Air Force has completed with a venture-backed orbital launch company at LC-16, and includes on-site vehicle integration and payload processing, with the opportunity to extend to an exclusive 20-year term. At the time, Relativity joined SpaceX, ULA, and Blue Origin as only the 4th company with a major operational orbital launch site at Cape Canaveral.
The LC-16 launch facility was historically used for Titan missile launches, the Apollo moon program, the Gemini program, and Pershing missile launches. Launch infrastructure is in limited supply, and LC-16 is one of the few major launch facilities still available at Cape Canaveral. LC-16 is capable of supporting Relativity’s rocket, Terran 1, as well as the company’s future expansions in payload capacity, and comes with substantial existing infrastructure and operational history. Additionally, Relativity has hired a team made up of former senior leadership personnel from top space companies, who have executed over 158 successful launches at Cape Canaveral. This combination has enabled Relativity to more quickly build and operate a rocket launch facility. Over the past few years since receiving access to the pad, Relativity has stayed busy and worked to transition it for their needs and specific rocket. Now in July of 2022, the first stage of Terran 1 is mounted to the pad and an orbital test flight is just around the corner.
Looking at the rocket itself, Relativity describes Terran 1 as a next generation launch vehicle. Terran 1 is designed for the future of constellation deployment and resupply. Its software-driven architecture is capable of accommodating satellite customers’ evolving needs, while also providing the most agile and affordable launch service on the market. Designed and printed in the USA, The company is confident Terran 1 is one of the most innovative products to emerge from the aerospace manufacturing industry since the dawn of privatization of space 20 years ago. The Terran 1 vehicle is 35 m in height by 2.3 m in diameter, and uses 10 Aeon engines. Nine Aeon-1 engines on the first stage, and one Aeon Vacuum engine on the second stage. Relativity’s Aeon engines are designed, assembled and tested in house. Except for the second-stage nozzle extension, each of Terran 1’s 10 engines is based on a common design, enabling simplified and repeatable manufacturing and acceptance testing. Aeon engines are fueled by liquid natural gas and liquid oxygen and operate using the gas generator engine cycle. Each engine uses two turbopump assemblies for thrust and mixture ratio control: one for liquid natural gas and one for liquid oxygen. The thrust chamber is regeneratively cooled with liquid natural gas, which is then injected into the main combustion chamber and burned with liquid oxygen to produce the required thrust.
Relativity prints all structures and major engine components using proprietary printable metal alloys, which leads to a dramatically simplified manufacturing process when compared to traditional fabrication methods. This will make it possible to shrink vehicle build and integration timelines down to just 60 days. The payload fairing leads its class in volume at 3 m (10 ft) in diameter by 6.8 m (22.2 ft) with a 986 mm (38.81 in) standard payload interface. Terran 1’s fairing volume accommodates a variety of payload designs and configurations, including dedicated launch for single payloads and constellations as well as multi-manifest and rideshare configurations. Terran 1 is designed for a mission duration of up to 2.5 hours as a standard service. The design of Terran 1 is intended to provide a predictable and controlled launch environment allowing for simplified payload design requirements. Terran 1 can support both industry-standard and custom interfaces, using commercially available adapter and separation hardware in addition to mission-specific designs. Environmental control systems maintain clean, thermally controlled payload environments.
To maximize flexibility, the avionics system includes a bussed, modular infrastructure that makes it possible to rapidly add or subtract components to meet changing vehicle configurations. Relativity designed the avionics system to leverage component and architecture commonality across both stages in order to reduce development time and simplify vehicle operations. They designed vehicle components to be as accessible as possible, allowing them to quickly and unobtrusively make any necessary modifications late in the integration process. The engineering team is considering vehicle reusability in its development roadmap and is making allocations in the current design for a fluid upgrade transition to reusability. Lastly, an autonomous flight termination unit (AFTU) provides safety in-flight by monitoring the flight path throughout the ascent and issuing a thrust termination command in the event of an anomaly. In addition, operational safety on the ground is provided by the inclusion of a hazard power bus and other lockout controls which must be actuated on the ground, independent of vehicle avionics control. All of which will be put to the test very soon.
Conclusion
Relativity has been working towards this first orbital test flight for years. In the past few weeks alone the company has not only delivered both stages to the launch site, but begun mounting and testing the first stage. At this rate, we could expect to see the first orbital test flight in just over a month from now. We will have to wait and see how it progresses and the impact it has on the space industry.