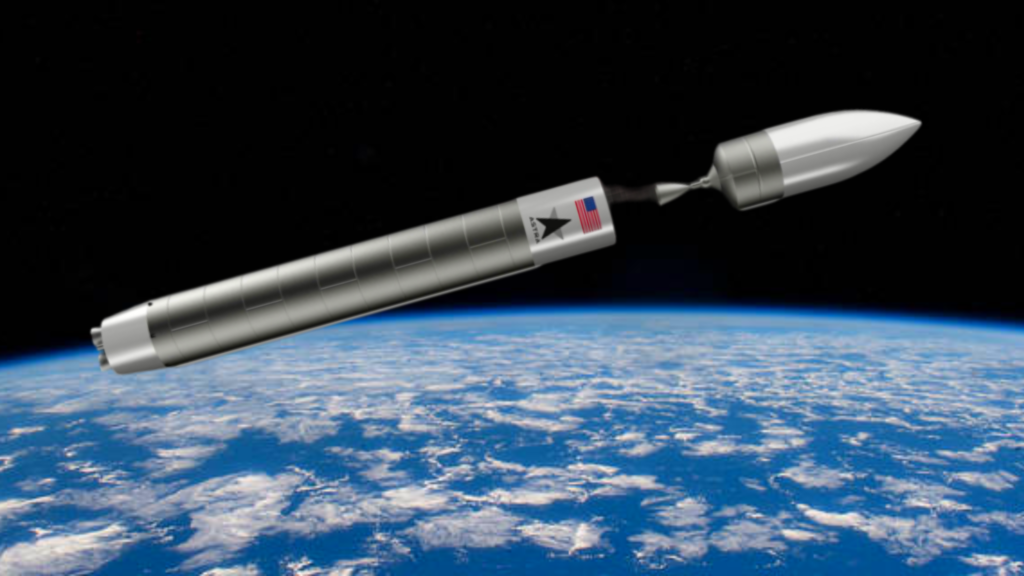
Is Astra Space’s Rocket 4 The Answer To The Company’s Problems?
Astra Space has had a very action packed few years within the space industry. Since being founded not long ago in 2016, they managed to reach orbit faster than any other company before losing this capability. Now in late 2022, they are without a launch vehicle or the ability to reach orbit which is not ideal when you’re a launch company.
This being said, just a few days ago Astra released new information on Rocket 4. This included a full payload user guide of information on the rocket meant to help regain the company’s ability to access space. We even learned more about upcoming launch and test dates that we can expect in 2023. All of which very important if Astra wants to survive within the industry.
While the most recent launch failure had a significant negative impact on the company, they are determined to come back and are excited about what Rocket 4 has to offer. Here I will go more in-depth into the new details of this launch vehicle, what changed from the unsuccessful Rocket 3 line, what to expect in the future, and more.
New Engine & Overview
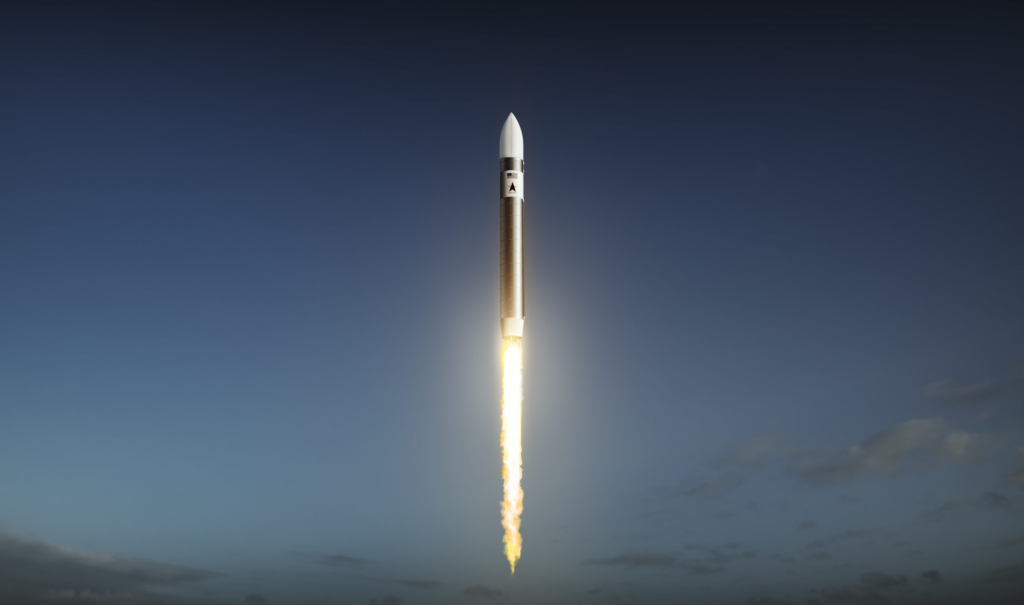
Thankfully, as more and more progress has been made on this new launch vehicle, Astra is finally starting to release more information on what we can expect. Just one week ago on November 16th Astra Space tweeted saying, “The Rocket 4 Payload User’s Guide is now live” This payload users guide includes a large host of information on everything Rocket 4 related.
Starting with the overview, Rocket 4 is an expendable, vertically-launched two-stage LOX/kerosene rocket, optimized for reliability and manufacturability, and built to significantly reduce the cost of dedicated orbital launches. Astra highlights that Rocket 4 is the product of extensive learning that took place during the design, manufacturing, and launch of the prior Rocket 3 series. With much of its architectural heritage coming from the Rocket 3 series, Rocket 4 capitalizes on Astra’s existing flight heritage, while fine-tuning the rocket for improved reliability and manufacturability. Astra has focused on building its rockets using proven and cost-efficient metallic structures, leveraging multidisciplinary production techniques, and eschewing labor-intensive processes such as carbon composite layups.
These techniques allow for rapid manufacturing and reduced production costs, which are realized in lower launch costs to customers. Astra plans to ramp Rocket 4 production in 2024, with the goal of creating increased launch availability by achieving an average weekly launch cadence over the course of the product lifecycle. Looking at some of the past Rocket 3 line launch failures, many of them suffered various problems including engine issues, fairing separation, and more. All of which Astra is trying to eliminate with this new rocket.
Focusing back on Rocket 4, one of the major new components has to do with its engine. Earlier this year we got a sneak peek when the company released a short video of the engine firing. Now we know much more about its unique capabilities and design. Specifically, the Rocket 4 first stage is powered by two turbopump-fed LOX engines, each with an expected maximum sea level liftoff thrust of 40,000 lbf. The engine features a regeneratively-cooled combustion chamber operating at over 1,000 psia chamber pressure which is fed by a turbopump. Each engine can gimbal to provide vehicle steering and control. Actuation of the Thrust Vector Control actuators is “fueldraulic”, powered by high-pressure fuel tapped off from the main fuel circuit. Fueldraulic actuation simplifies the vehicle as it does not require an external high-pressure or high-voltage source for actuation systems that require significant power. The pyrophoric ignition of the engine is ground-based, eliminating another plumbing system from the vehicle and further reducing cost, weight, and complexity. Astra is developing and qualifying an upgraded derivative of a previously qualified engine for this application.
Structure & More
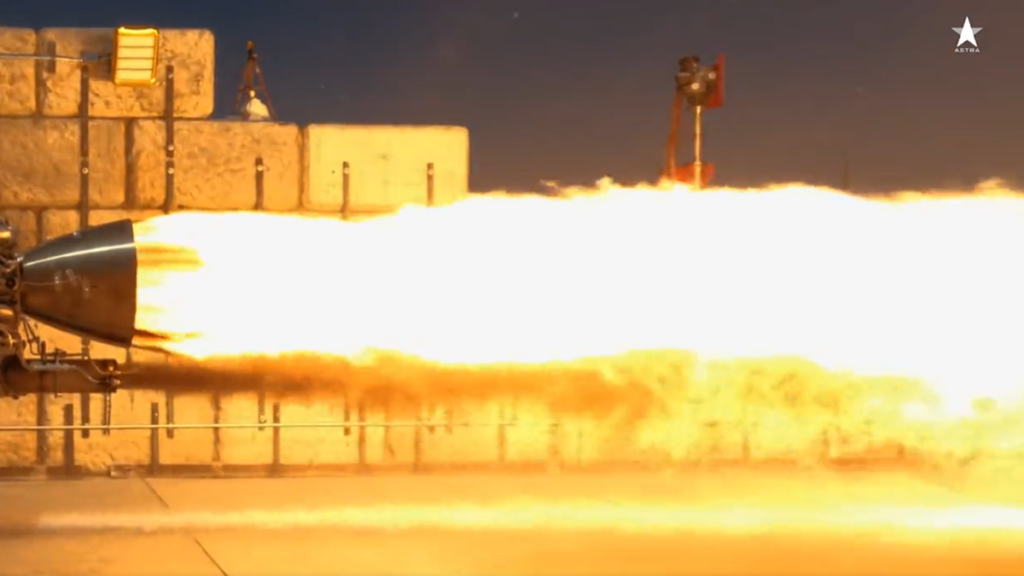
Now that we know more about Rocket 4 and its new first-stage engine, we can take a closer look at its improved structure, upper-stage engines, and Astra’s Launch System 2.0. The upper stage engine is a turbopump-fed engine with a vacuum thrust of approximately 6,500 lbf. This engine is a high-performance LOX engine that propels the upper stage and payload into orbit. It can be restarted prior to payload deployment to enable upper-stage circularization and after payload deployment to lower the upper stage’s orbit. The engine, which is being qualified for Astra’s use, is a derivative of an existing qualified engine.
While not much has changed regarding upper-stage propulsion, a lot has when looking at the structure. The structure of Rocket 4 is built entirely from metal, with design choices optimized to produce rockets efficiently at scale. Astra is trying to focus on simple and proven manufacturing techniques that result in lightweight structures throughout the vehicle: e.g. skin-and-stringers instead of milled isogrid and sheet metal in place of costly additive manufacturing. Throughout the vehicle, the company has incorporated mass-saving features such as common dome tank designs and submersed helium tanks. The first stage consists of two cylindrical tanks, enlarged relative to the Rocket 3 series, but using the same proven design and fabrication approach. The LOX and fuel tank are an aluminum common dome tank set, designed and qualified in-house. The longitudinal seams are friction stir welded and the circumferential seams are TIG welded. The domes are now formed directly from thin sheets of aluminum, and the cylinders are rolled sheets. Helium COPVs are submerged in the fuel tank for packaging efficiency. The tank includes slosh baffles and anti-vortex devices. The upper stage is now essentially a shorter version of the first stage, utilizing the same welding techniques on a similar architecture, though a number of elements are further weight optimized given the increased weight sensitivity of the stage. Like the first stage, it is a common dome assembly with Helium COPVs submerged in the fuel tank.
As for performance, Rocket 4 is designed for a nominal payload capacity of approximately 500 kilograms to a circular 500 km altitude Sun-synchronous orbit (SSO). Astra intends to initially operate the vehicle with de-rated engines in order to reduce initial system performance risks and schedule risks. This leads to an introductory payload capacity in 2024 of approximately 350 kilograms to a circular 500 km altitude Sun-synchronous orbit. As they gain data from ground testing and their early flights, they expect to reduce the engine de-rating which will increase the payload capacity of their launch vehicle.
One of the final important changes has to do with the launch process. Astra points out that its goal with Launch System 1 was to achieve orbital capability as quickly as possible and demonstrate that they could mass-produce rockets. However, following the flight anomaly on their last launch, they listened to their customers, their team, and their stockholders and made the decision to accelerate the introduction of a higher performance rocket and add additional testing that they believe will increase the reliability of future launches. Astra believes Launch System 2 will provide Astra’s customers the launch services they need, whether that be constellation deployment, constellation management, or responsive missions. Dedicated small launches give satellite operators the ability to deploy their spacecraft directly to their operational orbits and allow them to start providing services and adding value sooner.
Astra makes it clear that Launch System 2 is more than just upgraded hardware – it represents a cultural shift from their primary focus on schedule to a focus on reliability. This launch system is the result of a significant change in how Astra designs, builds, qualifies, and operates its launch system. While Launch System 1 began its initial development with just a handful of people in a garage six years ago, Launch System 2 is being designed by teams of world-class engineers in a 225,000 sq. ft. manufacturing and testing facility. They are a completely different company than when they designed Launch System 1 and that shows in the level of investment they’re making into the reliability of this system. The entire system has been scrutinized, and re-engineered where necessary, to support their plans to reliably and repeatably deliver its customers’ payloads to orbit. This shift encompasses every stage of the development process, with multiple teams in the organization focused primarily on reliability, quality, and system safety. Astra is confident they are better-resourced across the board than they were during the development of Launch System 1, including the creation of a new System Verification and Assurance team, quality control lab, and failure analysis lab with state-of-the-art testing capabilities.
Conclusion
Astra Space needs to make some big changes in order to be successful within the industry. This being said, between Rocket 4 and Launch System 2.0, the company is trying to create something special and is changing quite a bit. We will have to wait and see how it progresses and the impact it has on the space industry.