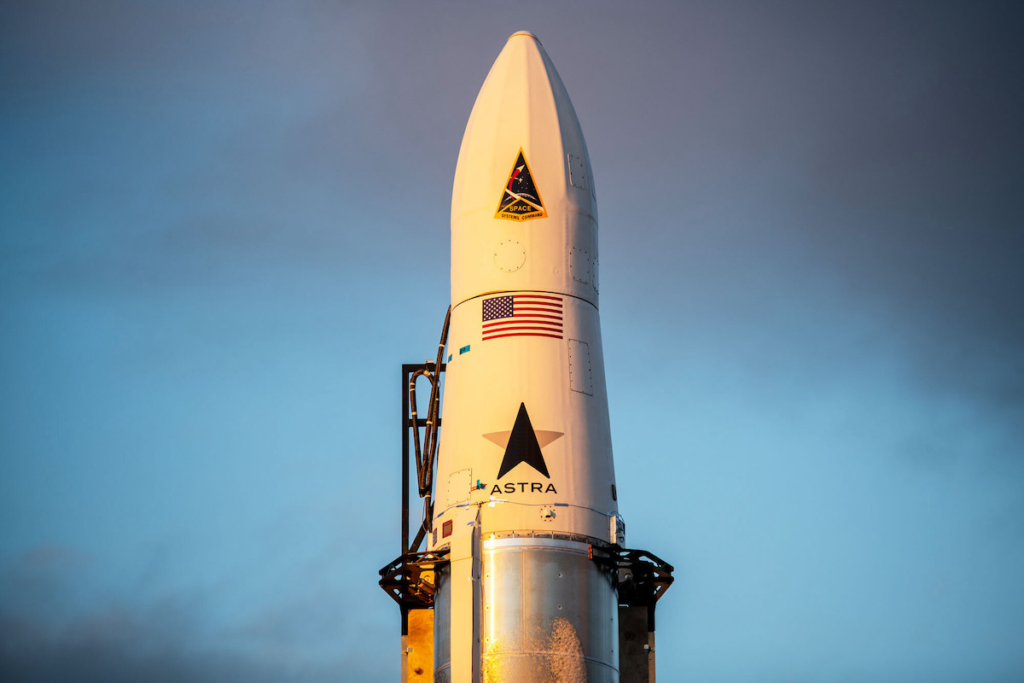
Exactly What Went Wrong On Astra’s Most Recent Launch
The TROPICS-1 mission launched on June 12, 2022, on Astra’s Rocket 3.3, serial number LV0010. The rocket completed a nominal first stage flight, stage separation, and upper stage ignition. Shortly after the ignition of the upper stage engine, the upper stage’s fuel consumption rate increased and remained higher than normal for the remainder of the flight. Soon after we learned that the rocket had failed to reach orbit which led to the cancellation of the Rocket 3 line entirely.
Since this launch Astra, NASA, and the FAA have been working to figure out exactly what went wrong. Just a few days ago however the company finally released a full investigation report and the reason for the failed mission. It turns out a burn through in the upper stage engine caused thrust issues and eventually the payload falling back into Earth’s atmosphere.
The findings of this mission are very important as the company is currently in the process of creating Rocket 4, which utilizes a lot of technology and techniques from the previous rocket line. Here I will go more in-depth into exactly what went wrong on the last flight, Astra’s plan with this new information, its impact on Rocket 4, and more.
Engine Problem
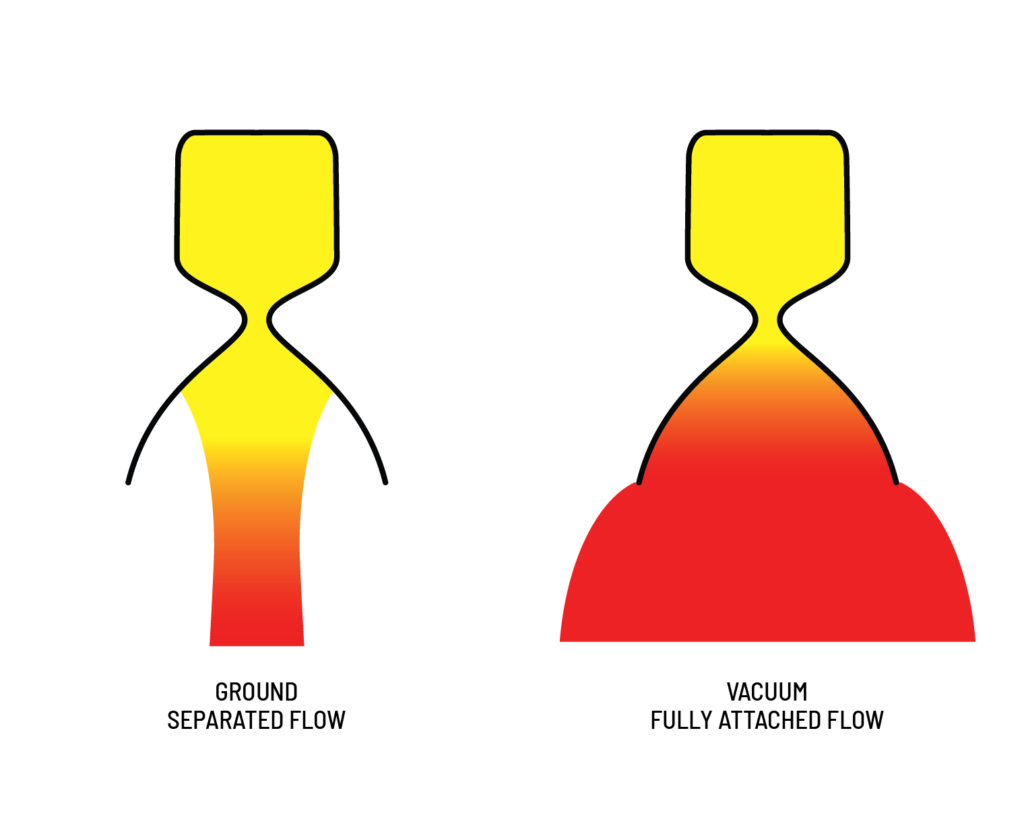
Days ago on the first Astra CEO Chris Kemp tweeted saying, “After working for more than six months to identify the cause of the upper stage mishap on the TROPICS-1 flight, Astra has received the formal closure letter from the @FAANews. Thank you @FAANews + @NASA for your continued partnership.” In terms of what they found, about 250 seconds after upper stage ignition, the stage exhausted its fuel supply with approximately 20% of the liquid oxygen still remaining onboard. As a result, the upper stage was only able to obtain about 80% of the required orbital velocity. The stage was unable to deliver its payloads to orbit, and subsequently re-entered the atmosphere, ending the mission.
Their analysis showed that the inconsistent fuel consumption during the upper stage flight was due to a combustion chamber wall burn-through that occurred 18 seconds into upper stage flight. Flight data showed that the burn-through was precipitated by a substantial blockage of the fuel injector. The mechanics of combustion and regenerative cooling are complex and this failure did not have an immediately apparent root cause, so extensive testing and analysis was required to recreate the failure mode and to understand both how the injector blockage was created and how it led to a burn-through.
When the fuel injector is partially blocked, the rate of fuel passing through the cooling channels decreases. This reduces the amount of heat the fuel can absorb and makes the combustion chamber wall hotter. If the wall gets hot enough, the temperature of the wall can exceed the local boiling point of the fuel, causing some of the fuel to boil along the wall inside the channels. Sometimes this condition can “self-heal”, because a small amount of boiling can actually enhance the cooling ability of the fuel, bringing the wall temperature back down. However, if too much of the fuel boils, its cooling capability is significantly and adversely impacted, and the wall temperature can go up and up until the wall fails and “burns through,” dumping a portion of the fuel flow directly into the combustion chamber – essentially wasting it. This is what they determined had occurred during the TROPICS-1 launch.
They point out that most liquid rocket engines require cooling to prevent the very hot combustion gases from melting the chamber wall and causing the engine to fail. Rocket 3.3’s upper stage engine used regenerative cooling to accomplish this. In a regeneratively-cooled rocket engine, cooling is achieved by routing the fuel through many cooling channels embedded within the combustion chamber wall. This allows heat from the wall to be absorbed into the flowing fuel, keeping the wall at a low enough temperature to prevent failure.
In addition to the partial blockage of the injector, Astra determined that a secondary factor for the burn-through was thermal barrier coating erosion. Portions of the upper stage engine’s combustion chamber have a thermal barrier coating on the inside to insulate the chamber wall and reduce the heat that the fuel is required to absorb as a coolant. If some thermal barrier coating is missing, even a very small amount, that portion of the wall can get much hotter and increase the likelihood of a local burn-through. During the investigation, Astra found that there was a small amount of missing thermal barrier coating on the LV0010 upper stage engine. This missing coating was in a location that was considered acceptable by engineers at the time, but further analysis showed that they had underestimated the need for coating in this region under flight conditions.
Testing & Astra’s Future
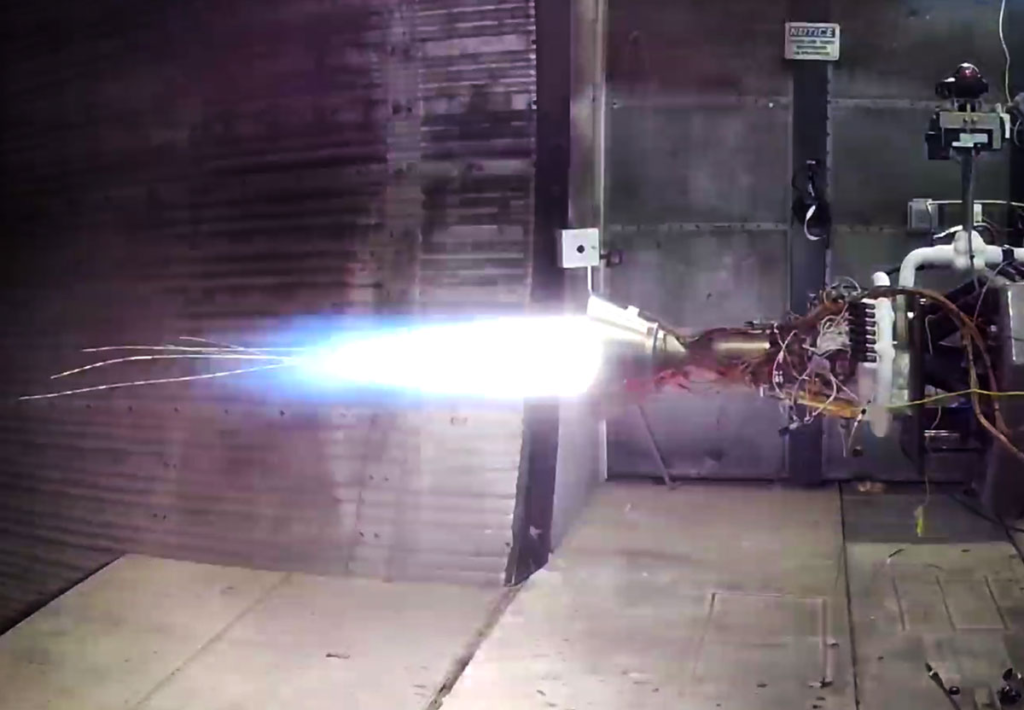
Astra highlights that while it was relatively straightforward to determine that a blockage of the injector had occurred during upper stage flight, it took much longer to conclusively determine what had caused the blockage. They used a combination of analysis and testing to systematically investigate each potential blockage source. Three credible sources for the blockage were the focus of this investigation including foreign object debris (“FOD”), such as particles of metal, gaseous helium, and gaseous fuel. After a lot of testing, they were able to come to the conclusion mentioned prior.
As far as what this means going forward, the company points out that almost immediately following the TROPICS-1 mishap, they made the decision to focus the majority of Astra’s resources on developing Astra’s next-generation launch vehicle: Rocket 4. They focused the TROPICS-1 investigation on learning all that they could to inform the design and operation of this new, larger, and more reliable rocket. To that end, Rocket 4 incorporates key architectural choices (most notably, a different upper stage engine design and a different fuel) that completely eliminate the causes of this mishap. They have also introduced controls designed to eliminate a number of other potential failure modes (like FOD and helium ingestion) that the investigation concluded did not occur on the TROPICS-1 flight, but that Rocket 3.3 could have been susceptible to. For example, they are upgrading their helium diffuser design to prevent frothing in the propellant tanks and ingestion of helium into the engine.
In parallel with the technical cause investigation, Astra also conducted an internal investigation related to improving their processes, systems, and culture to increase the reliability of their fourth generation rocket. They are quoted saying, “Astra has come a long way from the company that we were when we designed Rocket 3 back in 2018 and 2019; our team is now larger and more experienced, we have made significant investments in quality control and failure analysis, and we have learned vital lessons from both launch successes and failures. Still, we know that we have room to improve further, so we are implementing dozens of company-wide initiatives designed to ensure the reliability of Rocket 4.” These improvements include an overhauled design review process, a more robust test-like-you-fly qualification process, and a refreshed set of Astra core values. They are confident they now have the right team and systems in place to make Rocket 4 a success.
In terms of the research related to the TROPICS failure, they believe it was easily the most complex investigation that Astra has ever conducted. In another quote from the report, they said, “We were committed to rigorously and thoroughly investigating the cause of this mishap, and produced an incredible amount of analysis and test results to understand the failure and support our conclusions. Although we came to the preliminary conclusion of an injector blockage and a chamber burn-through quite quickly, we spent several additional months to ensure that we learned everything we could from this launch failure and left no stone unturned. I am thankful for the team’s hard work and we are grateful for the support and partnership of NASA and the FAA throughout this process. We are putting these lessons into action as we prepare for the first launch of Rocket 4.” Currently, the company is still targeting later this year for the first test flight of Rocket 4. With a lot of new hardware and knowledge from previous attempts, Astra has a unique opportunity going forward if successful early on.
Rocket 4 is an expendable, vertically-launched two stage LOX/kerosene rocket, optimized for reliability and manufacturability, and built to significantly reduce the cost of dedicated orbital launches. Rocket 4 is the product of extensive learning that took place during the design, manufacturing, and launch of the prior Rocket 3 series. With much of its architectural heritage coming from the Rocket 3 series, Rocket 4 capitalizes on Astra’s existing flight heritage, while attempting to fine-tune the rocket for improved reliability and manufacturability. Astra has focused on building its rockets using proven and cost-efficient metallic structures, leveraging multidisciplinary production techniques, and eschewing labor-intensive processes such as carbon composite layups. These techniques allow for rapid manufacturing and reduced production costs, which are realized in lower launch costs to customers. Astra plans to ramp Rocket 4 production in 2024, with the goal of creating increased launch availability by achieving an average weekly launch cadence over the course of the product lifecycle.
Conclusion
Astra Space has finally concluded its most recent launch investigation and found out exactly what went wrong on the TROPICS mission. Even though a lot of the information cant be applied to the new Rocket 4 line, some of it can, and it’s very important Astra applies everything learned going forward if they want to avoid similar mistakes. We will have to wait and see how it progresses and the impact it has on the space industry.