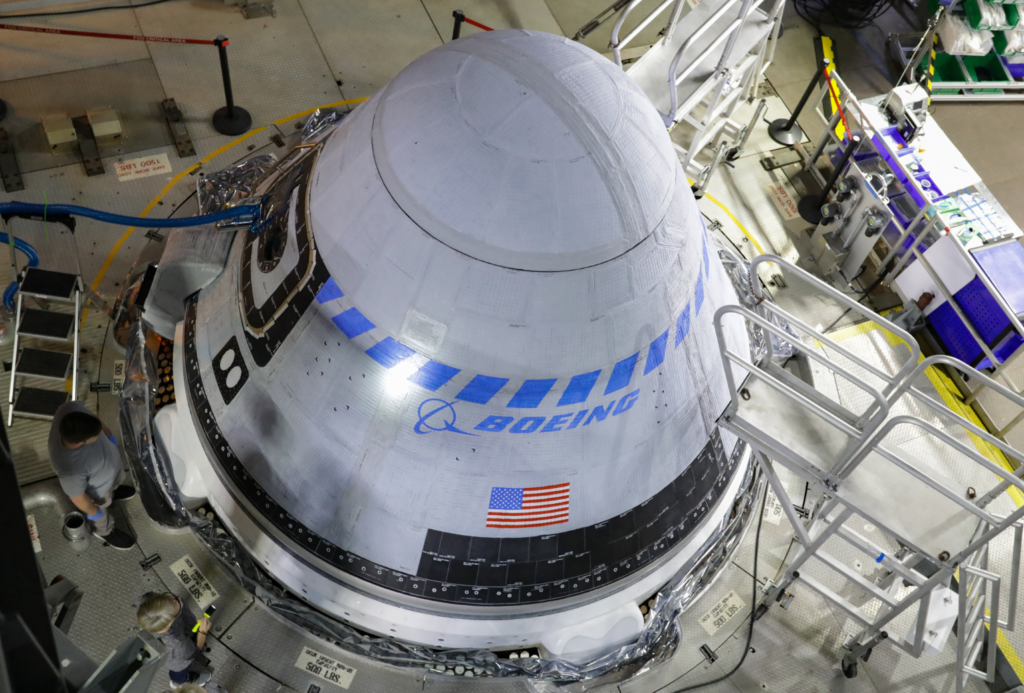
Boeing’s Starliner Is About To Launch For The Second Time
All throughout the space industry, a long list of companies are hard at work on different projects. Boeing is no exception with the work towards Starliner’s second orbital test flight. While the first test flight did not go according to plan, Boeing is confident this time around and have made changes accordingly. All of which need to work perfectly in order for the mission to be a success.
Over the past few days, Starliner has been getting prepared for the orbital test flight expected to launch in only a few days. Just yesterday the flight readiness review was completed along with checks of many of the major systems on both the spacecraft and rocket. In addition, United Launch Alliance’s Atlas V is preparing for the mission.
It has been a few years since the first orbital test flight in late 2019. During this test, just over half an hour into the launch, an issue with the Mission Elapsed Time clock occurred. This error caused the spacecraft to burn into an incorrect orbit, preventing a rendezvous with the International Space Station. Here I will go more in-depth into the upcoming launch and recent updates regarding the mission.
Orbital Flight Test 2
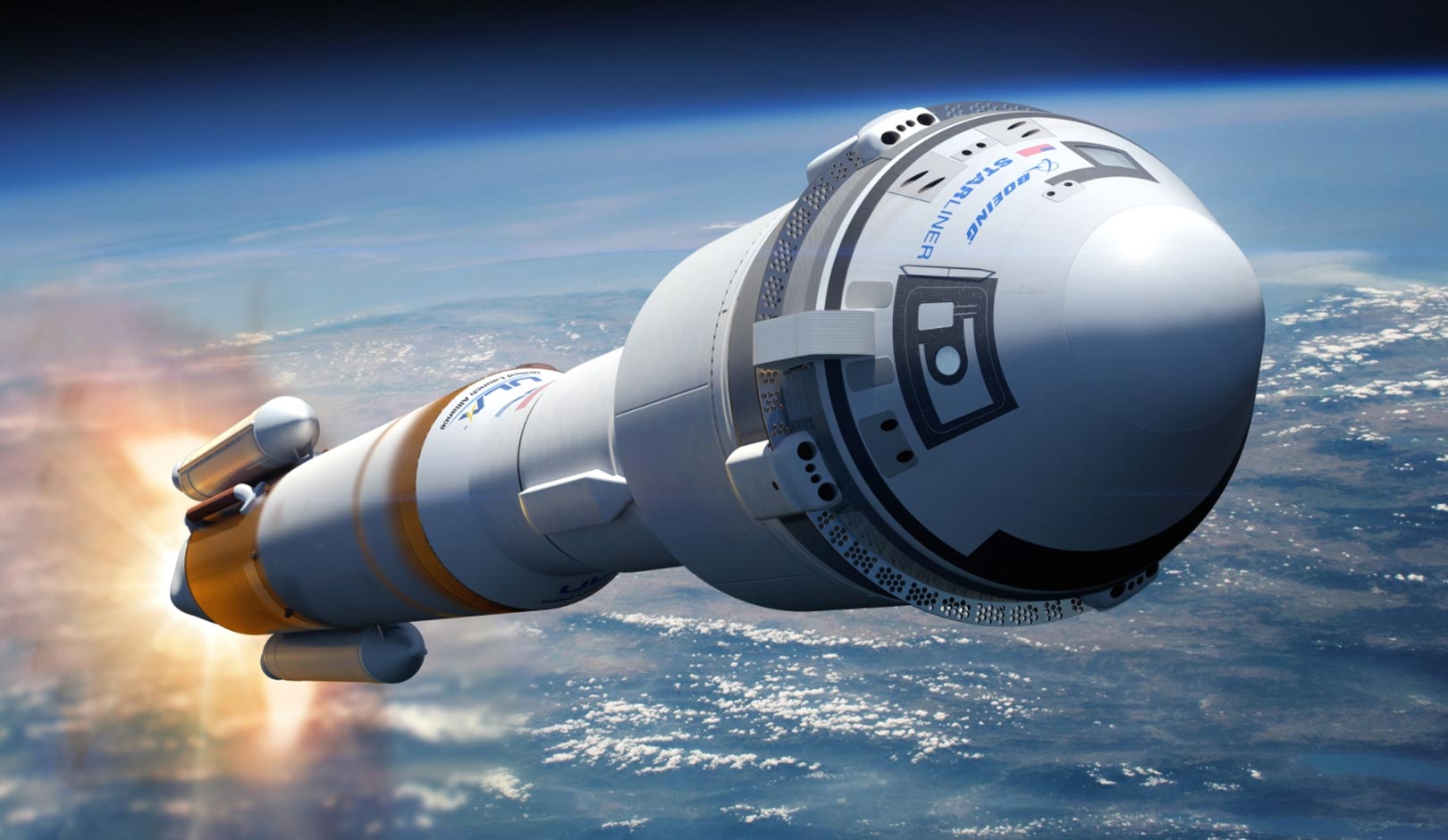
Reaching orbit is quite the feat no matter the size of the company or even agency. Boeing understands this and is working hard to make this second upcoming mission a success for Starliner. Over the past few days, the company along with ULA have provided updates on the mission expected to happen in only a few days. It began yesterday when Boeing tweeted saying, “The Launch Readiness Review for #Starliner’s #OFT2 is complete. Teams have been working to ensure all systems between the rocket and spacecraft are communicating and functioning properly before roll to the pad set for tomorrow, May 18th.” Next, only hours ago, they highlighted the rollout process. Specifically, they tweeted mentioning, “Our team along with @ulalaunch teammates have started rolling #Starliner out of the Vertical Integration Facility and across Space Launch Complex-41 to the Crew Access Tower. Roll to pad is one of the last major milestones before #OFT2 launch.” Finally, the rocket and spacecraft finished the rollout only hours ago. Boeing then highlighted, “The Crew Access Arm has been extended to the #Starliner and #AtlasV stack at Space Launch Complex-41. Pad and operations teams will conduct final checks before tomorrow’s 6:54 p.m. ET launch.” Finally, United Launch Alliance also provided updates and only hours ago pointed out that. “The 48-foot-long swing arm has extended into position, bridging the Space Launch Complex-41 Crew Access Tower to the #Starliner spacecraft.” Its clear from all these updates that everyone involved is very busy as they work towards a launch tomorrow.
Prior to rollout, Boeing’s CST-100 Starliner was integrated on top of United Launch Alliance’s Atlas V rocket at Cape Canaveral Space Force Station. Various tests were then completed to ensure all systems between the rocket and spacecraft were communicating and functioning properly before rolling to the pad. Teams then conducted numerous checks, including a power up of the spacecraft’s avionics system, health checks of the batteries, propulsion system, ordinance system, and data flight instrumentation. Teams also performed interior/exterior inspections, and side hatch leak testing. To date, frequent cycling of the oxidizer isolation valves has been successful in showing repeated valve performance. Tracking and Data Relay Satellite (TDRS) testing also took place to confirm telemetry and command capability between the launch vehicle and spacecraft and Starliner Mission Control in Houston. Final standard prelaunch preparations include loading “late stow” cargo at the launch pad, a final software Mission Data Load with standard prelaunch updates for relative navigation, space weather, inertial navigation, and propellant quantities.
Boeing Starliner
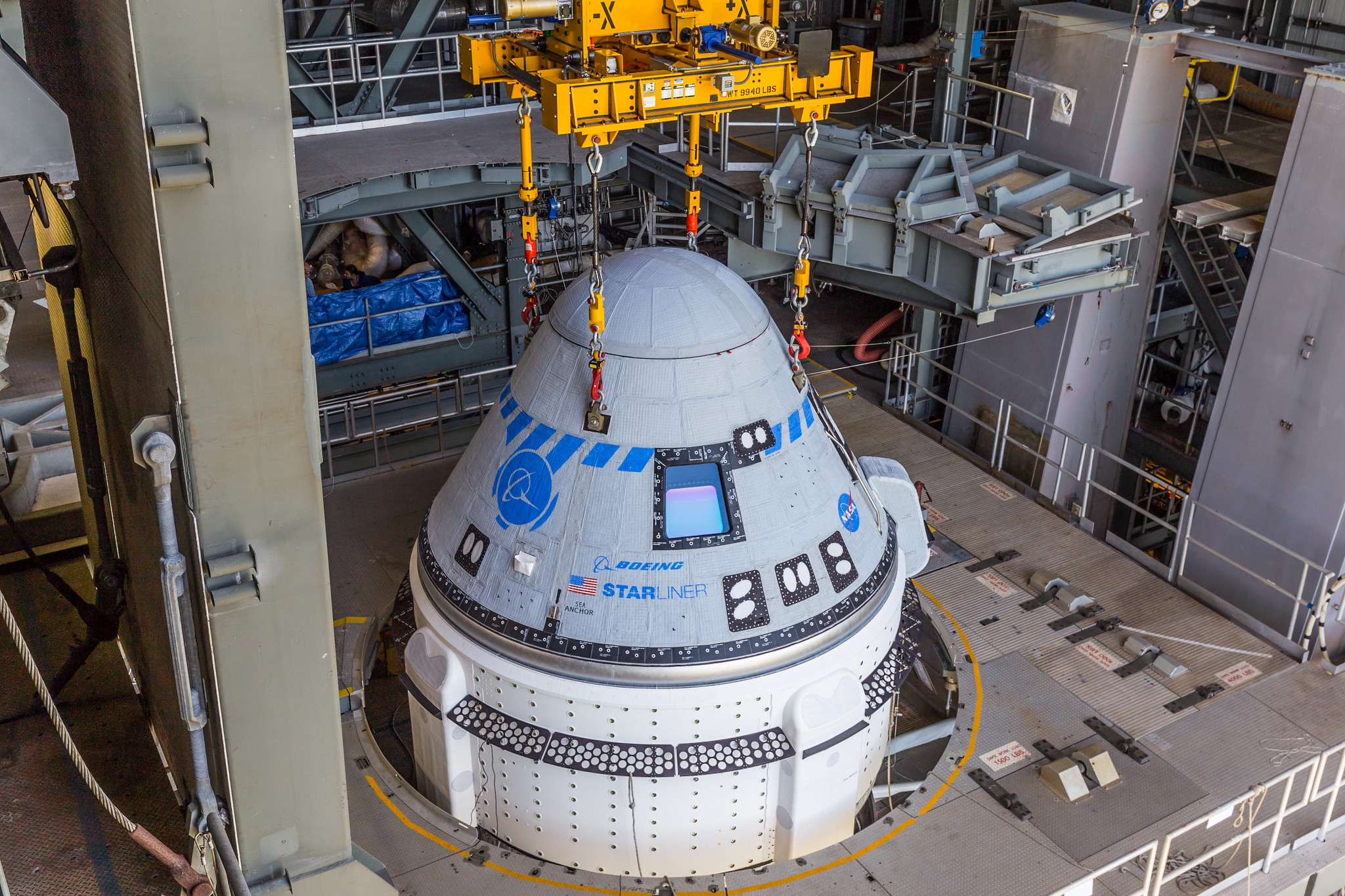
Now that we are up to speed on the mission and all the work currently going on, we can take a closer look at the mission itself and the significance of it. The mission consists of United Launch Alliance’s Atlas V rocket attempting to deliver Boeing’s CST-100 Starliner spacecraft to a 98-nautical mile sub-orbital trajectory on its second Orbital Flight Test. Following separation from Atlas V, Starliner engines will burn taking it the rest of the way to orbit and onto the International Space Station. Liftoff will occur from Space Launch Complex-41 at Cape Canaveral Space Force Station, Florida. Part of NASA’s Commercial Crew Program, the uncrewed OFT is the second launch of the CST-100 Starliner. The second uncrewed test flight will demonstrate end-to-end performance of the Atlas V rocket and Starliner spacecraft, including performance of the guidance, navigation and control systems, ground systems and operations teams, as well as on-orbit, docking, re-entry and landing operations. Starliner will land at one of five designated sites in the western United States. All human launch systems, going back to the Mercury Atlas, traditionally conduct uncrewed test flights prior to crewed flights. The uncrewed flight will allow the team to thoroughly evaluate all flight data against pre-flight predictions and make any necessary adjustments prior to flying astronauts.
The first orbital flight test mission was launched on December 20th, 2019, an issue with the spacecraft’s Mission Elapsed Time clock occurred 31 minutes into the flight. This anomaly caused the spacecraft to burn into an incorrect orbit, preventing a rendezvous with the International Space Station. The mission was reduced to just two days, with the spacecraft successfully landing at White Sands Space Harbor on 22 December 2019. This was a big setback for the company and held back a lot of future opportunities within the commercial crew program and more. However, since then Boeing has continued to work on the program and is confident in Starliner’s capabilities this coming launch.
In terms of the spacecraft, the Starliner was designed to accommodate seven passengers, or a mix of crew and cargo, for missions to low-Earth orbit. For NASA service missions to the International Space Station, it will carry up to four NASA-sponsored crew members and time-critical scientific research. The Starliner has an innovative, weldless structure and is reusable up to 10 times with a six-month turnaround time. It also features wireless internet and tablet technology for crew interfaces. On the launch tomorrow, as partially mentioned prior, Starliner will be on top of ULA’s Atlas V rocket. In this case, it has been modified specifically for the Boeing CST-100 Starliner spacecraft. The Atlas V Starliner configuration does not include a payload fairing. Instead, the Starliner’s insulated surfaces take the place of the fairing to protect the uncrewed spacecraft during ascent. The vehicle’s height with the Boeing CST-100 Starliner is approximately 172 ft. The CST-100 Starliner is attached to the Atlas V using a launch vehicle adapter, which also includes an aeroskirt to reduce the aerodynamic loads on the vehicle. The aeroskirt is jettisoned for improved performance following booster stage separation. Below the spacecraft sits the second stage Centaur. The Centaur second stage is 10 ft in diameter and 41.5 ft in length. Its propellant tanks are pressure-stabilized and constructed of corrosion-resistant stainless steel. Centaur is a cryogenic vehicle, fueled with liquid hydrogen and liquid oxygen. The Atlas V configuration for this mission is powered by dual RL10A-4-2 engines, each producing 22,600 lbs of thrust. The cryogenic tanks are insulated with a combination of helium-purged blankets, radiation shields, and spray-on foam insulation. The Centaur forward adapter provides structural mountings for the fault-tolerant avionics system and electrical interfaces with the spacecraft. The Centaur also includes an Emergency Detection System, or EDS, that monitors for critical hazards to detect an imminent or occurring failure. The EDS also provides critical in-flight data which supports jettison of the ascent cover and initiates CST-100 Starliner spacecraft separation.
Finally, you have the booster which is 12.5 ft in diameter and 106.5 ft in length. The booster’s tanks are structurally rigid and constructed of isogrid aluminum barrels, spun-formed aluminum domes and intertank skirts. Booster propulsion is provided by the RD-180 engine system (a single engine with two thrust chambers). The RD-180 burns RP-1 (Rocket Propellant-1 or highly purified kerosene) and liquid oxygen and delivers 860,200 lbs (3.83 mega-Newtons) of thrust at sea level. Two solid rocket boosters (SRBs) generate the additional power required at liftoff, with each SRB providing 348,500 lbs (1.55 mega-Newtons) of thrust. The Centaur avionics system provides guidance, flight control and vehicle sequencing functions during the booster and Centaur phases of flight.
Conclusion
Right now is a very busy time within the space industry. Many different companies and agencies are trying new and ambitious ideas with the goal of increasing access to space. Boeing has been working on Starliner for quite a while now and is confident in the orbital test flight set for tomorrow. We will have to wait and see how it progresses and the impact it has on the space industry.