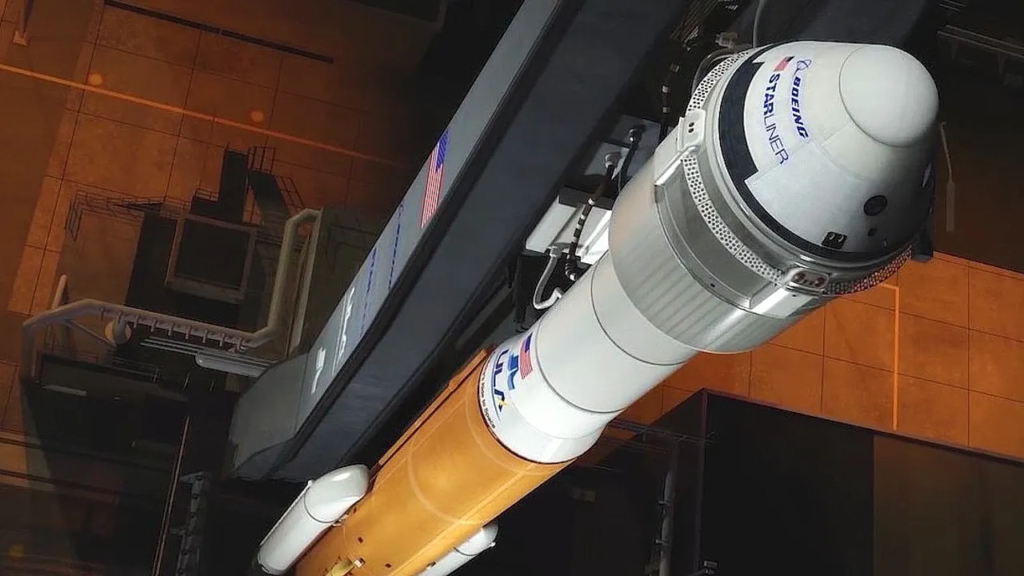
An In-Depth Look At The Design of Boeing’s Starliner Spacecraft
Just over a month from now, Boeing’s Starliner spacecraft is set to attempt its most important mission yet. After two past orbital test flights with varying results, this upcoming mission features the first crew ever to be launched on Starliner. With this big responsibility comes a lot of preparation and work to ensure the mission goes smoothly.
While Starliner has had somewhat of a rocky past, both NASA and Boeing are confident in its design and the changes made after different problems occurred. In reality, the spacecraft offers some unique qualities that differentiate it from other human rated spacecraft within the industry. Not to mention a long history of development and testing starting back in 2010.
However, it brings up the question of how exactly does this spacecraft work and how will it compete with other options such as SpaceX’s Crew Dragon. In the time since the two companies began competing, Boeing has missed out on a lot of launch contracts that SpaceX is securing. Here I will go more in-depth into Starliner’s design, the features in place to keep its crew safe, what to expect in the coming weeks, and more.
Starliner Design
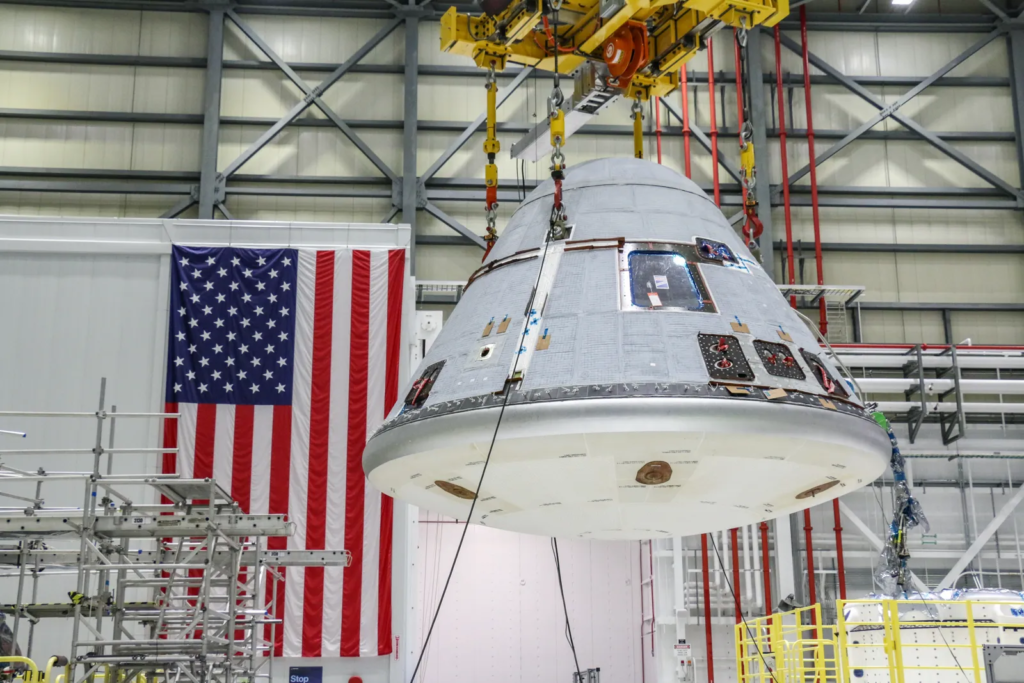
Starliner is a partially reusable spacecraft designed to transport crew to the International Space Station (ISS) and other low-Earth-orbit destinations. It was designed to accommodate seven passengers, or a mix of crew and cargo, for missions to low-Earth orbit. For NASA service missions to the International Space Station, it will carry up to four NASA-sponsored crew members and time-critical scientific research. The capsule has a diameter of 4.56 m (15.0 ft), which is slightly larger than the Apollo command module and SpaceX Dragon 2, and smaller than the Orion capsule. The Boeing Starliner is designed to be able to remain docked to ISS for up to seven months with reusability of up to ten missions.
In the future, Boeing plans to alternate between two reusable crew modules for all planned Starliner missions. Each flight uses a new service module, which provides propulsion and power-generation capacity for the spacecraft. Starliner uses the NASA Docking System for docking. Boeing modified the design of the Starliner docking system prior to OFT-2, adding a hinged re-entry cover below the expendable nosecone for additional protection during the capsule’s fiery descent through the atmosphere, similar to the one used in the SpaceX Dragon 2 nosecone. This was tested on the OFT-2 mission. Specifically, the capsule uses the Boeing Lightweight Ablator for its heat shield.
Solar cells, provided by Boeing subsidiary Spectrolab, are installed onto the aft face of the spacecraft’s service module, and provide 2.9 kW of electricity. Since Starliner is just a spacecraft, it requires a dedicated launch vehicle to get into LEO. The spacecraft is designed to be compatible with multiple launch vehicles, including the Atlas V, Delta IV, and Falcon 9, as well as the in-development Vulcan Centaur which is about to launch. In addition to the capsule and service module, a 1.78 m-long (5 ft 10 in) structure is integrated into the launch vehicle adapter of Atlas V, called aeroskirt, to provide aerodynamic stability and dampen the shock waves that come from the front of the rocket.
In the time since it was unveiled, there has been quite a bit of funding for this project. Boeing funded the development of Starliner in 2010 only after both commercial space station opportunities and NASA commercial crew contracts on offer allowed the business case to close. While the company had received $18 million under the NASA Commercial Crew Development (CCDev) contract by 2010 for early design work, substantial Boeing private funds would be required to complete development, even with Boeing competing for additional NASA contracts. This exposed Boeing to ordinary business financial risk that had not been a large part of traditional cost-plus contracting that Boeing had previously done for work on space capsules.
Boeing was awarded a US$92.3 million contract by NASA in April 2011 to continue to develop the CST-100 under CCDev phase 2. On August 3, 2012, NASA announced the award of US$460 million to Boeing to continue work on the CST-100 under the Commercial Crew Integrated Capability (CCiCap) program. However, due to delays and technical problems, Boeing has taken a number of charges against earnings for the Starliner program by 2022. This includes $410 million in 2020, $185 million in October 2021, and $288 million through the third quarter of 2022.
Abort Capabilities
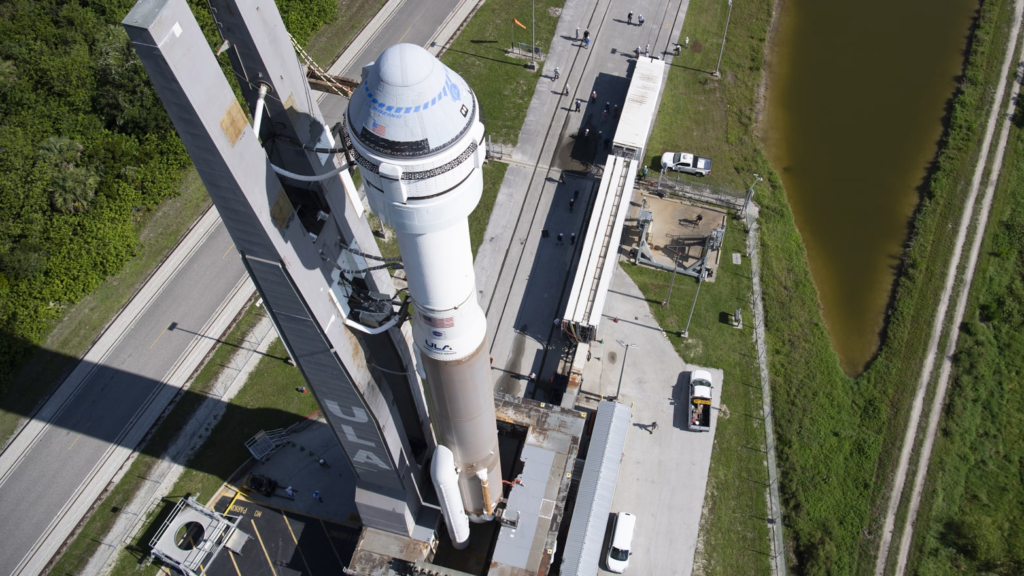
With the first human mission just months away, abort capabilities become extremely important. In the past, after several rounds of competitive development contracts within the Commercial Crew Program starting in 2010, NASA selected the Boeing Starliner, along with SpaceX Crew Dragon, for the Commercial Crew Transportation Capability (CCtCap) contract round. The first of these crewed test flight tests were initially planned to occur in 2017. In late 2019, the uncrewed Boeing Starliner Orbital Flight Test (Boe-OFT) launched on an Atlas V N22 and reached orbit, but the flight was not successful, failing to meet test objectives and returning to earth early. NASA allowed Boeing a repeat test flight, Boe-OFT 2, which was to launch in August 2021, but was scrubbed before launch due to inoperable valves in the propulsion system. After replacing the spacecraft’s service module, Boeing targeted OFT-2 to occur in May 2022 at the earliest. OFT-2 ended up launching on May 19, 2022. The craft suffered several anomalies during its flight but controllers were able to work around them and Boeing and NASA expressed confidence in the spacecraft.
These various issues lead us to some of the tests and options Starliner has to offer. On the service module are four Rocketdyne RS-88 engines burning hypergolic propellants, which will be used for launch escape capability in the event of an abort. In July 2018, a test anomaly was reported in which there was a hypergolic propellant leak due to several faulty abort-system valves. Consequently, the first unpiloted orbital mission was delayed to April 2019, and the first crew launch rescheduled to August 2019. In March 2019, it was reported that these test flights had been delayed by at least three months, and in April 2019 Boeing announced that the unpiloted orbital mission was scheduled for August 2019.
In May 2019, all major hot-fire testing, including simulations of low-altitude abort-thruster testing, was completed using a full up to service module test article that was “flight-like”, meaning that the service module test rig used in the hot-fire testing included fuel and helium tanks, reaction control system, orbital maneuvering, and attitude-control thrusters, launch abort engines and all necessary fuel lines and avionics that will be used for crewed missions. This cleared the way for the pad abort test and the subsequent uncrewed and crewed flights. Finally, a pad abort test took place on November 4, 2019. The capsule accelerated away from its pad, but then one of the three parachutes failed to deploy, and the capsule landed with only two parachutes. The landing was, however, deemed safe, and the test a success. Boeing did not expect the malfunction of one parachute to affect the Starliner development schedule.
Taking a closer look at a launch profile with an Atlas V can also help put this process into perspective. After passing through the stages of max q, SRB jettison, booster separation, Centaur ignition, nosecone and aeroskirt jettison, it finally releases the Starliner spacecraft at stage separation, nearly 15 minutes after lift-off on a 181 km-high (112 mi) suborbital trajectory, just below the orbital velocity needed to enter a stable orbit around Earth. After separating from the Dual Engine Centaur, the Starliner’s own thrusters, mounted on its service module, boost the spacecraft into orbit to begin its journey to the International Space Station.
The suborbital trajectory is unusual for a satellite launch, but it is similar to the technique used by the Space Shuttle and Space Launch System. It makes sure the upper stage of the rocket re-enters the atmosphere in a controlled way. The Starliner’s orbit insertion burn begins about 31 minutes into the mission and lasts 45 seconds. The N22 configuration is specific to Starliner. All other Atlas V payloads require fairings, but Starliner cannot use a fairing because it must be able to perform a “launch abort”. In addition, all other Atlas V payloads use the single-engine version of the Centaur upper stage, but Starliner uses the two-engine version to provide more flexible abort options in the case of failures in the later phases of the launch. These changes increase crew safety.
Boeing Crew Flight Test (Boe CFT) will be the first crewed mission of the Boeing Starliner and the third orbital flight test of the Starliner overall after the two uncrewed flight tests, OFT-1 and OFT-2. Though the launch date for the mission was scheduled for late 2021, various delays have pushed the launch of the CFT mission to no earlier than April 2023. It will fly with a crew of two NASA astronauts to the International Space Station for a one-week test flight. Something we can expect to see soon and hopefully with no errors.
Conclusion
Boeing has been working on the Starliner spacecraft for over a decade now. In that time there have been a host of different tests, two orbital test flights, and more. These tests have often revealed different problems that Boeing and NASA have fixed and now are confident enough for a crewed mission. We will have to wait and see how it progresses and the impact it has on the space industry.