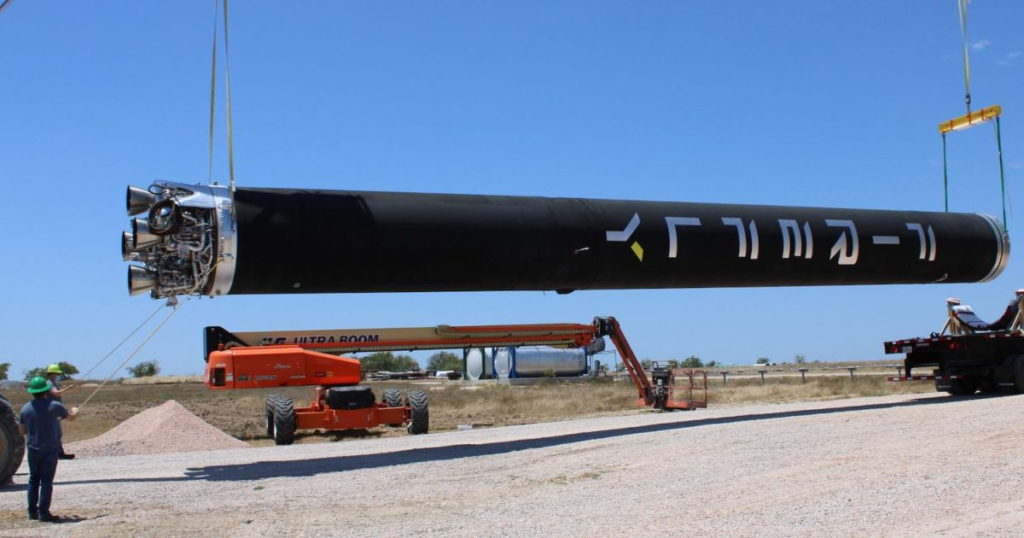
A Closer Look At Firefly Aerospace’s Alpha Launch Vehicle
Right now a lot is going on throughout the entire space industry. With the recent release of Webb’s first images, SpaceX’s continued work towards Starship’s first orbital test flight, SLS, and much more, it seems like everyone is very busy. Firefly Aerospace is no exception with the work towards its second orbit test flight with Alpha.
Alpha is attempting to offer the highest payload capacity for the lowest cost per kilogram in its vehicle class. Firefly describes Alpha as the world’s most advanced 1,000 kg small satellite launch vehicle. While its first orbital test flight was not 100% successful, few are, and the company learned a lot of valuable information from the launch.
Now in the summer of 2022, Firefly has tested the next Alpha rocket and is closer than ever to returning to the pad. However, this brings up the question of what makes Alpha different from other rockets within the industry, and what is Firefly hoping to achieve. Here I will go more in-depth into the design of Alpha, the features that make it stand out, and what to expect in the coming months regarding this rocket.
Firefly Alpha Progress
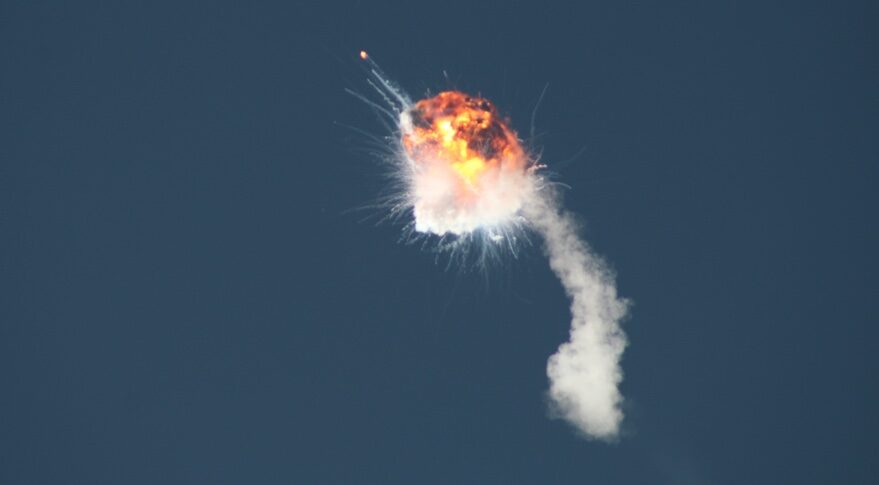
Over the past few months Firefly has been working in overdrive as they prepare for the next launch of Alpha named To The Black. Starting in late May the company tweeted saying, “Goodbye Briggs, TX; hello Vandenberg, CA. Launch preparations for Flight 2 #ToTheBlack have begun with both stages shipped from our test and manufacturing facilities to our launch site.” This tweet included multiple images of the shipping process with both stages. Since this tweet, a few months went by before the company provided another update on Alpha. Earlier this month on July 4th, Firefly tweeted again this time mentioning, “Happy 4th of July! (Pic: Firefly Alpha Flight 2 fully integrated vehicle at Vandenberg Space Force Base).”
All of this comes after Firefly conducted the maiden flight of its Alpha launch vehicle from Vandenberg Space Force Base in California in September of last year. After this first flight Tom Markusic, CEO of Firefly Aerospace said, “Firefly has conducted the first test flight of our Alpha vehicle. The day marked a major advancement for the Firefly team, as we demonstrated that we ‘arrived’ as a company capable of building and launching rockets. Although the vehicle did not reach orbit, we acquired a wealth of flight data that will greatly enhance the likelihood of Alpha achieving orbit during its second flight. In short, we had a very successful first flight.” The test began with a nominal countdown and lift off at 6:59 PM PDT and achieved a successful first stage ignition, liftoff from the pad, and progression to supersonic speed. During the flight, the launch vehicle experienced an anomaly that resulted in a safe termination of flight by the Range using the Flight Termination System (FTS). An initial review of flight data indicated that an electrical issue caused the shutdown of one of the four first stage Reaver engines.
As stated on September 2nd by Space Launch Delta 30 the Alpha rocket was terminated “over the Pacific Ocean at 7:01 p.m. Pacific Time after a successful liftoff at 6:59 p.m. There were no injuries associated with the anomaly.” During the two minutes and twenty-five seconds of flight, Firefly obtained a substantial amount of flight data that will be utilized to improve the design of future Alpha launch vehicles, including the second flight vehicle, which is currently being integrated for flight at their Briggs, Texas manufacturing and test facility.
Markusic also stated, “Firefly has been incredibly fortunate to have partners that share our vision and passion. The most difficult and perilous days of Firefly Aerospace were funded by Noosphere Ventures, founded by Max Polyakov. Early on, Max and I created the technological and business development roadmap – the first launch of Alpha being a hard-fought landmark achievement for the entire team.” He continued, “The Alpha launch vehicle was developed by a world-class group of talented and dedicated technical directors. Firefly’s Flight and Test Operations Department, led by Anne Chinnery, Brad Obrocto, and Sean Reilly, built Firefly’s launch facility and successfully conducted the first launch.” Dr. Max Polyakov, Firefly’s Co-Founder said, “Alpha’s first launch was a historic day for Firefly. I salute and thank the team that has worked so hard to make the vision of Firefly a reality. In just four years, Firefly has developed and flown an orbital class launch vehicle and is building our Blue Ghost lunar lander to go to the Moon in 2023 — incredible accomplishments for such a short time!” It has been close to a year since the first test flight. This being said, we should expect to see Alpha lift off once again in only a few months as Firefly continues to show promising results.
Launch Vehicle Design
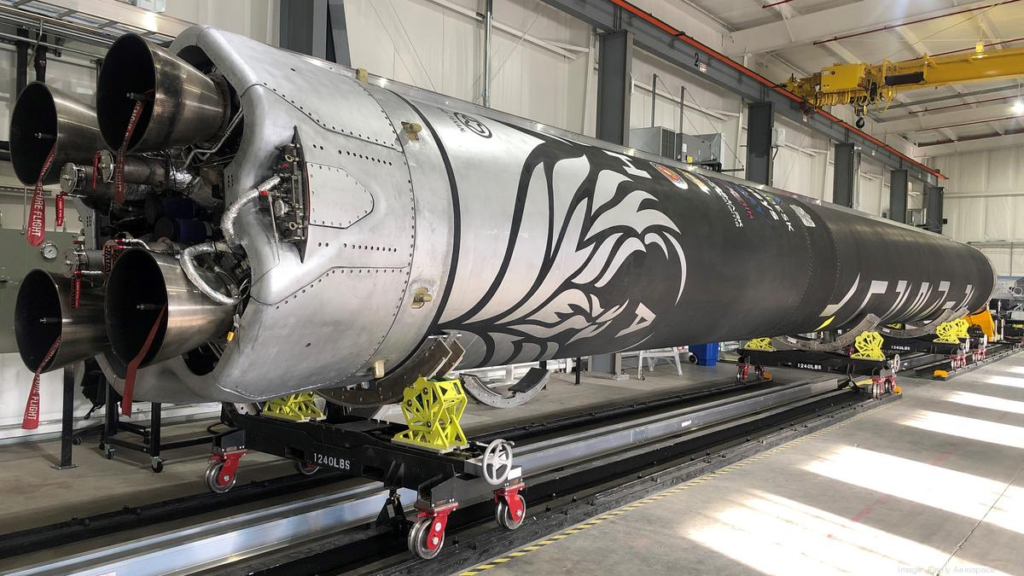
Now that we know more about Firefly’s journey and what the company has been working on, we can take a closer look at the launch vehicle itself. Using tried and true, flight-proven rocket technologies, Alpha is 100% manufactured in the USA and designed to be one of the most reliable small satellite launchers available. Alpha’s pump-fed, regeneratively-cooled engines use standard LOx/RP, and its avionics systems, such as the flight computer and communication system, employ COTS components with established flight heritage. Modern advances in carbon composite materials are used to create strong, lightweight primary structures such as propellant tanks. Entirely manufactured and launched in the USA, they are able to keep costs to a minimum while achieving unprecedented dependability. In addition, Firefly’s dedicated launch facilities on the west and east coast of the US, at Vandenberg Space Force Base Space Launch Complex 2 and Cape Canaveral Space Force Station Space Launch Complex 20, will enable flights as frequent as once per month by later this year.
As partially mentioned prior, Alpha utilizes well established propulsion technology. Both stages use common designs: copper regen-cooled LOx/RP-1 thrust chambers, a simple tap-off cycle which drives single shaft turbopumps, nozzle-mounted turbine exhaust manifolds, and hydraulic actuators. Innovations in Firefly engines include its simple “Crossfire” injector, tap-off geometry, dual-mounted electrically actuated, trimmable propellant main valves, and ultra-compact horizontal turbopump mounting. The upper stage engine, “Lightning,” includes a turbine-exhaust cooled refractory metal high area ratio nozzle extension. The first stage “Reaver” engines feature simple single axis gimballing. Consistent with the overall Alpha vehicle design, cost and performance are traded and optimized in Lightning and Reaver components to try and provide the best payload performance value. In terms of the structure itself, Firefly utilizes advanced carbon-fiber composites for the entire airframe of Alpha, including the state-of-the-art, linerless, cryogenic propellant tanks. Firefly points out that composite materials are ideally suited to launch vehicle structures due to their high strength, low density and tailorable material properties. This allows Firefly Alpha to lift heavier payloads than a similar metal rocket.
You then have avionics which play a very important role behind the scenes. Firefly Avionics hardware utilizes a combination of custom designed state-of-the-art and Commercial Off the Shelf (COTS) components. Data Acquisition is accomplished using a rugged, modular Data Acquisition Chassis, which provides analog to digital conversion of all sensor data, and further packages the data and transmits to the Flight Computer via an onboard Ethernet network. The Flight Computer incorporates all vehicle telemetry and transmits data along with video to various Earth ground stations along the flight trajectory, for the duration of the flight.
Firefly also put a lot of time into the payload fairing of Alpha. The Alpha payload fairing (PLF) is a carbon composite structure developed, manufactured, and qualified by Firefly. It measures 2.2 m in diameter, and 5 m in height. The fairing separation system employs a debris free, low-shock pneumatic separation system fully tested prior to each flight. The payload fairing remains latched until launch ascent free molecular heating is below a specific threshold. Immediately thereafter, Alpha initiates a low shock separation event to deploy the two fairing halves from the payload attach fitting (PAF) and LV upper stage. The dynamic payload envelope accounts for dynamic movement of the fairing and payload relative to one another, acoustic isolation panels, thermal expansion, and manufacturing tolerances.
Conclusion
Firefly Aerospace has been staying busy over the last few years. Not only are they working to launch Alpha for a second time, but the company has also been focusing on its Blue Ghost Lunar Lander and reaching the Moon. In recent weeks we have been provided updates on Alpha and the upcoming launch. The first was not perfect but Firefly has ambitious goals for the future. We will have to wait and see how it progresses and the impact it has on the space industry.