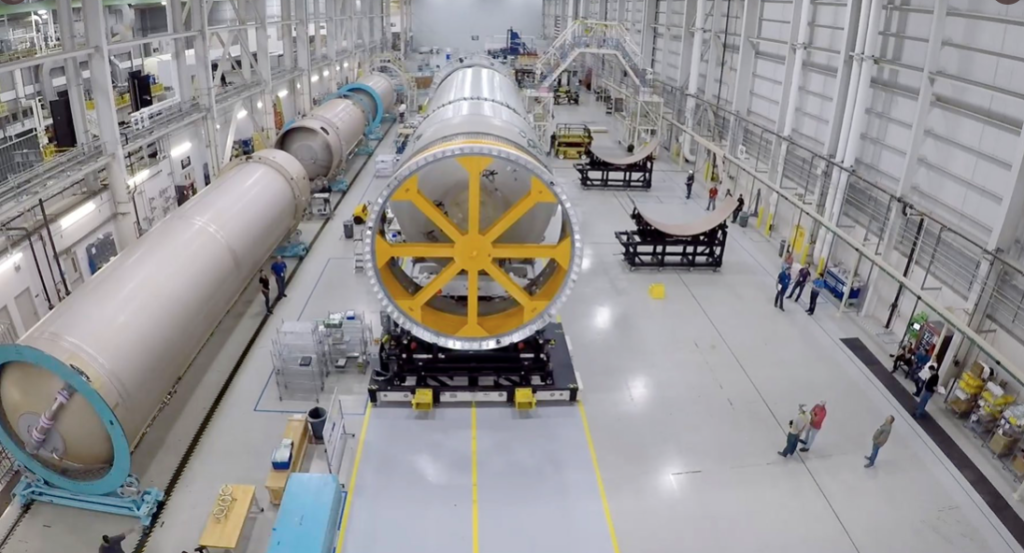
How ULA Is Fixing Vulcan’s Upper-Stage Tank
Vulcan is a next-generation launch system under development by United Launch Alliance that’s been trying to lift off for years now. Unfortunately, different delays related to the first mission’s payload, rocket, and plan have all pushed this date back a few years. Recently we got news that the upper stage was being unstacked and shipped to ULA’s factory for necessary upgrades.
Just days ago Tory Bruno gave more insight into this process and what the repairs will look like and how exactly it affects Vulcan’s schedule. All of this comes after a Vulcan upper stage Centaur test article exploded within the test stand. At first, the thought was that it wouldn’t affect the maiden flight but ULA has since changed its mind.
This comes in addition to the BE-4 flight engine explosion which ULA and Tory are very confident will have little to no impact on Vulcan’s maiden flight. Here I will go more in-depth into the upper stage repairs currently underway, the new launch date for Vulcan, what to expect in the coming months, and more.
Upper Stage Changes
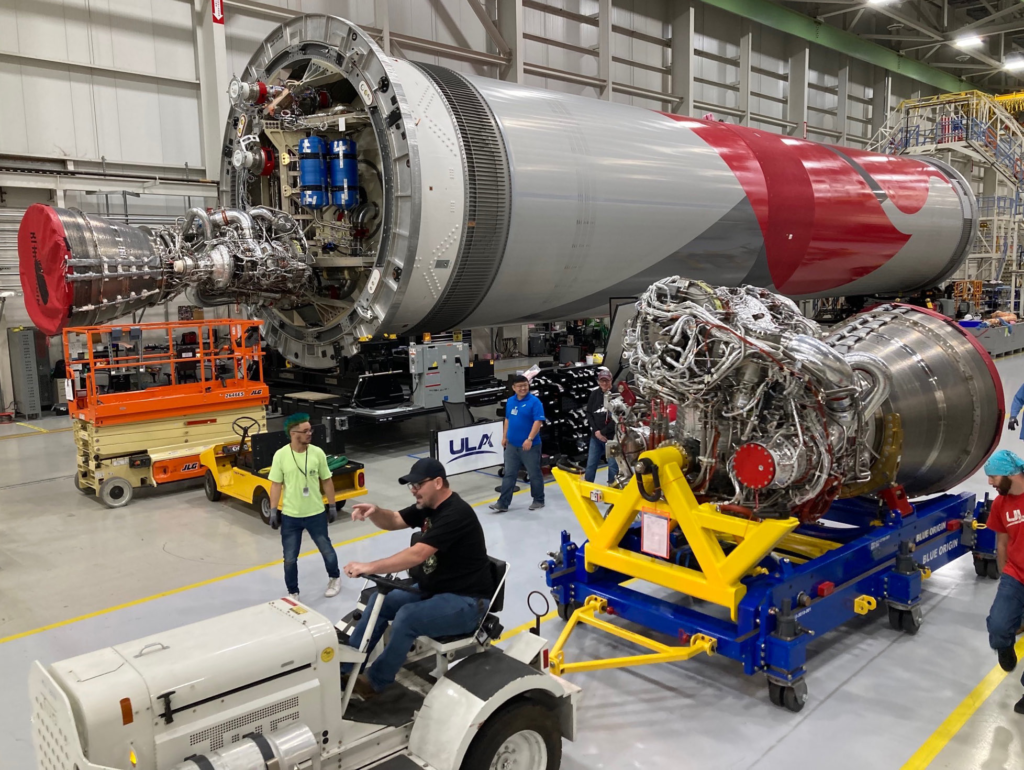
Back on March 29th, we first learned about the incident. At the time ULA CEO Tory Bruno commented that “During Qual testing of Centaur V structural article at MSFC, the hardware experienced an anomaly. This is why we thoroughly & rigorously exercise every possible condition on the ground before flight. Investigation is underway. Vulcan will fly when complete.” When video of the test anomaly came out he provided more context saying, “Outside of the test rig/ stand. Test article is inside (you can’t see it). Hydrogen leak. H2 accumulated inside the rig. Found an ignition source. Burned fast. Over pressure caved in our forward dome and damaged the rig.”
After this initial information was released, we didn’t hear much over the next few months other than updates on the general investigation. This was until very recently when the company made it clear that there was a problem that needed to be addressed and the Cert 1 Centaur upper stage would need to head back to the factory. A few days ago on the 13th, in a call with reporters, Tory Bruno said the changes to the Centaur upper stage stemmed from an investigation into the test mishap.
The investigation found that the leak originated in the forward dome of the tank, which is made of very thin stainless steel, near a door at the top of the structure. A very detailed finite element model of that part of the tank revealed a “stress riser,” or intensification of loads, because of the complicated geometry around that part of the dome. That had been missed in earlier, coarser analysis of the tank. To add on to this, the Centaur 5 uses a new laser welding technology, rather than arcwelding on earlier Centaurs, for seams in the tank dome. The strength of the laser welds is less than what had been expected from earlier tests.
“The two things together — higher loads, somewhat lower strength in the welds — are what caused the crack to begin,” Bruno said. The amount of testing of that specific Centaur may have also contributed to the crack, he added. To correct the problem, ULA will add a layer of stainless steel around the door on the top of the dome and strips along the welds extending about 60 centimeters from it. “It’s not a very sophisticated or high-tech or high-risk action,” he said. “We simply need it to be just a little bit thicker.”
The additional material will add about 135 kilograms of mass to the Centaur initially, but that increase will be cut in half on later ones. That will reduce the payload performance by the same amount, but Bruno said none of the upcoming Vulcan missions would be affected by that change given the requirements of those missions and vehicle margins. With all the future Vulcan rockets needing a few upgrades, it changes how ULA is going to approach the next few launches.
The company is already incorporating those changes in a Centaur that was originally going to be used on the third Vulcan mission. That will instead be used for the inaugural Vulcan launch, Cert-1, while the Centaur that had already been shipped to Cape Canaveral and tested for that launch will be returned to ULA’s Decatur, Alabama, factory for modifications. While not ideal, ULA has found the problem, a relatively easy fix, and is now applying it to each of the Vulcan rockets.
Vulcan’s Schedule
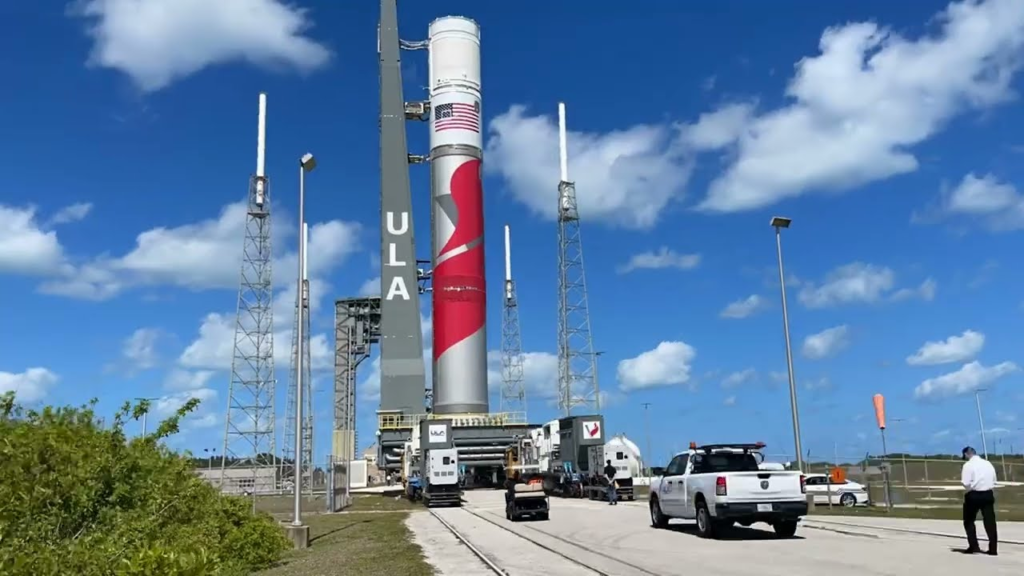
“In terms of schedule, that means that we expect to fly in the fourth quarter of this year,” Bruno said. On this first mission, Vulcan is carrying multiple payloads for a few different customers. For example, ULA is working with the primary customer of Cert-1, Astrobotic, to identify the windows in the fourth quarter that would be available for launching that company’s Peregrine lunar lander. ULA previously said only a few days were available each month for launching Peregrine.
It’s important to point out that these delays will also have an impact on Dream Chaser and the spaceplane’s maiden flight. Earlier this year Sierra Space pushed the date back of Tenacity’s maiden flight to late this year. With Vulcan’s first mission set to happen then, and Dream Chaser launching on the second, this mission won’t be possible until at least a few months after Cert 1. This could delay it to early or even mid-2024.
On the bright side, ULA got a lot of testing done with the Cert1 Vulcan rocket before unstacking and shipping the upper stage. In March, the ULA team accomplished tanking demonstrations at Cape Canaveral Space Force Station, Florida. The pathfinder tests filled the Vulcan first stage and Centaur V upper stage with cryogenic propellant on separate days to validate performance of the stages, Vulcan Launch Platform (VLP), Space Launch Complex-41 facilities, and ground support systems. The tests, which also verified countdown steps, procedures and timelines, were successfully performed March 10 on the Vulcan booster stage and March 16 on Centaur V.
This led up to the Flight Readiness Firiing (FRF) that demonstrates the day of launch timelines and procedures, propellant loading operations, and the entire countdown through ignition of the twin booster engines at Space Launch Complex (SLC)-41. The firing generated a roar of nearly a million pounds of thrust, while Vulcan remained on the launch pad thanks to restraining mechanisms. The software program running in the rocket’s flight computer commanded engine shutdown to complete the FRF.
The two BE-4 engines underwent extensive acceptance testing at Blue Origin before delivery to the ULA factory for installation into the Vulcan rocket. FRF verified engine operations while coupled together with Vulcan to demonstrate engine start, throttle up, steady-state firing, and shutdown. The entire sequence lasted approximately 6 seconds. This milestone gave them the opportunity to observe critical elements of Vulcan as a complete rocket in the launch environment. It provided a rigorous performance check of the vehicle, pad systems, and the launch control team. The objectives included assessing the integrity and function of the main propulsion system, propellant feed systems, and engines. “FRF is really about confirming the operational readiness of the integrated system: launch vehicle, ground systems, facilities, and the associated software. In addition, we will demonstrate the ability to successfully execute the engine start sequence and validate our hot-fire abort response procedures,” said Dillon Rice, ULA’s Vulcan launch conductor.
Engineers studied temperatures, pressures, and other parameters while controllers monitored vital signs from Vulcan and send commands to the rocket and pad systems from the launch control center at the Advanced Spaceflight Operations Center (ASOC). The countdown matched normal launch day timelines and activities except the Certification-1 (Cert-1) mission payloads were not aboard nor involved. These different metrics combined with the test itself is why Tory Bruno and Blue Origin are not worried about the BE-4 engine explosion at the test stand.
In regard to the anomaly, Bruno said “I’m flattered by the attention we have now that a routine acceptance test was colorfully discussed on social media, but it really isn’t news”. This particular engine, he said, did not pass its first acceptance test, and was back on the test stand after changes when it exploded. “In this case, it didn’t pass it in a dramatic fashion,” he said, likely because the test thresholds were set too high. “It wasn’t able to automatically shut the engine down before the engine had a burnthrough. This doesn’t indict the qualification at all,” he said, noting that BE-4 engines have more than 26,000 seconds of cumulative runtime. “We’re very confident in the design and the workmanship of the assets that have passed acceptance. This is not unexpected.”
He also added that the production rate of the BE-4 is high enough that the test failure will not delay upcoming Vulcan launches. Blue Origin and other suppliers, along with ULA itself, are working to increase production to meet a rate of 25 vehicles a year by mid-2025, an initiative he called “25 in ’25.” Something we will likely get more updates on in the next few weeks.
Conclusion
ULA is in the process of upgrading all of its complete Centaur V upper stages after a weakness was found. This includes the Cert1 upper stage which is getting somewhat of a rough fix before being sent back to the site and tested for a launch late this year. We will have to wait and see how it progresses and the impact it has on the space industry.