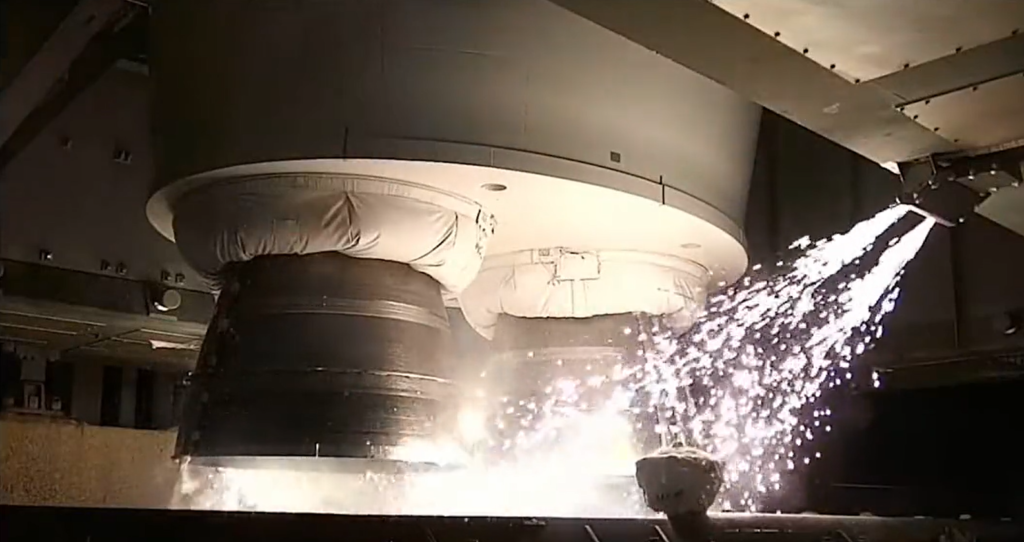
The BE-4 Engine Was Just Fired On Vulcan For The First Time
For years now both the Vulcan launch vehicle and the BE-4 engines have been going through constant development and testing in preparation for an initial launch. Yesterday they both passed the most important milestone yet with the successful completion of Vulcan’s Flight Readiness Firing. With this test done, there are only a few final steps before the long-awaited launch.
Specifically, ULA completed the first static fire of the two BE-4 engines. In total, they fired all the hardware for a few seconds and with very promising results. We have seen countless BE-4 static fires in the past but nothing on an actual launch vehicle only months away from lift-off.
While both the rocket itself and the BE-4 engines have had varying results in the past few years in the form of delays, this milestone is a good sign for both. Here I will go more in-depth into yesterday’s test, what’s left before the maiden flight, what to expect in the coming weeks, and more.
Vulcan Flight Readiness Firing
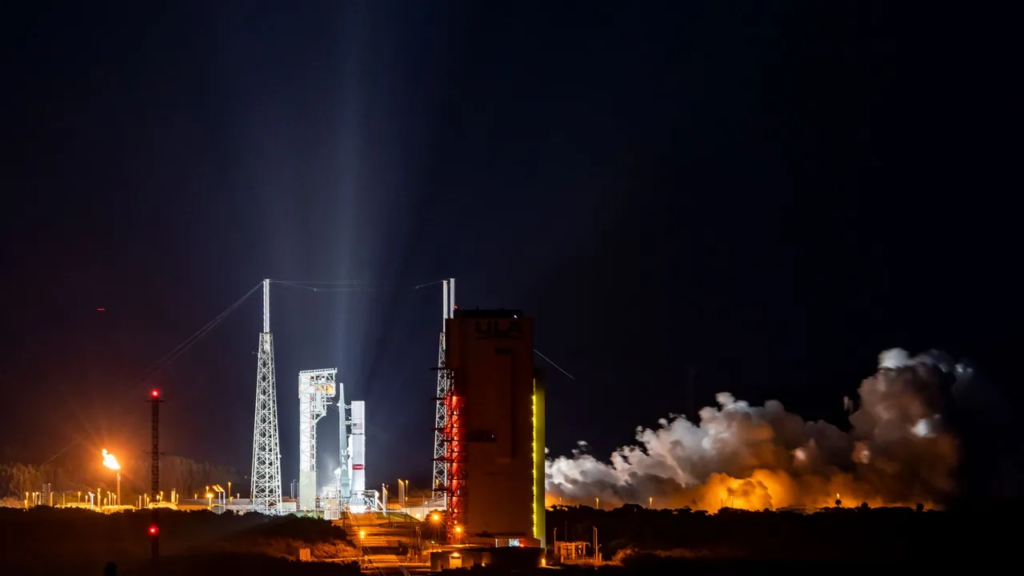
A full Flight Readiness Firing (FRF) demonstrates the day of launch timelines and procedures, propellant loading operations and the entire countdown through ignition of the twin booster engines at Space Launch Complex (SLC)-41. Just over a week ago on the 25th, ULA was scheduled to attempt this test however during the countdown, the team observed a delayed response from the booster engine ignition system that needed further reviewing prior to proceeding with the flight readiness firing.
Between then and now the teams at ULA addressed this issue and conducted the FRF. At first, there was a lightning event during the planned hold. This triggered a redline and re-test criteria. From here the teams ran it through the System Integration Lab, recycled, and headed back into the count. Finally, once the count got to 0 both BE-4 engines ignited for a few seconds before shutting off. ULA soon tweeted “United Launch Alliance successfully conducted a booster engine flight readiness firing (FRF) at Cape Canaveral Space Force Station, Florida. The engine start sequence began at T-4.88 seconds, the engines throttled up to the target level for two seconds and then powered down.”
In total, the entire FRF lasted for six seconds. Before this, the two BE-4 engines underwent extensive acceptance testing at Blue Origin before delivery to the ULA factory for installation into the Vulcan rocket. This milestone gives the opportunity to observe critical elements of Vulcan as a complete rocket in the launch environment. It provides a rigorous performance check of the vehicle, pad systems and the launch control team. Engineers studied temperatures, pressures and other parameters while controllers monitored vital signs from Vulcan and sent commands to the rocket and pad systems from the launch control center at the Advanced Spaceflight Operations Center (ASOC). The countdown matched normal launch day timelines and activities except for the fact that the Certification-1 (Cert-1) mission payloads were not aboard nor involved.
With this complete, ULA is more than 98% complete with the Vulcan qualification program, with the remaining items associated with the final Centaur V testing. In this case, the team is reviewing the data from the systems involved in today’s test and, in parallel, continuing with the Centaur V test stand anomaly investigation. Pending the data review and the investigation results, ULA will develop a plan for launch. They said in a statement that “Testing is an integral part of our launch vehicle development program, and we will fly when we believe it is safe to launch.”
In regard to this, a few months ago images came out of a large explosion at ULA’s test stand. ULA confirmed that during a Centaur upper stage test, H2 accumulated inside the rig, found an ignition source, and exploded. The overpressure caved in the forward dome and damaged the rig. The upper stage that exploded was not part of the hardware for the first launch, but the investigation needs to be completed before Vulcan is clear to fly. The launch was most recently scheduled in May however the most realistic and up to date timeframe is next month in July. ULA wants to make sure that whatever caused the test explosion has practically no chance of happening on the maiden flight of Vulcan. This will take time however the company is confident a month or so is all that’s needed.
Vulcan & BE-4
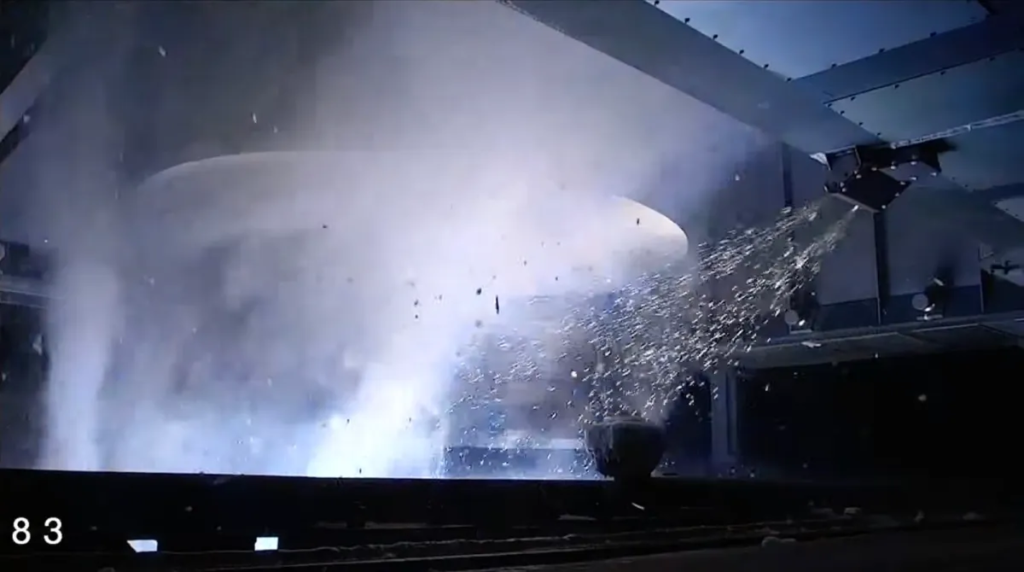
This test isn’t just a big deal for Vulcan but also the BE-4 engine and its extensive history. For over a decade now this engine has been in development. After years of manufacturing and testing, this was the first static fire on an actual rocket. It’s a good sign for the engine as Blue Origin begins ramping up production.
This being said, the BE-4 and Vulcan have had somewhat of a rocky relationship over the past few years. All the way back in 2014, it was announced that the engine would also be used on the United Launch Alliance (ULA) Vulcan Centaur launch vehicle. However, in the early 2020s is when some problems came up. In 2020, Tory Bruno stated that the second test BE-4 would be delivered soon, followed quickly by the first flight-qualified ones. He noted an ongoing issue with the BE-4’s turbopumps. At the time, Blue Origin was still troubleshooting the 75,000-horsepower pumps that bring fuel to the BE-4’s main combustion chamber, Bruno said, adding that he was confident the issues would be resolved soon. In October, Bruno stated that the issue was resolved and that the engine was moved into production. In the event, it was not, and would not be until 2022.
This among other issues came up around the same time which delayed operations for both the engine and the rocket. Finally late last year, Blue Origin announced that the first two BE-4 engines had been delivered to ULA and were in the process of being integrated on a Vulcan rocket. Soon after the engines were installed on the Vulcan test article and prepared for testing.
In terms of the recent test, Blue Origin tweeted saying, “A big congrats to our partner @ULALaunch on #VulcanRocket’s Flight Readiness Firing test. We’re proud to be part of this milestone. Did you know that each BE-4 engine provides 550,000 pounds of thrust at 100% power level?” The BE-4 is one of the most powerful liquefied natural gas (LNG) fueled rocket engine ever developed. The company chose LNG because it is highly efficient, low cost and widely available. Unlike kerosene, LNG can be used to self-pressurize its tank. Known as autogenous repressurization, this eliminates the need for costly and complex systems that draw on Earth’s helium reserves. LNG also possesses clean combustion characteristics even at low throttle, simplifying engine reuse compared to kerosene fuels.
BE-4 was designed from the beginning to be a medium-performing version of a high-performance architecture. A conscious design choice made to lower development risk while attempting to meet performance, schedule, and reusability requirements.
The Vulcan Centaur on the other hand, is expected to become ULA’s new workhorse and primary launch option. The spacecraft is encapsulated in a 5.4-m- (17.7-ft-) diameter payload fairing (PLF), a sandwich composite structure made with a vented aluminum-honeycomb core and graphite-epoxy face sheets. The bisector (two-piece shell) PLF encapsulates the spacecraft.
The Vulcan Centaur booster is 5.4 m (17.7 ft) in diameter and 33.3 m (109.2 ft) long. The booster’s tanks are structurally stable and constructed of orthogrid aluminum barrels and spun-formed aluminum domes. The Vulcan Centaur vehicle is controlled by an avionics system that provides guidance, flight control and vehicle sequencing functions during the booster and Centaur phases of flight. It also integrates up to 6 solid rocket boosters for additional power and capabilities.
ULA highlights that access to orbit remains a critical hurdle for many missions. However, this company is trying to provide flexible and cost-effective multi-manifest solutions to overcome this barrier. With multi-manifest, two or more spacecraft are integrated on a launch vehicle using available performance and volume margin that would otherwise go unused — optimizing mass to orbit and enabling missions. Multi-Manifest on a Vulcan rocket is expected to provide a highly reliable and schedule certain launch solution for spacecraft ranging from CubeSats to small sats and beyond.
Dependent on the size of the spacecraft, multi-manifesting on a Vulcan can be done in several ways. The Aft Bulkhead Carrier (ABC) interfaces at the aft end of the Centaur upper stage and can carry up to 24U CubeSats weighing 80 kg each. The Secondary Payload Adapter (ESPA Ring) is located between the upper stage and the primary payload and can accommodate 4-6 payload modules weighing up to 318 kg each.
This among other features is a result of the partnership and work between ULA and Blue Origin. With this test complete, the two companies are one step closer to the most significant milestone, launch.
Conclusion
Blue Origin and ULA have been working together for many years now ever since the BE-4 engine deal was made. While there were plenty of delays and issues along the way, the rocket and engines just completed the first static fire together successfully. We will have to wait and see how it progresses and the impact it has on the space industry.