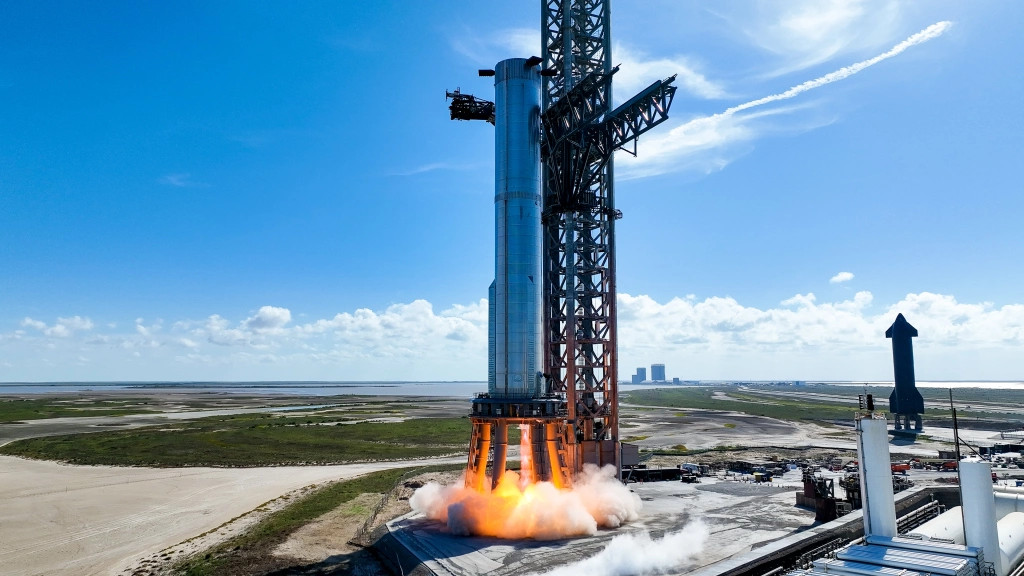
How A Steel Plate Could Solve SpaceX’s Starship Pad Issues
Since the first launch of Starship just a few days ago, quite a few things have changed at both the site itself and regarding the future of the program. One of the bigger topics of interest for the company is the launch site itself and the damage it sustained due to the power of the Raptor engines. As teams at SpaceX start to return to the pad, they will begin determining the scale of the damage and exactly what the next steps are.
However, even before this, we know that SpaceX’s main solution to the issue will be a massive water-cooled steel plate. This brings up the question of what exactly do they mean and how will a water cooled steel plate deal with both the strength and sound waves produced by 33 Raptor engines. Not to mention the additional damage to the surrounding Stage 0 infrastructure.
We also learned more about the damage to the orbital launch mount itself and SpaceX’s hopes for the pad going forward. Here I will go more in-depth into the application of a steel plate, the high water table and possible solutions, what to expect in the coming months, and more.
Steel Plate
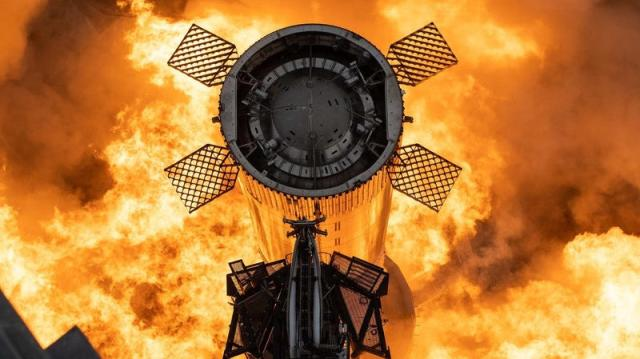
For a quick recap, recently Starship lifted off and for around 8 seconds the rocket was firing its Raptor engines onto the concrete below. This shot concrete and other debris hundreds of meters in every direction, creating a significant trench below the mount, stripping concrete from the mount supports, damaging the nearby tank farm, and possibly damaging the Starship rocket itself. Yesterday Elon tweeted a theory saying “Still early in analysis, but the force of the engines when they throttled up may have shattered the concrete, rather than simply eroding it. The engines were only at half thrust for the static fire test.” That past static fire had given them the confidence that the concrete would hold up, however, that was not the case.
With all of this in mind, SpaceX highlighted that prior to the launch they had already been planning to use a large water-cooled steel plate to deal with the flames and exhaust of the Raptors. In regard to this, Dr. Phil Metzger, a planetary scientist with quite a lot of experience, gave some insight into this process and how it could work. He commented that he used steel plates for some of the Morpheus launch locations so that they weren’t tied down to places with concrete. He analyzed the heating of the sheet and showed that the heat would redistribute fast enough that it would not locally melt on the surface, and that the steel plate was large enough to take the heat of the entire launch event without melting.
In reference to using this method for Starship, he was quoted saying, “For such a large rocket that much steel would be excessive. And ablative would not be enough to solve this, either. Would the ablative need to be 3 feet thick? He continued by saying, “But he said it will be water-cooled, which is an awesome idea. The water will be taking heat out of the steel in realtime so it won’t melt. Simple, and it should be effective.” This would also allow SpaceX to use much less steel as it won’t be needed to distribute the heat.
He then said, “So all that was just to say that I like the idea SpaceX is pursuing. I think it will work great to solve the plume erosion problem. It will *not* mitigate launch acoustics, however. The flat plate will reflect the sound back up along the sides of the vehicle, shaking the structure.” The very first “sound” that happens on launch is the shockwave from engine ignition. It bounces off the pad then runs up the sides of the vehicle, stressing everything. At NASA it is called the “Initial OverPressure” or IOP. To put in perspective the power of this, the IOP almost ruined the 1st Shuttle launch.
This is why the steel plate will need to be complemented by a significant water deluge system at Stage 0. On the first Space Shuttle launch the IOP deflected the elevons— the control surfaces on the wings — so far that the engineers were worried they could have snapped. So they added the water deluge system to absorb and break up the IOP shockwave. Considering the power of the Shuttle in comparison to Starship, it’s clear that during engine ignition as Starship was lifting off, it was producing immense sound waves that could have easily damaged it. He finished by saying, “If the rocket doesn’t mind the shaking, then fine. But it is easy to design systems that reduce launch acoustics and give more margin back to the vehicle, so if SpaceX decided to do so then it could be done.
Pad Damage Explained
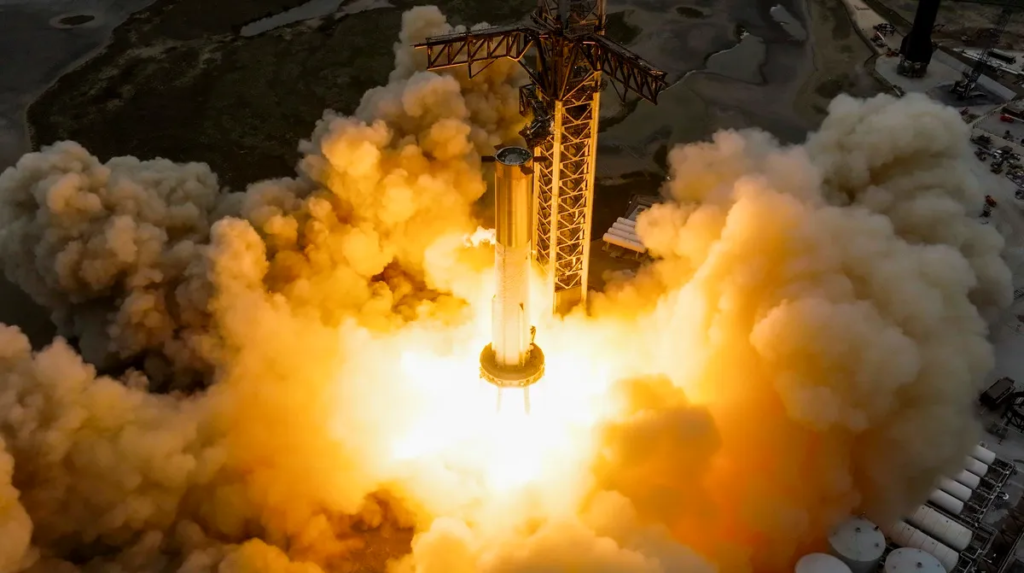
Images of the pad show not only a big trench, but massive concrete slabs completely missing after the launch. Dr. Phil Metzger commented that “One thing that people probably forget when building launch pads is that there is gas pressure pushing up from under the pad. Dirt has air pressure in it. If rocket exhaust finds a crack, it pressurizes the dirt under the launch pad far more. This can lift concrete slabs. If a slab starts to lift, it creates a bigger crack, and the gas that hits its edge comes to a full stop, converting its kinetic energy to super high pressure. This pressure is right at the crack so it drives even more gas to the space below the slab, lifting it even more. As concrete is eaten away it creates more paths for the gas to get through and under the concrete, and more disruption of the flow converting more kinetic energy into heat and high pressure, accelerating the process. This can run away in an uncontrolled pad failure.
When it comes to properly dispersing the exhaust of the most powerful rocket in the world, there are a lot of considerations that make it a difficult process. For one, it would be hard for SpaceX to build a large trench due to the high water table in Boca Chica. The water table is an underground boundary between the soil surface and the area where groundwater saturates spaces between sediments and cracks in rock. As a solution to this, you can build up the ground level quite a bit and then make a trench with the extra room. In SpaceX’s case, they already have set up all the Stage 0 infrastructure meaning we can expect everything to stay at the level it’s at currently. This is why the use of a large steel plate is the current plan. The plates are designed to sit directly on top of the water pipes, which are over 6 feet wide. Those pipes need to be buried underground for the plates to be at ground level.
For the Saturn V, designers who established criteria for the pads had wanted to keep the Saturn vehicle as close to the ground as possible in order to lessen wind stresses. They settled on a two-way, wedge-type flame deflector similar in design to those used on pads 34 and 37. The deflector, 13 meters in height and 15 meters in width, would weigh 317 tons. Since the water table was close to the surface of the ground, the criteria group wanted the bottom of the flame trench at ground level. The flame deflector and trench determined the height and width of the octagonal shaped launch pad; this in turn set the width of the space between the crawler treads, because the crawler straddled the pad.
During testing, they found that the launch complex 37 deflector, a copper, water-cooled, ridged model, suffered serious erosion from the concentration of heat and high gas velocities. Not long after, the preliminary designs for a steel deflector and for a reinforced concrete deflector had been completed. By means of instrument readings and motion pictures, the aerothermodynamic flow characteristics were determined, and the flame deflector and trench designs were refined. In designing the deflectors for launch complex 39 pads, it was necessary to have a replaceable leading edge which eroded but was insulated. Four types of deflector ridges were tested, using information gained in the study of heat-resistant shapes and materials for the Jupiter-C nose cone. When sufficient evidence was gathered, the design of the deflector proceeded with dispatch.
The selection of a refractory surface for the walls, floor, and an area outside of the flame trench was exact. The surface had to withstand temperatures of 1,922 kelvins and flame velocities four times the speed of sound. Special refractory fire bricks were held to the walls by interlocks, mechanical anchors, and a modified epoxy cement. All concrete surfaces protected by the brick had to have a smoothness tolerance of 0.3 centimeters in 3 meters to provide a bonding surface. This careful work was to limit the maximum temperature in the adjacent concrete structure during launch.
Now, SpaceX is working to figure out a system that can work near ground level for the most powerful rocket in the world. In terms of the mount and the damage it sustained, Elon Musk said, “All that’s left of the concrete lateral support beam is the rebar! Hopefully, this didn’t gronk the launch mount.” This highlights that the company is hoping to only need some repairs and not have to replace the entire mount. If a replacement is deemed necessary, this will add to the time before Stage 0 is up and running again and another launch attempt can happen. In the past, it took a decent amount of time to create that mount as it’s more complex than it looks. Either way, it’s likely that Stage 0 will be the limiting factor on when testing will begin.
Conclusion
SpaceX has a lot of work to do as they begin to head back to the site and evaluate the damage. The water cooled steel plate could solve the problem even without the use of a massive trench. However, this process will not be simple and will need to be perfect based on the pressure and dynamics of a launch pad. We will have to wait and see how it progresses and the impact it has on the space industry.