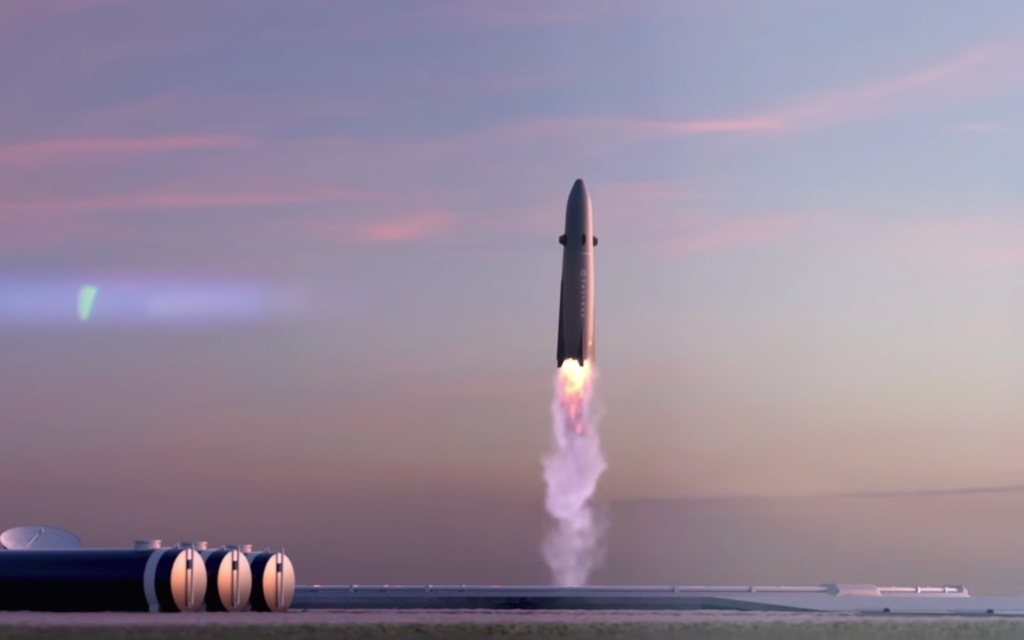
An In-Depth Look At Rocket Lab’s Neutron Launch Vehicle
For years now Rocket Lab has been trying to innovate and perfect small lift launch with the company’s Electron rocket. At this point in time, they are launching more frequently than ever before and from different locations around the world. While exciting, Rocket Lab is also in the process of developing, manufacturing, and testing an almost fully reusable medium lift launch vehicle.
The Neutron rocket is meant to thrive for constellation deployment but features interplanetary options and the possibility of even human missions. What it’s capable of is directly related to its unique design which Rocket Lab is taking a lot of freedom in working on. Even in the short period of time since the rocket’s original announcement, a lot has changed already.
Whether it’s the materials being used, the tapered rocket body, or the new engine under development, Neutron is trying to change how we access space. With a launch date still scheduled for next year, Rocket Lab has been working at an extremely rapid pace. Here I will go more in-depth into the design of Neutron, some of the big changes that have been made, important developments, and more.
A Unique Structure
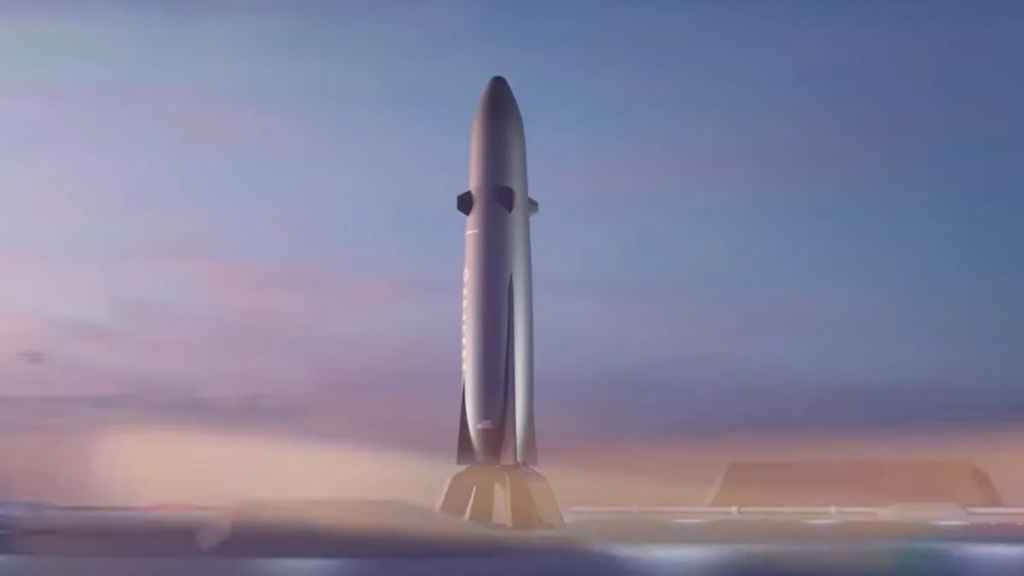
Looking at the design of Neutron whether it be from video animations or just images, highlights how different this rocket is from anything in the industry. The main reason for its odd shape and features comes down to Rocket Lab’s plan for the rocket. A quote from Rocket Lab CEO Peter Beck highlights this plan. He said, “Neutron is not a conventional rocket. It’s a new breed of launch vehicle with reliability, reusability, and cost reduction hard baked into the advanced design from day one. More than 80% of the satellites to be launched in the next decade are expected to be constellations, which have unique deployment needs that Neutron is the first vehicle to address specifically. Like we did with Electron, rather than starting with a traditional rocket design, we focused on our customers’ needs and worked back from there. The result is a rocket that is right-sized for market demand and can launch fast, frequently, and affordably.”
In order to achieve the perfect constellation deploying rocket, the company began with the general shape of Neutron. In this case, reusability is key to enabling frequent and affordable launch, so the ability to launch, land and lift-off again has been built into every aspect of Neutron’s design from day one. It starts with Neutron’s unique shape, a tapered rocket with a wide base to provide a robust, stable base for landing, eliminating the need for complex mechanisms and landing legs. This balanced structure also removes the need for bulky launch site infrastructure, including strongbacks and launch towers. Neutron will instead stand securely on its own legs for lift-off. After reaching space and deploying Neutron’s second stage, the first stage will return to Earth for a propulsive landing at the launch site, eliminating the high costs associated with ocean-based landing platforms and operations.
What makes Neutron’s design especially unique is the captive ‘Hungry Hippo’ fairing design. This innovative design will see the fairing form part of the first stage structure and remain fixed to the stage. Rather than separating from the stage and falling away to the ocean like traditional fairings, Neutron’s Hungry Hippo fairing jaws will open wide to release the second stage and payload, before closing again ready to return to Earth with the first stage. What lands back on the launch pad is a complete first stage with fairings attached, ready for a new second stage to be integrated and launched. This advanced design can speed up launch frequency, eliminates the high cost, low reliability method of capturing fairings at sea, and enables the second stage to be lightweight and nimble. Originally Neutron was going to have four fairing halves but that was reduced to just two not long ago.
Thanks to this ‘Hungry Hippo’ fairing design, the entire second stage will be completely enveloped within Neutron’s first stage structure and fairing during launch. Neutron’s second stage is designed to be the lightest in history to enable high performance for complex satellite deployments. Typically, a second stage forms part of the launch vehicle’s exterior structure and needs to provide strength to the vehicle from lift-off, exposing it to the harsh environments of the lower atmosphere during launch. By being housed inside the first stage and ‘Hungry Hippo’ fairing, the requirement for the second stage to withstand the launch environment is eliminated and the second stage can be made significantly lighter enabling higher performance in space. Designed as an expendable upper stage for now, Neutron’s second stage is a six-meter-long carbon composite structure with a single vacuum optimized Archimedes engine.
We even got multiple sneak peeks and hints at a possible future crewed variant of Neutron. This being said, they stressed that this was simply an option and at the moment there was no actual plan for this. Although, assuming initial launches go well and Neutron performs as expected, we could see it launching humans many years from now.
Neutron Developments
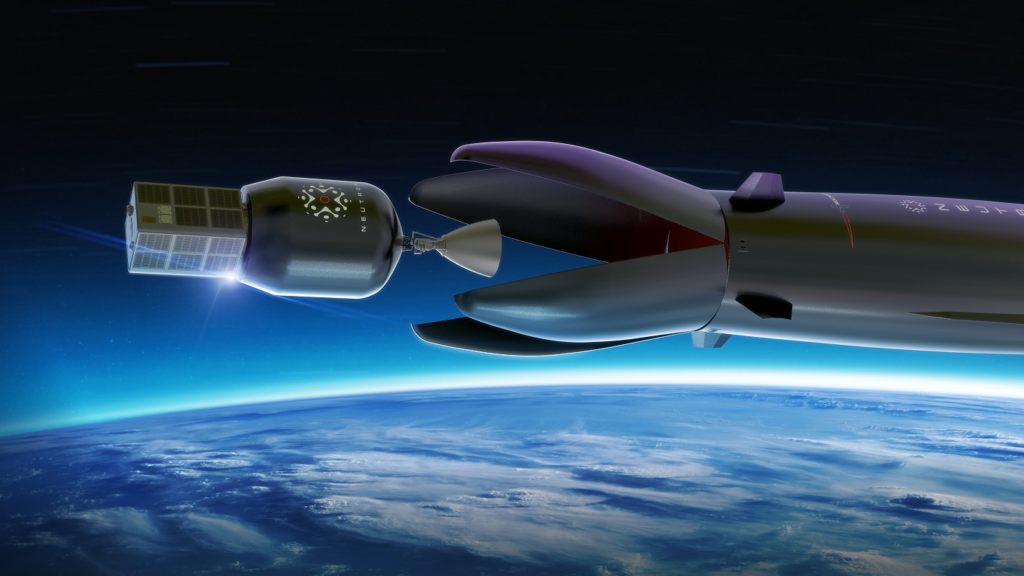
Standing at 43m (141ft) tall and featuring a base width of 7 meters, Neutron is a significant upgrade from Electron. Neutron has a payload capacity ranging from 8 to 15 tons depending on the mission profile. For example, 8 tons to LEO when Neutron returns to the pad, 13 tons when Neutron lands down range, and 15 tons when expendable. This variability provides a lot of options depending on the customer and what they require.
In terms of developments, both the general structure materials and the engines have both made impressive progress. Starting with the propulsion, Neutron will be powered by an entirely new rocket engine, Archimedes. Designed and manufactured in-house by Rocket Lab, Archimedes at first was planned to be a reusable liquid oxygen / methane gas generator cycle engine capable of 1 meganewton thrust and 320 seconds of ISP. In addition, only seven of these engines were expected to be used on the first stage. Practically all of this has changed since then, however. Looking at the updated stats, the vacuum engine features an ISP of 367 seconds, and the sea level ISP is 329 seconds. The ISP is the specific impulse and a good way to determine the efficiency of a rocket engine.
They then announced the change from a gas generator cycle to oxidizer rich closed cycle because as they worked through the content of operations and did all the power balances, they found turbine temperatures that were too high, a low amount of margin, and the need for a lot of compromises. Lastly, instead of just 7 of these engines powering the first stage, there will instead use 9. Neutron’s lightweight carbon composite structure means Archimedes does not need the immense performance and complexity typically associated with larger rockets and their propulsion systems. By developing a simple engine with modest performance requirements, Rocket Lab is confident the timeline for development and testing can be drastically accelerated. Back in January of this year, the company tested engine ignition on dev hardware. Soon we should expect to hear more about hot firing hardware with full propellant flow rates to verify injector performance.
The other big development besides the Archimedes engine has to do with the materials being used. Neutron will be the world’s first carbon composite large launch vehicle. Rocket Lab pioneered the use of carbon composite for orbital rockets with the Electron rocket, which has been delivering frequent and reliable access to space for government and commercial small satellites since 2018. Neutron’s structure will be comprised of a new, specially formulated carbon composite material that is lightweight, strong, and meant to withstand the immense heat and forces of launch and re-entry again and again to enable frequent re-flight of the first stage. To enable rapid manufacturability, Neutron’s carbon composite structure will be made using an automated fiber placement system which can build meters of carbon rocket shell in minutes. This exact process we have already seen quite a bit of progress in. For months now we have been receiving the occasional update from Rocket Lab of physical Neutron test tanks being worked on and completed. This technology and process connects to the final main piece of the Neutron rocket, which is its factory.
The Neutron Production Complex and launch pad for the Neutron rocket is located at the NASA Wallops Flight Facility and Mid-Atlantic Regional Spaceport on Virginia’s Eastern Shore. The Neutron Production Complex will be home to a rocket production, assembly, and integration facility, as well as a dedicated launch pad for the Neutron rocket located on the southern end of Wallops Island. The estimated 250,000 square foot state-of-the-art complex is being constructed on a 28-acre site adjacent to the Wallops Island Flight Facility and will include a Launch Control Center, Rocket Lab’s fifth global operations center for launch activities and on-orbit operations. Commercial and government interest in Neutron is strong and includes a recent $24 million development contract granted by the U.S. Space Force’s Space Systems Command (SSC) in support of Neutron’s capability to aid national security and defense missions ranging from scientific and experimental satellites to the largest and most critical national security payloads. Further Neutron expansion will continue throughout the United States as the program develops toward its first launch.
Conclusion
Rocket Lab is hard at work trying to create the future of constellation deploying rockets within the industry. Neutron is very different from anything else within the industry and will be an exciting rocket to keep up with as time goes on. We will have to wait and see how it progresses and the impact it has on the space industry.