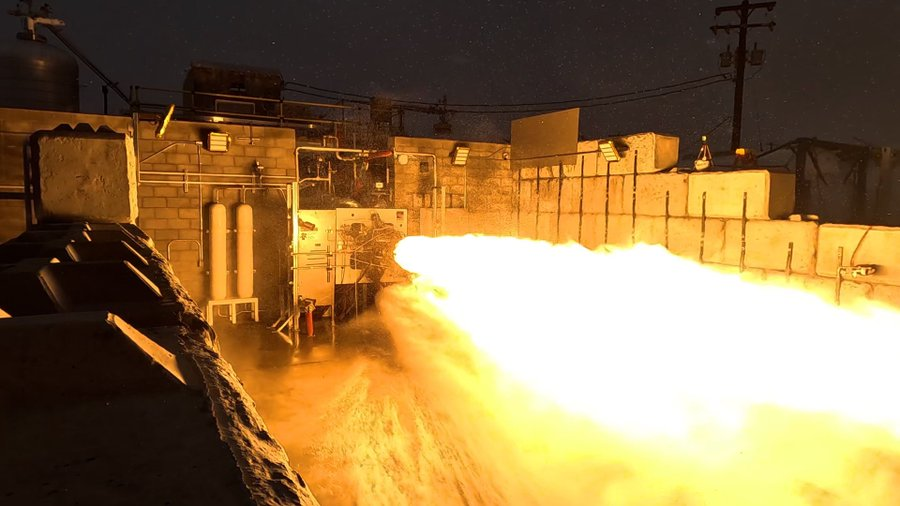
Astra’s New Engine Completes Major Development Test
Astra Space is continuing to work toward the first launch of Rocket 4. Not long ago the company officially canceled the Rocket 3 line after inconsistent results and the most recent launch failure on the TROPICS Mission. With the new rocket development comes various similarities and differences to Rocket 3, with one of the main changes revolving around the first stage engines.
Specifically, Rocket 4 will now feature two turbopump-fed engines rather than the five battery pump-fed engines used on the Rocket 3 line. In terms of progress, just a few days ago these new engines achieved a full mission duty cycle firing. A major step in the development and future application of this hardware. With a launch date goal of late this year, Astra will need to continue with this accelerated pace.
One of the most interesting parts about these new engines has to do with a possible partnership. Various reports highlight that these new engines have to do with Firefly Aerospace and already have a decent flight heritage. Something that could be very beneficial to Astra going forward. Here I will go more in-depth into the most recent successful test results, the history of these new engines, why they are so important, and more.
New Engine Test
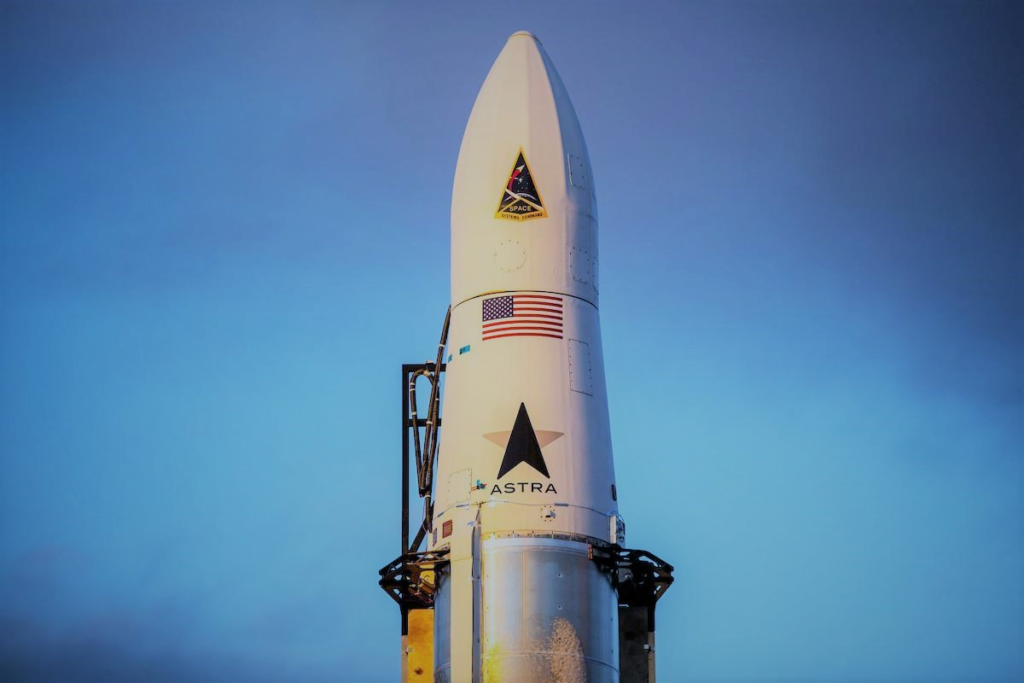
Only a couple of days ago on the 31st, Chris Kemp, Astra CEO tweeted saying, “Rocket 4 first stage engine full mission duty cycle of 175 seconds achieved – a major development milestone for Rocket 4” This included a 3 minute long video of the hot fire from start to finish. The last time we were updated on this engine’s progress was in September of last year when the company released footage of an initial 20 second hot fire. In the time since then, they continued to work on the engine and now have completed a full cycle successfully.
The Rocket 4 first stage is powered by two turbopump-fed LOX engines, each with an expected maximum sea level liftoff thrust of 40,000 lbf. The engine features a regeneratively-cooled combustion chamber operating at over 1,000 psia chamber pressure which is fed by a turbopump. Each engine can gimbal to provide vehicle steering and control. In addition, actuation of the Thrust Vector Control actuators is “fueldraulic”, powered by high-pressure fuel tapped off from the main fuel circuit. Fueldraulic actuation simplifies the vehicle as it does not require an external high-pressure or high-voltage source for actuation systems that require significant power. The pyrophoric ignition of the engine is ground-based, eliminating another plumbing system from the vehicle and further reducing cost, weight, and complexity. Astra also points out that they are developing and qualifying an upgraded derivative of a previously qualified engine for this application.
What’s most interesting about this engine and the relation to this comment from the company has to do with some reports made back in September of 2021. Here, a few different news agencies reported on a deal between Firefly Aerospace and Astra. Supposedly, Astra signed a roughly $30 million deal for the rights to manufacture Firefly’s Aerosapce’s Reaver engine which is used on the first stage of Alpha. They reported that within this deal which was closed earlier in 2021, Firefly would send 50 Reaver engines to Astra’s factory. From here, the company would make some changes and adjustments as they see fit. This means we could be seeing Reaver derived engines built by Astra. While Astra as a company has still not commented on this information, there are definitely some similarities between this engine and Reaver.
For one the engines look very similar. Firefly Aerospace has quite a bit of footage of the Reaver engine and they are not far off from this recent Astra test fire. The other similarity has to do with the sound. At the start of Astra’s static fire, you can hear a very unique engine start up sound that is similar to what you hear at the start of Firefly Aerospace’s first orbital test flight and other engine tests. These reasons among others are why many people are confident a deal was made between the two companies. In reality, this is quite a good thing for Astra as they need capable and reliable hardware going forward. Rocket engines are extremely complex and important pieces of equipment that they practically already have under control for Rocket 4.
Rocket 4
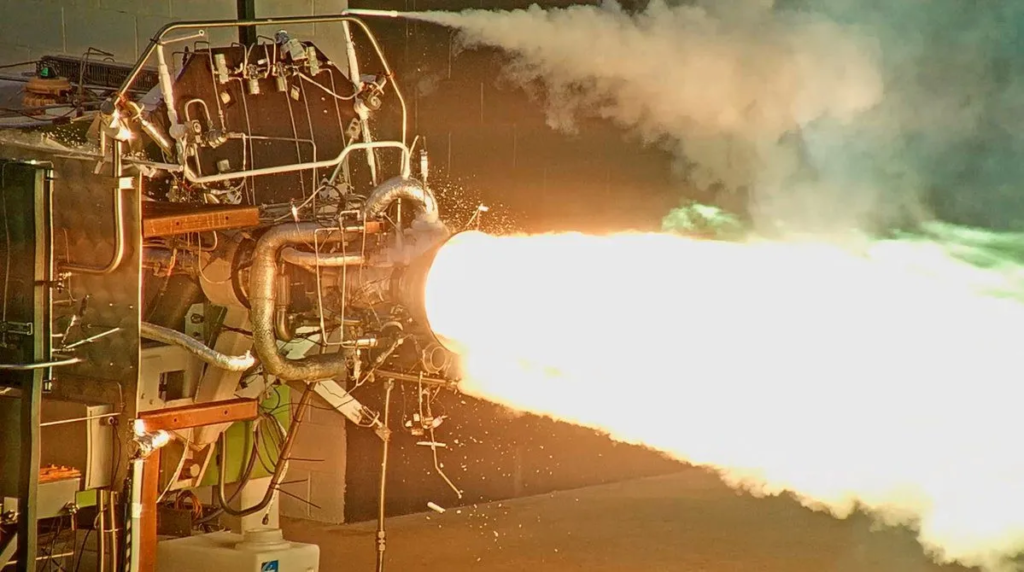
Now that we know more about the most recent Rocket 4 first stage engine fire, we can take a closer look at the rocket itself and what Astra has planned going forward. When focusing on the structure and various features of Rocket 4, you can see a lot of similarities to the Rocket 3 line with some changes as well. The structure of Rocket 4 is built entirely from metal, with design choices optimized to produce rockets efficiently at scale. Astra is trying to focus on simple and proven manufacturing techniques that result in lightweight structures throughout the vehicle: e.g. skin-and-stringers instead of milled isogrid and sheet metal in place of costly additive manufacturing.
Throughout the vehicle, they have incorporated mass-saving features such as common dome tank designs and submersed helium tanks. The first stage consists of two cylindrical tanks, enlarged relative to the Rocket 3 series, but using the same proven design and fabrication approach. The LOX and fuel tank are an aluminum common dome tank set, designed and qualified in-house. The longitudinal seams are friction stir welded and the circumferential seams are TIG welded. The domes are now formed directly from thin sheets of aluminum, and the cylinders are rolled sheets.
The upper stage has also gone through a few changes including its engine. Specifically, the upper stage has undergone the largest architectural change from Rocket 3.3. Rocket 4’s upper stage has moved to a full-diameter, common dome design – which aligns production approaches between the two stages – increasing build reliability and decreasing total manufacturing costs. Taking over following stage separation, the upper stage engine is a turbopump-fed engine with a vacuum thrust of approximately 6,500 lbf. The upper stage engine is a high-performance LOX engine that propels the upper stage and payload into orbit. It can be restarted prior to payload deployment to enable upper stage circularization and after payload deployment to lower the upper stage’s orbit. The engine, which is being qualified for Astra’s use, is also a derivative of an existing qualified engine.
In terms of performance, Rocket 4 is designed for a nominal payload capacity of approximately 500 kilograms to a circular 500 km altitude Sun-synchronous orbit (SSO). Astra intends to initially operate the vehicle with de-rated engines in order to reduce initial system performance risks and schedule risks. This leads to an introductory payload capacity in 2024 of approximately 350 kilograms to a circular 500 km altitude Sun-synchronous orbit. The expected and initial de-rated 2024 payload capacities for additional inclinations include 550kg to LEO. As they gain data from ground testing and early flights, they expect to reduce the engine de-rating which will increase the payload capacity of the launch vehicle.
In the past with the Rocket 3 line, we saw various issues with the upper stage and the payload fairing in particular. This is an area Astra is working to improve and make consistent for Rocket 4. Rocket 4 will be configurable with two standard payload attach fittings to serve a single ESPA Large payload or two ESPA standard payloads. Secondary payload adapters can be utilized to serve multi-manifest missions (e.g. multiple cube sat dispensers for a rideshare mission) which are customized with an interface bolt pattern based on customer mission requirements. As a non-standard service, Astra is also able to design custom adapters if the footprint of the payload plate is insufficient to accommodate the desired payload interfaces. They offer the ability for payload integration to take place at the launch site, and can also provide the Rocket 4 payload adapter plate to the customer for the customer to complete integration at their own facility, separate from the launch vehicle.
Altogether, Rocket 4 is an expendable, vertically-launched two stage LOX/kerosene rocket, optimized for reliability and manufacturability, and built to significantly reduce the cost of dedicated orbital launches.
Rocket 4 is the product of extensive learning that took place during the design, manufacturing, and launch of the prior Rocket 3 series. With much of its architectural heritage coming from the Rocket 3 series, Rocket 4 is trying to capitalize on Astra’s existing flight heritage, while fine-tuning the rocket for improved reliability and manufacturability. Astra believes they are a completely different company than when it designed Launch System 1 and that shows in the level of investment they’re making into the reliability of this system. The entire system has been scrutinized, and re-engineered where necessary, to support plans to reliably and repeatably deliver their customers’ payloads to orbit. This shift encompasses every stage of the development process, with multiple teams in the organization focused primarily on reliability, quality, and system safety.
Conclusion
Astra Space is making significant progress toward the first launch of Rocket 4 still set to happen later this year. Just days ago they announced the successful completion of a full mission duty cycle using the new first stage engine. A very important milestone that could determine the future success of this rocket and even the company. We will have to wait and see how it progresses and the impact it has on the space industry.