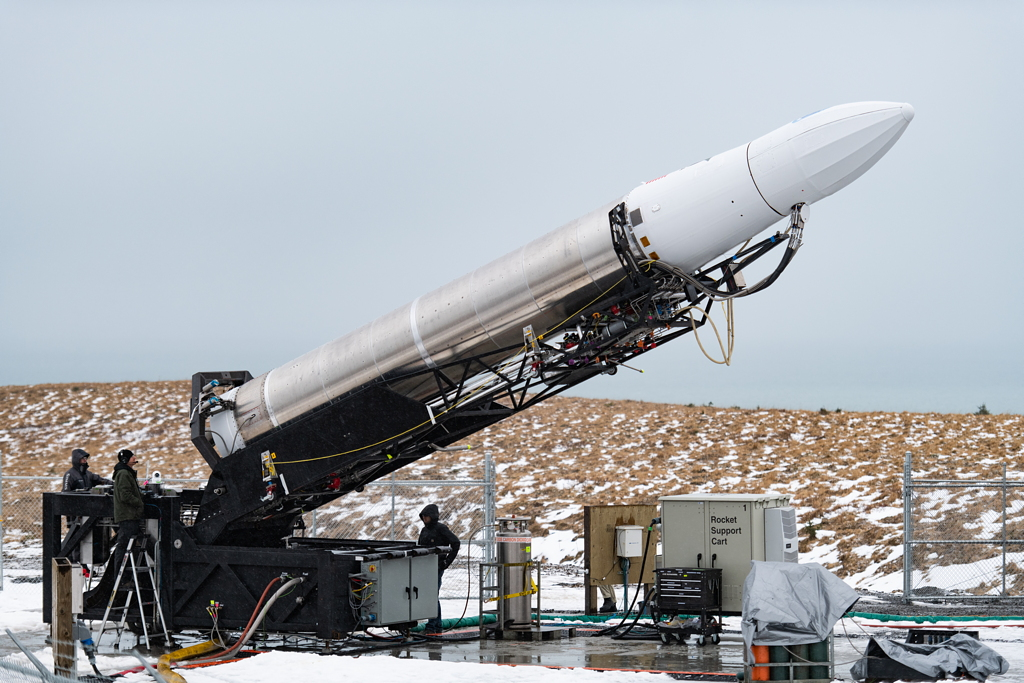
Astra Space New Developments On Engines & Rocket Manufacturing
Astra Space is trying to turn things around and produce a new and improved launch vehicle. After quite a few failed launches with the Rocket 3 line, they made the decision to stop launching and move on to Rocket 4. Not to mention an additional shift in the entire launch process with new goals, ways of approaching small launches, and speed, just to name a few.
Just in the last couple of weeks, the company has announced even more updates on both the future launch vehicle and its spacecraft engine technology. An aspect of Astra Space that is becoming much more important without any launches available. These updates included more information on the welding process and more infrastructure for various spacecraft technology.
While Astra Space has had a bit of a rough last few years, they are confident that they have learned from their mistakes and will come back much stronger in 2023. However, before this becomes a reality they have a lot of work to do starting with getting Rocket 4 ready for testing. Here I will go more in-depth into the company’s recent welding and spacecraft engine update, its plan for the future, what to expect in the coming months, and more.
Recent Updates
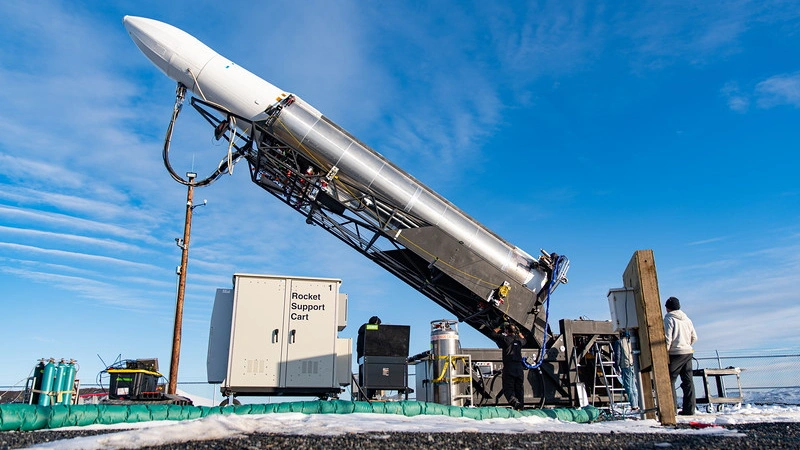
Starting just earlier this month on December 9th, Astra Space tweeted saying, “Building a scalable system includes having simplicity and consistency in our production process. Enter our new Friction Stir Welder: responsible for all of the vertical weld seams on Rocket 4’s tank sections.” This included a short video going over the new system and process that Astra is using. They also commented in another tweet mentioning, “With the transition to a common diameter upper stage, this new tooling will help Astra automate and scale both first stage and upper stage Rocket 4 tank production.”
Rocket 4 is the product of extensive learning that took place during the design, manufacturing, and launch of the prior Rocket 3 series. With much of its architectural heritage coming from the Rocket 3 series, Rocket 4 capitalizes on Astra’s existing flight heritage, while working to fine-tune the rocket for improved reliability and manufacturability. Astra has focused on building its rockets using proven and cost-efficient metallic structures, leveraging multidisciplinary production techniques and eschewing labor- intensive processes such as carbon composite layups. These techniques allow for rapid manufacturing and reduced production costs, which are realized in lower launch costs to customers.
In addition to work on Rocket 4, the company also released more information regarding its spacecraft engines. Only 3 days ago on the 16th, Astra Space tweeted highlighting, “Earlier this month, we received our three-station Astra Spacecraft Engine™ test chamber, which will allow us to increase engine testing throughput and production capacity. Stay tuned for more updates on our new spacecraft engine facility in 2023!” This also included a short video of the new system being delivered and installed. Ever since Rocket 3 was canceled, we have seen more activity on various sources of income from the company such as spacecraft engines. This includes more contracts and work on the system.
One month ago in October, Astra announced that it had reached an agreement with Astroscale Holdings Inc (“Astroscale”), to provide Astra Spacecraft Engines for its space sustainability spacecraft platform, ELSA-M, that can safely and responsibly capture and retire multiple client satellites in a single mission. This satellite servicer will be designed and optimized to remove multiple pieces of debris from LEO in a single orbital mission. The development of this satellite commercial service is supported by the UK Space Agency and European Space Agency as part of the ESA Sunrise program.
Not to mention, only a few days before this announcement, Astra announced that it has reached an agreement with Maxar Technologies (“Maxar”) to supply Astra Spacecraft Engines. The propulsion systems will be used in Maxar’s proliferated low Earth orbit (LEO) spacecraft, which support a wide variety of global coverage missions, including Earth observation, communications, and national security. Astra expects to begin delivery of its spacecraft engines in 2023. “The Astra Spacecraft Engine’s™ flight heritage, high performance, and high reliability were critical in our decision-making process as we prepare to deliver our spacecraft platforms to customers for their critical missions,” said Joe Foust, Maxar Vice President of proliferated LEO Programs.
Launch System 2.0
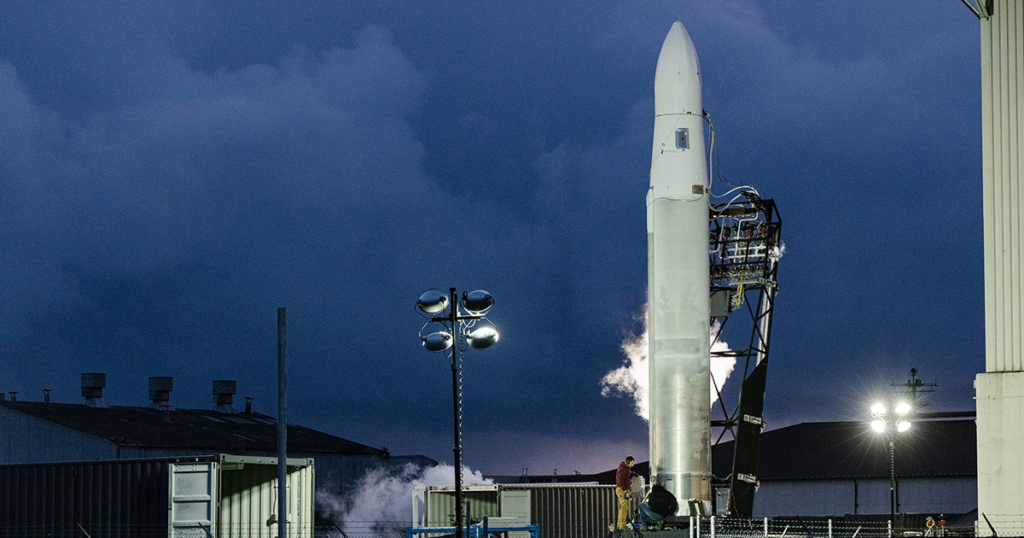
Now that we know more about some of the recent updates on Rocket 4 and Astra’s spacecraft engines, we can take a closer look at the exact plan and design of these core company components. The recent update regarding friction stir welding is quite a big deal for the company. To put it in perspective, the structure of Rocket 4 is built entirely from metal, with design choices optimized to produce rockets efficiently at scale. They are trying to focus on simple and proven manufacturing techniques that result in lightweight structures throughout the vehicle: e.g. skin-and-stringers instead of milled isogrid and sheet metal in place of costly additive manufacturing.
Throughout the vehicle, they have incorporated mass-saving features such as common dome tank designs and submersed helium tanks. The first stage consists of two cylindrical tanks, enlarged relative to the Rocket 3 series, but using the same proven design and fabrication approach. The LOX and fuel tank are an aluminum common dome tank set, designed and qualified in-house. The longitudinal seams are friction stir welded and the circumferential seams are TIG welded. The domes are now formed directly from thin sheets of aluminum, and the cylinders are rolled sheets. Helium COPVs are submerged in the fuel tank for packaging efficiency. The tank includes slosh baffles and anti-vortex devices. The upper stage is now essentially a shorter version of the first stage, utilizing the same welding techniques on a similar architecture, though a number of elements are further weight optimized given the increased weight sensitivity of the stage. Like the first stage, it is a common dome assembly with Helium COPVs submerged in the fuel tank.
In addition, one of the biggest updates that Astra released in the past couple of months was progress on its new Rocket 4 main engine. The Rocket 4 first stage is powered by two turbopump-fed LOX engines, each with an expected maximum sea level liftoff thrust of 40,000 lbf. The engine features a regeneratively-cooled combustion chamber operating at over 1,000 psia chamber pressure which is fed by a turbopump. Each engine can gimbal to provide vehicle steering and control. Actuation of the Thrust Vector Control actuators is “fueldraulic”, powered by high-pressure fuel tapped off from the main fuel circuit. Fueldraulic actuation simplifies the vehicle as it does not require an external high-pressure or high-voltage source for actuation systems that require significant power. The pyrophoric ignition of the engine is ground-based, eliminating another plumbing system from the vehicle and further reducing cost, weight, and complexity. Astra is developing and qualifying an upgraded derivative of a previously qualified engine for this application. The company’s past engine was responsible for a few issues on Rocket 3 launches and Astra is trying to change that going forward.
Astra makes it clear that they are a completely different company than when Launch System 1 was designed and that shows in the level of investment they’re making into the reliability of this system. The entire system has been scrutinized, and re-engineered where necessary, to support their plans to reliably and repeatably deliver they customers’ payloads to orbit. This shift encompasses every stage of the development process, with multiple teams in the organization focused primarily on reliability, quality, and system safety. They’re better-resourced across the board than they were during the development of Launch System 1, including the creation of a new System Verification and Assurance team, quality control lab, and failure analysis lab with state-of-the-art testing capabilities. It’s important to point out that a reliable launch system is about much more than just a rocket, it’s about creating an integrated system that works seamlessly together. The Astra launch system is comprised of three key subsystems: The Rocket – the launch vehicle itself, which ultimately delivers payloads into their final orbit The Ground System – the infrastructure on the pad when Astra launches. And Mission Control – the interface between their operators and the rocket.
Astra’s goal with Launch System 1 was to achieve orbital capability as quickly as possible and demonstrate that we could mass-produce rockets. Following the flight anomaly on their last launch, the company says they listened to their customers, their team, and their stockholders and made the strategic decision to accelerate the introduction of a higher performance rocket and add additional testing that they believe will increase the reliability of future launches. Now as 2023 approaches, they need to execute.
Conclusion
Astra Space is trying once again to reach orbit with a new launch vehicle. This time around they are making very big changes and quite a few updates are being made. We will have to wait and see how it progresses and the impact it has on the space industry.