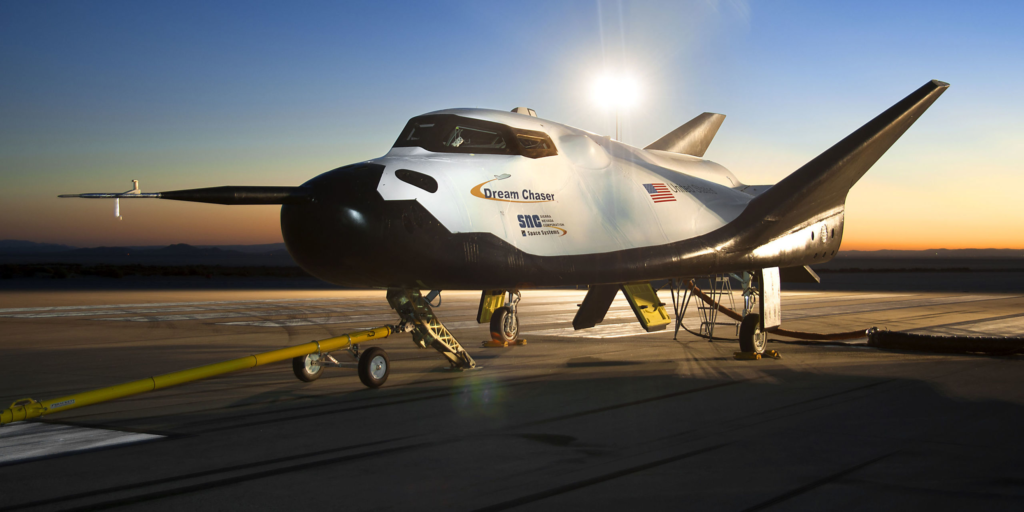
The Thousands of Tiles Protecting Dream Chaser Tenacity On Its First Launch
Sierra Space is closer than ever to the first launch of Dream Chaser Tenacity, the company’s first test article set to launch in the near future. One of the most essential parts of this next generation spacecraft and the current project being undertaken is its thermal protection system. In total Dream Chaser features thousands of thermal tiles across the body of the spacecraft trying to ensure it withstands the forces upon reentry.
Since October of this year, Sierra Space has been busy applying these tiles to the spacecraft in preparation for its first launch to the International Space Station under a significant NASA contract. During reentry, the spacecraft will face temperatures around 3,000 degrees Fahrenheit or 1650 degrees Celcius.
In the past spacecraft such as the Shuttle experienced a few different issues relating to its thermal protection system. This is an especially important and complex component of reusable spacecraft. In Dream Chaser’s case, Sierra Space plans to reuse it quite a few times over the course of its life. Here I will go more in-depth into the design of Dream Chaser’s tiles, their importance, what to expect in the coming months, and more.
Dream Chaser’s Heat Shield
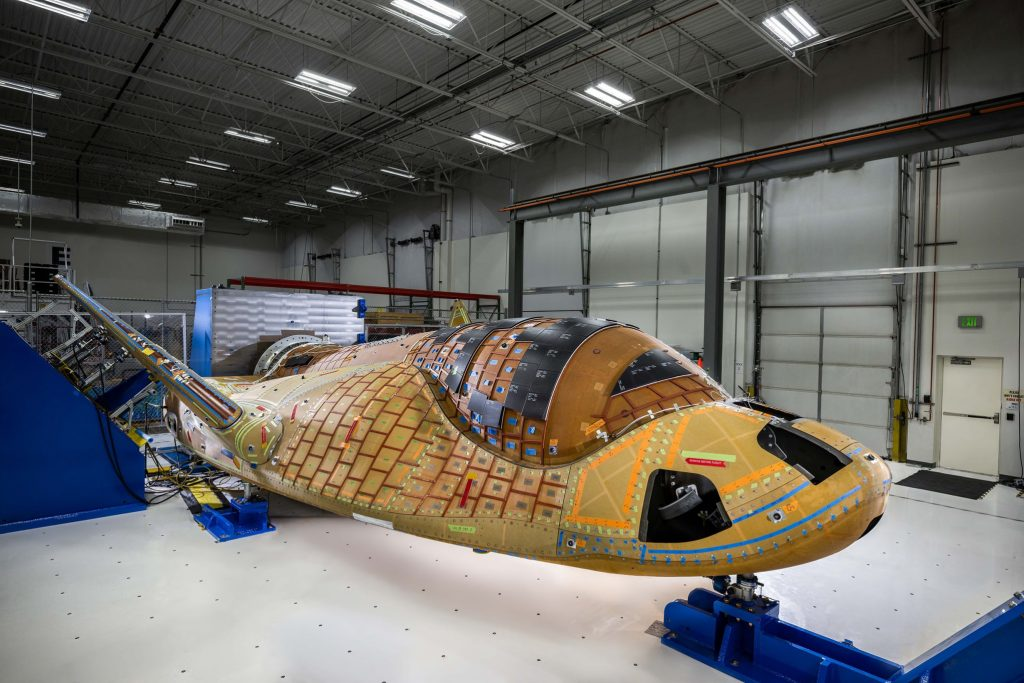
By now as we head towards the middle of December, Dream Chaser Tenacity is not far away from being complete. One of its most important features, its heat shield, is currently being installed by the team at Sierra Space. For reference, back in October the company tweeted saying, “Right now, our Dream Chaser team is hard at work affixing more than two thousand hand-cut thermal tiles. We’ll have more photos and close-ups of Tenacity coming soon.”
Dream Chaser is a spaceplane hoping to transport both crew and cargo to and from low Earth orbit in the coming years. Currently, its first launch is scheduled for the third quarter of 2023. For years now Sierra Space has been working to develop and create a new and improved heat shield capable of protecting the spacecraft upon re-entry. To be specific, around 2,000 of these tiles will protect Dream Chaser from temperatures that could reach upwards of 3,000°F on entry, while keeping the vehicle itself at only 350°F. One unique aspect of these tiles is their different colors depending on their location on the spacecraft. In this case, the white tiles reject more heat from the sun while on-orbit, which helps to keep the components within Dream Chaser cooler. As for size, Dream Chaser is about 30 feet long, or about ¼ the total length of the space shuttles. In comparison, more than 24,000 tiles were used on NASA’s space shuttle orbiters.
Back in 2015, Sierra Nevada Corporation (the parent company of Sierra Space) successfully completed several significant Thermal Protection System (TPS) material development tests for its Dream Chaser spacecraft. The TPS tests were completed at NASA’s Ames Research Center and Johnson Space Center under reimbursable Space Act Agreements (SAA). The tests provided critical data needed to support the TPS subsystem Critical Design Review (CDR) and to validate Dream Chaser TPS manufacturing readiness.
At the time, the corporate vice president of SNC’s Space Systems commented, “Safety of crew and cargo is most important to our team as we continue to mature the spacecraft design. For several years, we have worked collaboratively with Johnson and Ames, leveraging their existing infrastructure, materials, and expertise to mature and customize the TPS for our unique spacecraft. Our TPS is lighter, stronger, and more efficient than previous generations. We have met or exceeded all mission requirements. We are now prepared to enter the Critical Design Review phase for this system.”
As far as the tests themselves, over 100 arc jet cycles and radiant heat tests were completed at Johnson’s Radiant Heat Test Facility (RHTF) and Ames’ Aerodynamic Heating Facility (AHF). RHTF provided results supporting thermal characterization of the developmental TPS materials. The test data was then used for thermal modeling, analysis, and TPS sizing. The Ames AHF arc jet tests were performed as a second phase in the development testing to gauge the material performance in environments simulating Dream Chaser flight conditions. Valuable arc jet test results supported SNC’s certification of the manufacturing capability of a high-temperature material called Toughened Uni-Piece Fibrous Reinforced Oxidation-Resistant Composite TUFROC. TUFROC will be used on the high-temperature nose and wing leading edges of the Dream Chaser spacecraft.
TPS Importance
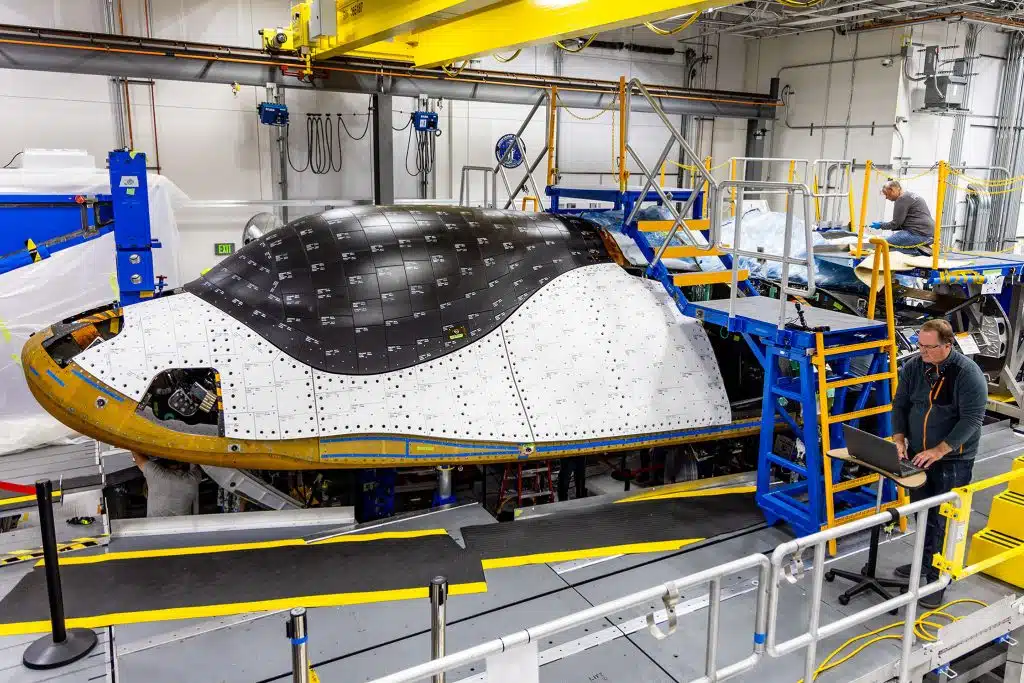
Now that we know a bit more about some of the testing completed in previous years for the spaceplane’s heat shield, we can take a closer look at its current application. Recently Sierra Space has provided some new images of Dream Chaser with a majority of its tiles installed. This gives us a better idea of what they are trying to achieve. In these images, you can see that practically every tile is unique and is meant for an exact spot on the spacecraft. In order to keep the tiles on Dream Chaser, Sierra Space’s engineers use room temperature vulcanizing (RTV) silicone. RTV silicone is able to withstand high temperatures, making it perfect for bonding the tiles. Each tile is tested by using a mechanism that pulls on them, which ensures the bond is sufficient.
The company also highlights that SNC engineers have been able to update the TPS tiles from what was used during NASA’s shuttle program with more innovation, better technology, and utilizing lessons learned. They use more modern manufacturing techniques to increase strength and reduce cost. Another difference between the tiles is Dream Chaser tiles are about 10 inches by 10 inches, while those on the shuttle were six inches by six inches. Dream Chaser is also smaller in size, which also means fewer tiles to replace in general. Not to mention, Dream Chaser tiles are stronger and lighter weight than those used during the shuttle program and meet all Micro-Meteroid Orbital Debris (MMOD) requirements to ensure safe entry, descent, and runway landings for crewed or cargo missions.
In the past, SNC also simulated re-entry environments to measure the thermal performance of new silica tile coating developed by NASA and SNC. SNC’s assessments showed that these new coatings offered the same thermal protection as previously flown tile coatings, but at a greatly reduced cost. All of which in an effort to make Dream Chaser not only capable of safely entering Earth’s atmosphere, but also to facilitate a quick and cost effective turnaround for the next mission.
Dream Chaser is a next generation spaceplane trying to change how we access space. This spacecraft features both a crewed and uncrewed variant. The crewed version of Dream Chaser is approximately 85% common to the cargo system. The main differences are environmental control and life support systems, windows for crew visibility, an integral main propulsion system for abort capability, and major orbital maneuvers. This and the fact that when being launched into space, the crewed version will not have a payload fairing while the uncrewed variant will.
Not too long ago NASA selected Dream Chaser to provide cargo delivery, return, and disposal services for the International Space Station. Under the Commercial Resupply Services 2 (CRS-2) contract, Dream Chaser will provide a minimum of seven cargo service missions to and from the space station. The first of these missions is expected to happen late next year on top of United Launch Alliance’s Vulcan Centaur. To meet CRS-2 guidelines, the cargo Dream Chaser will have folding wings and fit within a 5 m diameter payload fairing. The ability to fit into a payload fairing allows the cargo version to launch on any sufficiently capable vehicle, such as Ariane 5, Atlas V, and Vulcan Centaur, just to name a few. An expendable cargo module will launch attached to the back of the spacecraft named Shooting Star, expanding the cargo uplift capacity and supporting the disposal of up to 3,250 kg (7,170 lb) of trash. Total uplift is planned for 5,000 kg (11,000 lb) pressurized and 500 kg (1,100 lb) unpressurized, with a downlift of 1,750 kg (3,860 lb) contained within the spaceplane.
Back in late 2019, it was announced that almost all Dream Chaser CRS-2 flights will be carried into orbit by ULA’s Vulcan launch vehicle, with the first Dream Chaser flight being the second Vulcan flight in late 2021. However, on February 9, 2022, Ken Shields, Sierra Space’s Director of Commercial Market Development announced that the first flight would be pushed to January 2023. By now we are hoping to see this launch by the end of 2023. Currently, there are two known Dream Chaser test articles being worked on. The first and the one with the most progress is Tenacity which we have seen a lot of recently. The second however has been kept out of sight for the most part from Sierra Space. A few months ago they provided a tweet showcasing the new test article which was just a frame at that point. Over time we will likely start to receive more information on both of these spacecraft.
Conclusion
Sierra Space is trying to change how we access space. Dream Chaser is a unique spaceplane that is set to launch for the first time not long from now. For years now a lot of the focus on this spacecraft has been on its heat shield and TPS tiles. The company is confident that they have made significant improvements to its design and capability. We will have to wait and see how it progresses and the impact it has on the space industry.