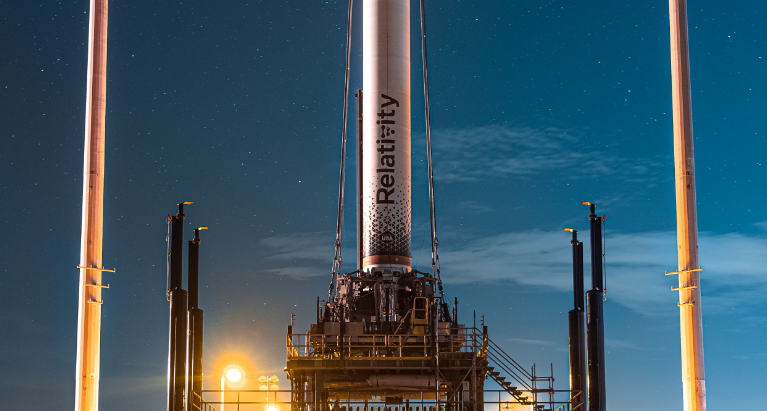
Relativity Finishes More Tests In Preparation For The First Terran 1 Flight
Relativity Space has been working towards the first flight of Terran 1 for years now. This launch is a big deal not only because the launch vehicle itself will be put to the test but so will the company’s 3D printing manufacturing process and more. Whether it goes well or not, it’s expected to provide a lot of invaluable information as the company moves on to the next steps.
The last couple of weeks have been especially busy with multiple static fires, general tests, and final preparations for launch. Only days ago we watched the mounted stage complete a spin start test at LC-16. This launch pad has gone through a lot of work and will also be an important test article for the maiden launch of Terran 1.
Looking at different companies within the industry, no matter the size the first launch was by no means easy. More often than not the first launch of a rocket ends with a big explosion not long after lift off. However, Relativity is confident and hoping for success. Here I will go more in-depth into the recent progress the company has made, the launch vehicle and launch site responsible, and more.
Recent Updates
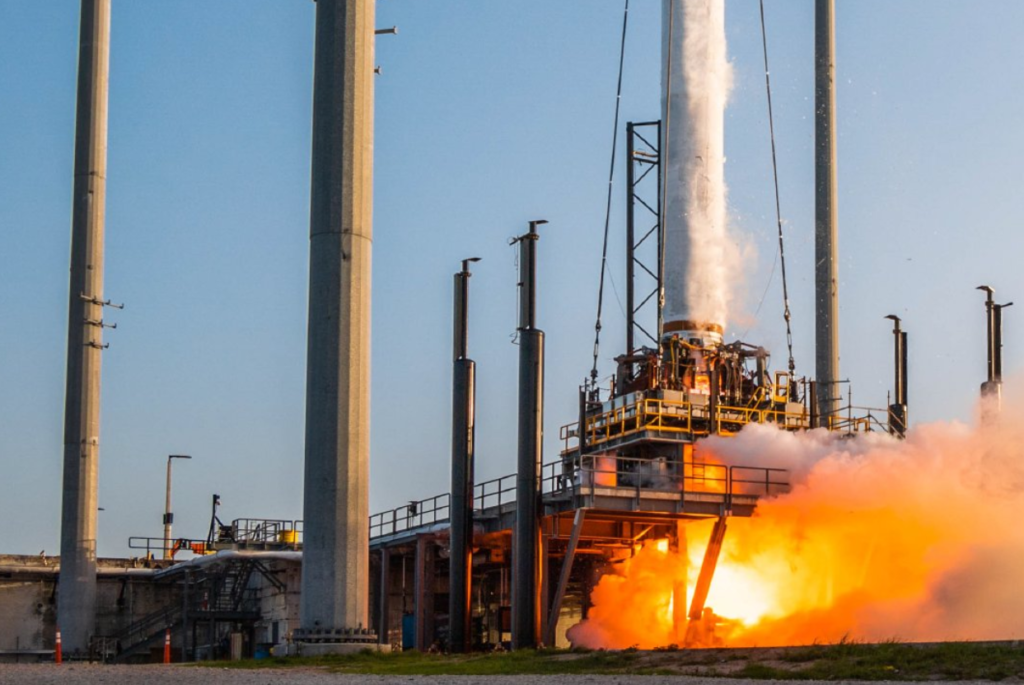
With the first launch of Terran 1 closer than ever, Relativity Space has been very busy. Thankfully, over the past few weeks, the company along with CEO Tim Ellis have provided some updates on what they are working on and have accomplished. One of the biggest updates came on July 28th when Relativity tweeted saying, “Peek inside our first Stage 1 hot fire, bringing all nine Aeon 1 engines up to full power. The test marked another first not only for us here at Relativity, but also for aerospace manufacturing as an industry, with all engines and Stage 1 being 3D printed.” This included a ten second video of the hot fire showing a close up of the exhaust. Relativity Space’s engines, Aeon 1, Aeon R and Aeon Vac, are 3D-printed, intended to enhance mission reliability by reducing part count in engine combustion chambers, igniters, turbopumps, reaction control thrusters, and vehicle pressurization systems.
All Aeon engines use propellants of the future, such as liquid oxygen plus liquid natural gas, which are not only one of the best for rocket propulsion, but also the easiest to eventually make on Mars. The thrust chamber is regeneratively cooled with liquid natural gas, which is then injected into the main combustion chamber and burned with liquid oxygen to produce the required thrust. To date, Aeon has completed over 500 test fires. Each of Terran 1’s 10 engines is based on a common design, enabling simplified and repeatable manufacturing and acceptance testing.
In the short video, we are watching the first stage of Terran 1. The first stage assembly consists of three main components: the thrust structure, the Stage 1 tank, and the interstage. The tanks share a common dome and airframe that is integrally printed as monolithic sections, where a horizontal welding process integrates Stage 1 segments together to achieve the final stage structure. A transfer tube carries LOX through the center of the LNG tank to the engines. Nine Aeon-1 engines power the first stage with up to 23,000 lbf thrust per engine at sea level, for a total thrust of up to 207,000 lbf at liftoff. Terran 1 autogeneously pressurizes the tanks with gaseous natural gas and gaseous oxygen via heat exchangers integrated into the Aeon-1 engines, eliminating the need for a separate pressurization system and avoiding the use of helium on the vehicle entirely. Electromechanical actuators gimbal the outer 8 engines, providing thrust vector control. The stage separation system is located at the forward end of the interstage and interfaces with the second stage.
Next, on the 4th of August, Relativity tweeted again mentioning, “#TBT at LC-16, Cape Canaveral, FL: Between 1959-1988, LC-16 supported a total of 141 launches, and this year, it will host the first orbital launch of #Terran1 – marking the site’s first launch in 34 years. Historic then, historic now.” This included some images of the initial launch operations at this site long ago and new images of Relativity preparing for the launch of Terran 1. Specifically, back in 2019, Relativity announced that it had been granted a Right of Entry for its own rocket launch facilities at Launch Complex 16 (LC-16) at Cape Canaveral Air Force Station in Florida by The 45th Space Wing of the United States Air Force. The Right of Entry signified the U.S. Air Force’s formal acceptance of Relativity to build and conduct launch operations from Cape Canaveral Air Force Station. This is the first and only direct agreement the U.S. Air Force has completed with a venture-backed orbital launch company at LC-16, and includes on-site vehicle integration and payload processing, with the opportunity to extend to an exclusive 20-year term. Relativity joined SpaceX, ULA, and Blue Origin as only the 4th company with a major operational orbital launch site at Cape Canaveral.
Finally, only two days ago on August 9th, Relativity Space tweeted again highlighting, “POV from LC-16 Blockhouse on a recent spin-start test operation.” This tweet included a GIF of the stage 1 test from a camera in the distance which provided a great view of the engine fire.
Terran 1 & 3D Printing
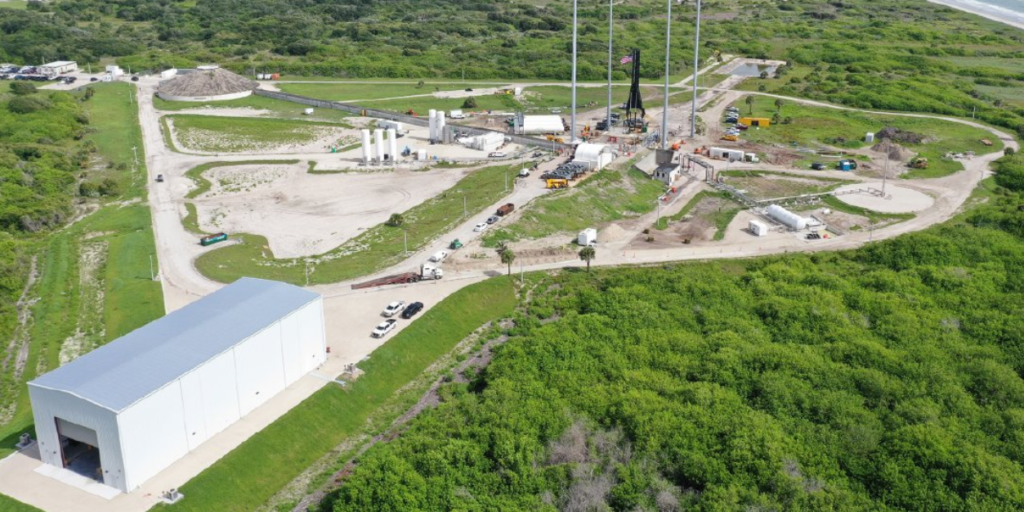
Now that we know more about some of the recent updates from Relativity, we can take a closer look at the upcoming mission itself, and why it’s such a big deal to the company and space industry. Not long ago Relativity scheduled its first launch of Terran 1, called “GLHF” (Good Luck, Have Fun), from Launch Complex 16 (LC-16) in Cape Canaveral in summer 2022. This launch of Terran 1 is the first orbital attempt by Relativity and will not include a customer payload. As a two-stage, 110ft. tall, 7.5 ft. wide, expendable rocket, Terran 1 is the largest 3D printed object to exist and to attempt orbital flight. Working towards its goal of being 95% 3D printed, Relativity’s first Terran 1 vehicle is 85% 3D printed by mass. Terran 1 has nine Aeon engines on its first stage, and one Aeon Vac on its second stage. As one of the few LOX/LNG fueled rockets in the industry, Terran 1 is racing to be the first LOX/LNG rocket to fly.
As partially mentioned prior, the mission is a big deal not only because it will test Terran 1 as a launch vehicle, but also the design and manufacturing process Relativity is trying to innovate. Relativity’s proprietary Factory of the Future centers on Stargate, the world’s largest metal 3D printers, that create Terran 1, and the first fully reusable, entirely 3D printed rocket, Terran R, from raw material to flight in 60 days. Relativity is confident its Stargate printers’ patented technology enables an entirely new value chain and innovative structural designs that make Terran 1 and Terran R possible. By developing its Factory of the Future and rockets together, Relativity accelerates its ability to improve design, production, quality, and speed. In addition, the company often highlights that for 60 years, aerospace manufacturing has relied on large factories, fixed tooling, complex supply chains, and extensive manual labor to build costly rockets comprised of 100,000 plus parts in 2 years or longer. These printers use materials intended to work for both rockets and the printing process. Some features include high strength alloys specially designed for Stargate printers. Physical properties designed to meet mission-critical structural requirements. In-house material characterization lab for quickly iterating on new alloy development. Relativity also developed multiple proprietary alloys custom designed for 3D printing to meet mission-critical performance.
To accelerate innovation in the industry, Relativity built its Factory of the Future, the first aerospace platform to automate rocket manufacturing, vertically integrating intelligent robotics, software, and data-driven 3D printing technology. Incorporating Stargate, the world’s largest metal 3D printer with AI-driven controls, Relativity’s Factory of the Future continuously optimizes production, resulting in greatly compounded quality and time improvements, lower costs, and product designs previously not possible. Relativity is an application-layer 3D printing company that is starting with rockets, and will extend its Factory of the Future to all of aerospace. Not long ago the company acquired a new facility and are starting to work on it. With 120,000 sq. ft., Relativity’s brand new headquarters and expanded factory will host both the company’s business operations and an unprecedented manufacturing facility, integrating machine learning, software, and robotics with metal additive manufacturing technology to produce Terran 1.
Conclusion
Relativity Space is getting very close to the first launch of Terran 1. For years now the company has been working to recreate how rockets are manufactured. Not long from now, this process will be put to the test. While most first launches aren’t fully successful, it will no doubt provide the company with a lot of invaluable information. We will have to wait and see how it progresses and the impact it has on the space industry.