A company called Sierra Space has been working on a modern spaceplane known as Dream Chaser. With the first launch scheduled to happen in 2025, we are not far away as they complete final testing and assembly on the first test article, named Tenacity.
One of the main focuses of this reusable vehicle has been its heat shield, which will determine not only its ability to reenter the atmosphere in one piece but also launch consistently with limited refurbishment between flights. Interestingly, the company is already working on a new heat shield for the second test article.
New Heat Shield

As of right now, the final tiles are being installed on Dream Chaser Tenacity for a launch early next year. Since the start of the program, the tiles have been a major focus and for good reason, considering their impact on core parts of the mission. However, it seems that the second Dream Chaser launch will feature a new type of heat shield.
Earlier today Sierra Space tweeted saying, “Sierra Space and the Oak Ridge National Laboratory (@ORNL) are collaborating on a groundbreaking new technology that will enable exterior spacecraft tiles to withstand the high temperatures of re-entering Earth’s atmosphere over multiple missions.”
Included was a statement highlighting the new protection system. They were quoted saying, “The breakthrough development enables exterior spacecraft tiles that can withstand the high temperatures of re-entering Earth’s atmosphere over multiple, frequent missions. This new Thermal Protection System (TPS) was created to meet the needs of a commercial space industry that is moving at a faster pace than previous generations of spaceflight, and now requires more missions over shorter periods of time.
They go on to highlight that “The team at Sierra Space and Oak Ridge National Laboratory leveraged more than three decades of experience with NASA’s Space Shuttle program to design the new system.”
In the past, exterior tiles used on the Space Shuttle were only needed for an average of five missions per year. The Shuttle also had a number of complications related to its heat shield. Since the start of work on Dream Chaser, they have expressed a number of changes that differentiate the new spaceplane from the Shuttle.
For example, Dream Chaser features around 2,000 tiles in total compared to the more than 20,000 on the Shuttle. Also, Sierra Space is quoted saying, “SNC engineers have been able to update the TPS tiles from what was used during NASA’s shuttle program with more innovation, better technology, and utilizing lessons learned. They use more modern manufacturing techniques to increase strength and reduce cost. Another difference between the tiles is Dream Chaser tiles are about 10 inches by 10 inches, while those on the shuttle were six inches by six inches. Dream Chaser tiles are meant to be stronger and lighter weight than those used during the shuttle program and meet all Micro-Meteroid Orbital Debris (MMOD) requirements to ensure safe entry, descent, and runway landings for crewed or cargo missions.
Keep in mind these comments are talking about the current heat shield system used on Tenacity, not the upgraded variant that the company is working on right now. In a quote from today’s statement, the Sierra Space CEO said, “Today marks a new era of spaceflight safety technology, and it’s going to enable travel to Low Earth Orbit that will eventually rival the frequency of commercial air travel. Our patent-pending Thermal Protection System is like nothing ever before created and essential to a near future where space travel becomes routine. Reusability of space vehicles is a key factor in expanding the commercial space industry and to do that we need new technology to keep spacecraft and crew safe” he said.
In terms of the progress on these new tiles, Sierra Space and Oak Ridge National Laboratory have completed the first development phase of the TPS. The next phase involves more testing, which includes subjecting the tiles to testing at NASA’s Arc Jet plasma facility, which simulates the conditions of re-entry to Earth from space with heated gas flow. The second phase also explores using advanced manufacturing techniques to lower the costs of TPS production. They then mentioned, “The new TPS system is planned to be used on Sierra Space’s Dream Chaser moving forward, including the second Dream Chaser, called Reverence™, which is currently in production at the company’s Dream Factory in Colorado” they said.
For reference, over the past few years we haven’t received a lot of information on the second Dream Chaser besides a couple images of it in early production. In regard to the heat shield change, this is quite a big deal and suggests the company’s confidence in the system. It also could highlight that the current heat shield installed on Tenacity may not be a long term solution but good enough for initial uncrewed cargo missions.
Heat Shield Design
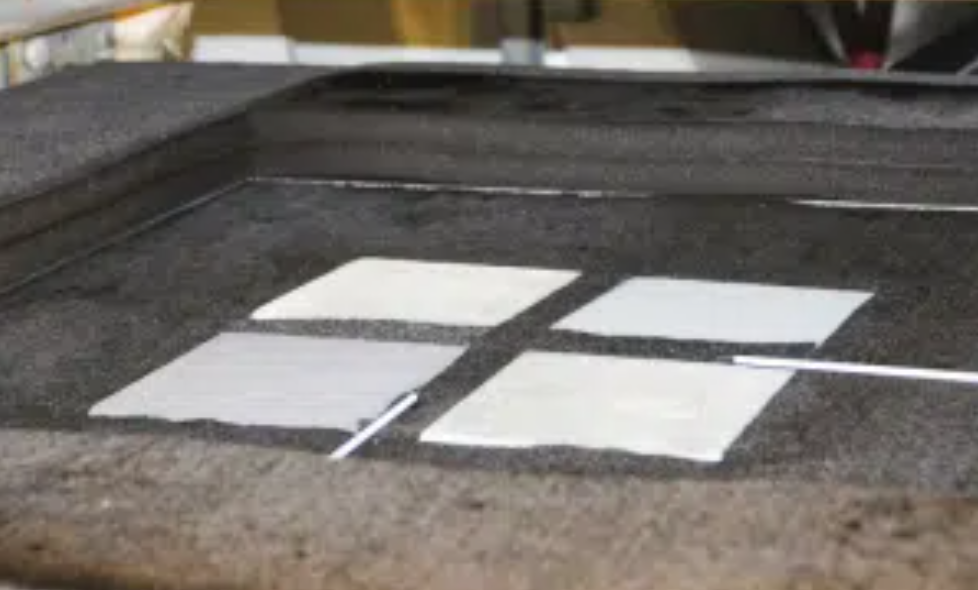
As far as the actual design, the new tiles are made of a proprietary composite material that’s as strong as carbon fiber but with the added high-temperature stability of ceramic materials. The composite tiles have low-density thermal protection properties that are vital for insulative protection and stable flight dynamics. Atmospheric re-entry exposes spacecraft to speeds of more than Mach 17 (About 13,000 mph or 21,000 kph) with temperatures reaching higher than 3,100 degrees Fahrenheit (1,704 degrees Celsius).
Its important to point out that the heat shield has always been a major focus of the company. Back in 2015 for example, Sierra Nevada Corporation (the parent company of Sierra Space) successfully completed several significant Thermal Protection System (TPS) material development tests for its Dream Chaser spacecraft. These initial TPS tests were completed at NASA’s Ames Research Center and Johnson Space Center under reimbursable Space Act Agreements (SAA).
At the time, the corporate vice president of SNC’s Space Systems commented, “Safety of crew and cargo is most important to our team as we continue to mature the spacecraft design. For several years, we have worked collaboratively with Johnson and Ames, leveraging their existing infrastructure, materials, and expertise to mature and customize the TPS for our unique spacecraft. Our TPS is lighter, stronger, and more efficient than previous generations. We have met or exceeded all mission requirements. We are now prepared to enter the Critical Design Review phase for this system” they said.
As far as the tests themselves, over 100 arc jet cycles and radiant heat tests were completed at Johnson’s Radiant Heat Test Facility (RHTF) and Ames’ Aerodynamic Heating Facility (AHF). RHTF provided results supporting thermal characterization of the developmental TPS materials. The test data was then used for thermal modeling, analysis, and TPS sizing. The Ames AHF arc jet tests were performed as a second phase in the development testing to gauge the material performance in environments simulating Dream Chaser flight conditions. Valuable arc jet test results supported SNC’s certification of the manufacturing capability of a high-temperature material called Toughened Uni-Piece Fibrous Reinforced Oxidation-Resistant Composite TUFROC. At the time they noted that TUFROC would be used on the high-temperature nose and wing leading edges of the Dream Chaser spacecraft.
The shift to somewhat of a new tile build suggests they weren’t fully satisfied with what the original tiles had to offer. The goal of Dream Chaser is to launch and reenter the atmosphere when the mission is complete followed by a runway landing. Sierra Space is aiming for a minimum of 15 flights per vehicle. The heat shield will likely be the determining factor in whether or not they can continue to launch different test articles and finished vehicles.
On the Space Shuttle, the Thermal Protection System was designed to provide a smooth, aerodynamic surface while protecting the underlying metal structure from excessive temperature. Several types of TPS materials were used on the Orbiter. These materials included tiles, and advanced flexible reusable surface insulation.
Specifically, NASA used two categories of Thermal Protection System tiles on the Orbiter—low- and high-temperature reusable surface insulation. Surface coating constituted the primary difference between these two categories. High-temperature reusable surface insulation tiles used a black borosilicate glass coating that had an emittance value greater than 0.8 and covered areas of the vehicle in which temperatures reached up to 1,260°C (2,300°F). Low-temperature reusable surface insulation tiles contained a white coating with the proper optical properties needed to maintain the appropriate on-orbit temperatures for vehicle thermal control purposes. The low-temperature reusable surface insulation tiles covered areas of the vehicle in which temperatures reached up to 649°C (1,200°F).
Unfortunately, tiles often fell off and caused much of the delay in the launch of STS-1, the first shuttle mission, which was originally scheduled for 1979 but did not occur until April 1981. Each tile used cement that required 16 hours to cure. After the tile was affixed to the cement, a jack held it in place for another 16 hours. This combined with the fact that there were tens of thousands of tiles in total and it caused a few issues over the lifetime of the program.
It seems like Sierra Space is aware of this and trying to upgrade and alter the technology to support a rapid and consistent turnaround after reentry. As partially mentioned before each Dream Chaser still has thousands of tiles which means the build and installation will need to be significantly improved.
Conclusion
Just earlier today Sierra Space announced work on a new and upgraded heat shield that they plan to use on the next Dream Chaser. With plans to reuse each vehicle at least 15 times, they will need a thermal protection system that not only is strong enough for reentry, but can do it again and again with minimal refurbishment in between.