Rocket Lab is still targeting a maiden flight of the Neutron launch vehicle as soon as 2025. As we approach the end of 2024, progress is ramping up both on Archimedes engine development as well as composite test structures. Even the launch pad has been busy as they prepare to support a new partially reusable medium-lift rocket.
While the company’s current time estimates are ambitious, they’re not completely out of the question with more and more work being done each day.
Recent Progress
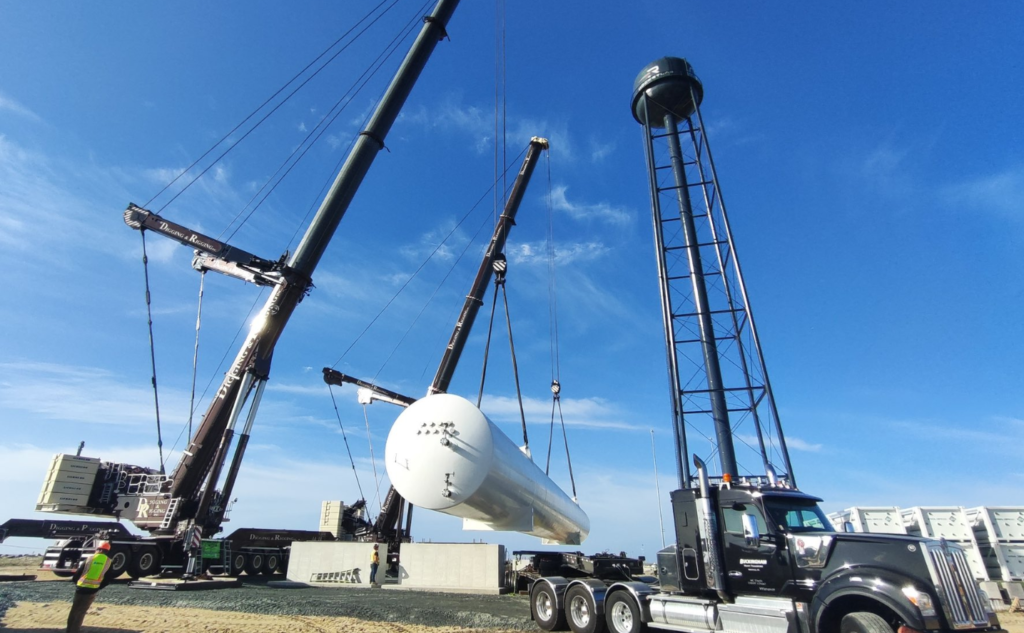
One of the main focuses surrounding Neutron development has been its new Archimedes engine. In total, each Neutron will feature 10, 9 on the first stage and one vacuum-optimized engine on the second stage. The Archimedes engine is an oxidizer-rich staged combustion cycle engine that will propel the rocket, designed to carry up to 13,000 kilograms of payload to space.
Back in August of this year, Rocket Lab completed the first hot fire of this new engine. Since then, they have produced a few more engines and completed a number of additional hot fires. Only yesterday, the company CEO Peter Beck tweeted saying, “Keeping them shipping.” With an image of a brand-new engine being shipped off.
This is believed to be the fourth Archimedes engine that’s completed production. In a different quote from Beck only a few weeks ago he said, “A hot fire a day keeps the critics away. Of course we are rotating engines in and out as we put them through their paces, find limits and make tweaks. SN2 is on the stand now and SN1 and SN3 will be going back out to the site as soon as next week as we play with things. It’s all part of a normal engine development and qualification program” he said.
This helps put in perspective the number of capable engines the company has and the rotation and test campaign they are currently putting them through.
In addition, on September 28th Rocket Lab tweeted saying, “Things have been heating up at Stennis. The Archimedes engine development and qualification campaign continues to progress well with lots of hot fires taking the engine through various operating conditions and tweaks.” This included more than two minutes of hot fire footage. It’s clear based on all these comments and examples that Rocket Lab is putting a lot of effort and focus on the development of Archimedes.
However, when you look at some of the upcoming milestones and tests, it’s clear the company will need quite a few of these engines. Rocket Lab highlights that each engine is capable of producing up to 165,000 (733 kilonewtons) pounds of thrust, and that Archimedes operates at lower stress levels than other rocket engines to enable rapid and reliable reusability. The combined thrust of nine Archimedes engines for Neutron’s first stage is designed to reach 1,450,000 lbf total. In terms of fuel, Archimedes uses a cryogenic propellant mix of liquid oxygen and LNG to enable higher reusability and performance.
The goal for the company is to both improve the design and speed up the general engine manufacturing over time. In support of this, many of its critical components are 3D printed including Archimedes’ turbo pump housings, pre-burner and main chamber components, valve housings, and engine structural components.
Beyond the engines, we’re also seeing progress on the new launch pad and rocket structures themselves. A few weeks ago Rocket Lab tweeted saying, “Another day, another large carbon composite structure complete for Neutron. From here this stage 1 LOx tank common dome will be fitted with internal propellant management devices ahead of assembly into the flight stage 1 tank.”
This progress matches up with the company’s official timeline and progress. Specifically, looking at their website, you can see that there are currently three major developments marked as in progress. This first includes testing of critical flight mechanisms including separation systems, fairing actuation, control surfaces and actuators. The next, which has to do with the tweet is the Stage 1 build, or completing a full-scale carbon composite stage 1 tank built using advanced manufacturing methods. In the future Rocket Lab is hoping to hot fire this stage, then complete a full wet dress rehearsal, and finally launch the hardware. In other words, they are actively working on flight hardware right now.
The third milestone marked as in progress is the completion of Launch Complex 3. As recently as last month, Rocket Lab installed a new propellant tank. Peter Beck was quoted saying, “Nothing like 680,000L of LOX for breakfast. LC3 launch pad taking shape nicely.
Only a few months earlier we saw even more progress. That included the installation of a massive water tower and work on concrete. Back then, propellant and gas storage foundations were undergoing a final concrete pour.
Neutron’s Development
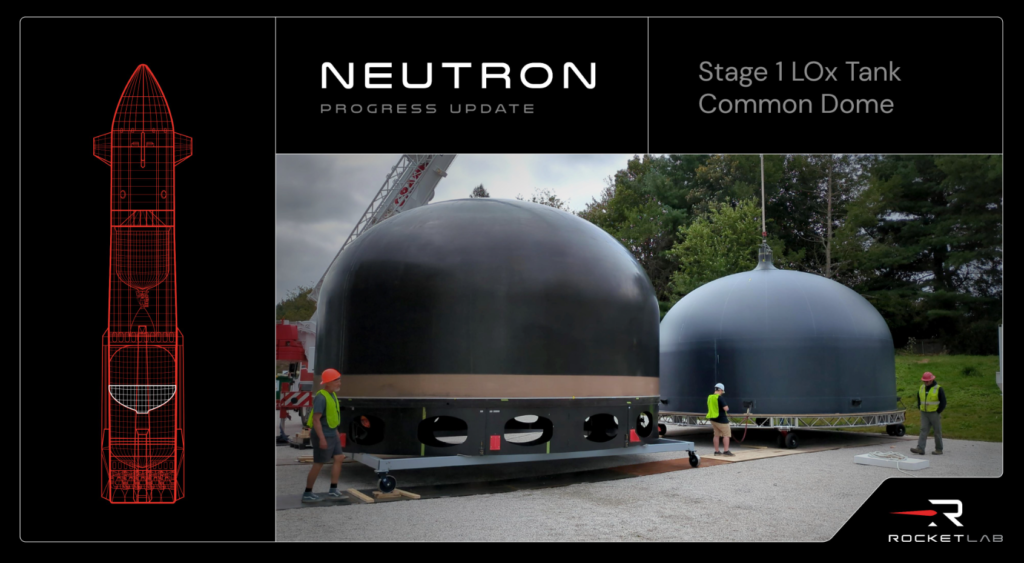
While all of this progress is great, there still is a lot of work to do. Looking back at Rocket Lab’s timeline, there are quite a few items that they were hoping to complete before 2025 that will end up being pushed back. For example, with just over two months left before the end of the year, they also want to check off the first Stage 2 static fire, the first stage static fire, complete vehicle integration, and then a full wet dress rehearsal.
One of the most recent official time estimates for the first launch came in May when the company confirmed that they were still targeting a maiden flight in mid-2025. A schedule that would make Neutron the fastest a commercially developed medium-class launch vehicle has been brought to market.
Focusing back on their progress, recently they began installation of the largest automated fiber placement (AFP) machine of its kind into the Company’s Neutron rocket production line. The AFP machine will enable Rocket Lab to automate the production of the largest carbon composite rocket structures in history.
In a statement they were quoted saying, The custom-built 99 ton (90 tonne), 39 ft tall (12-meter) robotic machine, American-made by Electroimpact in Washington, has just completed final acceptance testing with the manufacturer and installation has begun at Rocket Lab’s Space Structures Complex in Middle River, Maryland. The new machine will automate the production of all large composite structures of the Neutron launch vehicle including the panels that make up the 91 ft (28 meter) length interstage and fairing, 22.9 ft (7 meter) diameter first stage, and the 16.4 ft (5 meter) diameter second stage tank.”
“The autonomous machine can move up to 98 ft (30 meters) in length and lay down continuous carbon fiber composite at a rate of 328 ft (100 meters) per minute. The AFP machine also has a fully automated real-time inspection system that hunts for miniscule defects throughout the laminated carbon composite and alerts the machine operator of any issues before the machine begins laying down the next layer, providing additional assurance that these critical structures of the launch vehicle meet Rocket Lab’s high-quality standards required for reusable Neutron launches” they said.
Peter Beck was quoted saying, “As we build the world’s largest carbon composite rocket, it makes sense that we require a world-first carbon composite fiber placement machine. We’re combining our proprietary flight-proven carbon composite technology, additive manufacturing, and autonomous robotics to design and build large-scale aerospace components at a pace that will support not only Neutron’s launch cadence, but support Electron and carbon composites structures for our spacecraft customers too. We worked closely with our excellent partners at Electroimpact to create this robot and we’re thrilled with the results. It’s an innovative machine producing a next-generation rocket from one of the birthplaces of the aerospace industry in Baltimore, and we can’t wait to see its first carbon composite printed panels come off the production line soon” he said.
It’s systems like these that could help the company reach some of its ambitious timelines, assuming things work as intended. As Neutron’s carbon composite structures move into full-scale production, Rocket Lab believes this autonomous machine will introduce significant time-savings of 150,000+ manufacturing hours in the production process.
When talking about Archimedes and Neutron’s timeline as a whole Peter Beck said, “What we’ve taken to the test stand is very close to a flight-like engine, and with all of our production infrastructure stood up alongside the engine’s development, we’re in a prime position to be able to make quick iterations to Archimedes for a rapid development and qualification campaign. We took the time to not only bring a mature design to the stand that has been thoroughly tested at the component level, but to also stand up the experienced team, manufacturing line, and test facilities required to support the long-term production of Archimedes.”
“This approach has ultimately pushed the first flight to mid-2025 at the earliest, but it’s an approach we believe will deliver the frequent flight rates the market needs quickly after flight one. Designing a brand-new rocket engine to meet the market demand for frequent and reliable launch is complex feat, but it’s something we’ve successfully done before, having launched more than 470 Rutherford engines to space. We look forward to repeating this success with Archimedes” he said.
This suggests that they expect to pick up the pace now that the initial Archimedes engines have been delivered. If they can continue to produce them at a rapid pace and get good results on the test stand, they won’t be far away from actual flight hardware static fires in the future.
Conclusion
Rocket Lab is continuing to make a push toward the maiden flight of Neutron. In the past few months, we’ve seen more engine production, hot fires, launchpad development, and actual flight hardware being constructed. All of which as they target a launch by the middle of next year.