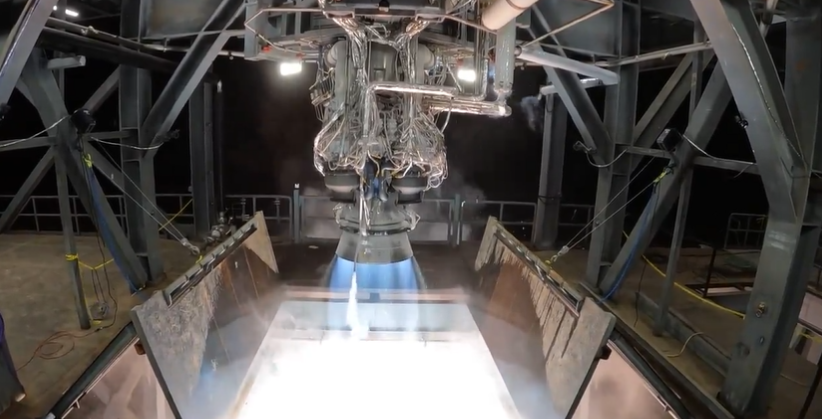
Relativity Just Fired Its New 3-D Printed Aeon R Engine
Ever since the launch of Terran 1, Relativity Space has shifted its complete focus to Terran R, a much larger reusable 3D-printed rocket. For months now we have seen work on new manufacturing facilities, test sites, and actual rocket hardware. This includes brand-new testing and the first full static fire of the vehicle’s Aeon R engine.
Just yesterday the company released footage of the engine firing and provided updates on its progress. In the future, 13 of these engines will power Terran R and are necessary when determining the efficiency, reliability, and reuse opportunities of this next-generation rocket. Something Relativity is taking very seriously and needs to get right in order to have success in the future. Here I will go more in-depth into the new static fire, how Aeon R got to this stage, other Terran R developments, and more.
New Static Fire

Starting earlier this month we got a hint that a big test was about to happen when the company tweeted saying, “First look: Aeon R on the test stand.” This included an image of the engine rigged up and practically ready to fire. Only a few weeks later on the 14th the company announced that they had completed the static fire and the results were promising. In total, it was a 10-second fire. However, they pointed out that the test validated component harmony during start up, at a target power of (70%), and shutdown. They also were quoted saying, “Strong start to test campaign. Initial hardware inspections look healthy. Longer duration. More power. More blue fire.”
What makes this test especially interesting is the fact that this engine is 3D printed. Relativity believes that by using 3D printing techniques, they are able to design more function into the engines, with less material, for less cost. They also have some history building the Aeon 1 engine for Terran 1, which they have learned a lot from. To put it in perspective, a single Aeon R engine has 25% more thrust than all nine Aeon 1 engines combined. This significant size and power increase means teams at Relativity are facing a lot of new challenges. This being said, the progress on the new engine seems to be going very smoothly and has been for quite a while now.
Since mid-2022, Relativity has been underway testing all Aeon R combustion devices at NASA Stennis Space Center – including the main Thrust Chamber Assembly (TCA), gas generator (GG), and gas-gas ignition system – at full scale and 100% power with high combustion efficiency. All engine active valves are developed in-house, with all valves produced, successfully actuated, and in development testing. In February 2023, the company completed its first full build of an Aeon R engine. This combined with other milestones along the way highlights that the company has been consistently building, testing, and improving this system.
The Aeon R produces a sea level thrust of 258,000 lbf and a combined vehicle liftoff thrust of 3,354,000 lbf. Looking at images of it next to Aeon 1 and humans helps put its size and power in perspective. At its core, Terran R’s 3D printed Aeon R engines are designed to use liquid oxygen and liquid methane propellants, be highly reusable, and feature a uniquely high-pressure gas generator cycle driving two turbopumps. The company is quoted saying, “Designed and manufactured in-house by Relativity, Aeon R engines are produced with significant advancements in additive manufacturing technology, building on the development of the company’s prior engine, Aeon 1. These new 3D printing capabilities enable the scale required for the higher thrust-class Aeon R engine, continuing to drive part count reductions by designing and printing singular ‘nodes of simplicity’, streamlining many engine elements into unified prints. This innovative design approach supports lowered costs, lowered engine complexity, greater robustness, rapid iteration, and the speed and scale of production required to serve customers” they said.
The company is obviously very confident in both the engine’s design and the manufacturing techniques being used. At the same time, they are making physical progress quite quickly which helps their case. Focusing back on the static fire, there still is a lot of work necessary to perfect this process and prepare for full-duration fires. With the booster expected to be reused 10s of times, the engines need to work again and again and require little to no refurbishment between missions. An extra hurdle that Relativity will continue to work on in the coming months.
Terran R Developments
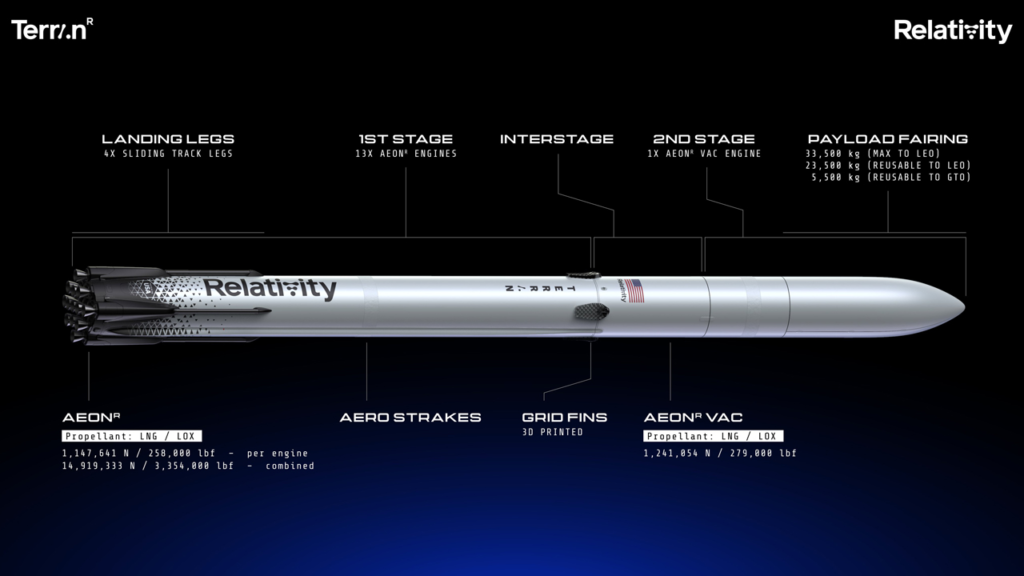
Standing at 270 feet (82m) tall with an 18-foot (5.5m) diameter and a 5-meter payload fairing, Terran R is going to be a massive rocket. This large jump from the much smaller expendable Terran 1 to a reusable giant like Terran R is extremely ambitious. It’s also why Relativity has been all hands on deck building new 3D printers, facilities, test stands, etc, all to get ready for the future of this rocket.
For example, the company recently got access to the A-2 test stand and has been working to revamp and prepare it. This is going to be a large overhaul and is meant for future Terran R testing. Over on the launch site, specifically, Space Launch Complex-16, in Cape Canaveral, Florida, demo work is underway for land clearing of TerranR’s new propellant farm and future launch pad. Even in Stennis, the company is in the process of building and constructing massive test stands and propellant farms all for this next-generation vehicle.
As of right now, Relativity believes they can launch Terran R for the first time in 2026. This has moved back a decent bit from past estimates but is still not far away especially considering the work that still needs to be done.
Taking a closer look at the rocket, they describe Terran R as a customer-centric next-generation launch vehicle designed to meet the needs of commercial companies and government entities sending payloads into LEO, MEO, GEO, and beyond. The vehicle’s architecture choices are meant to enable accelerated development and the ability to deliver a rapidly scaling launch cadence for customers. As far as reusability, Terran R will prioritize first-stage reuse, with the capability of launching 23,500kg to Low Earth Orbit (LEO) or 5,500kg to a Geosynchronous Transfer Orbit (GTO), both with downrange landing, or up to a maximum payload of 33,500kg to LEO in expendable configuration.
Most uniquely, Terran R is a 3D printed rocket, with initial versions using aluminum alloy tank straight-section barrels in a hybrid manufacturing approach, which the company says allows them to meet the rapid launch and ramp rate timelines necessary to serve overwhelming market demand. By now, Relativity has a total of nine signed customers for Terran R, including multiple launches, totaling more than $1.8 billion in backlog. This funding and support have helped the company build and expand at such a rapid pace.
While they have experience with Terran 1, each Terran R requires approximately 6 times more 3D printing by mass than that smaller vehicle. They point out that 3D printing technology for Terran R is strategically used to reduce vehicle complexity and improve manufacturability, with continued company focus on redefining what is possible with large-scale additive manufacturing after successfully proving the viability of 3D printed rockets with Terran 1. Initially, Terran R will use the same proprietary printed aluminum alloy as flown on Terran 1 with a focus on supply chain scaling. However, a third-generation aluminum alloy, designed for improved performance of an orbital vehicle mission life beyond 20 reusable flights, is in active development, which they say is accelerated by the aid of artificial intelligence-based alloy discovery tools.
The plan for first-stage reuse will also be somewhat similar to other rockets within the industry. As partially mentioned prior, Terran R’s first stage will be outfitted with 13 3D-printed gas generator cycle Aeon R LOx/Methane rocket engines, while its second stage houses a single LOx/Methane Aeon Vac engine. The specific engine composition on the first stage is comprised of four outer fixed engines aligned underneath four landing legs, and nine center gimbaled engines, providing enhanced reliability on vehicle ascent with engine-out capability. On both Terran R stages, the LOx propellant tanks are forward of the methane tanks, separated by a printed common dome. Subcooled cryogenic propellants are used on all parts of the vehicle except for the first stage liquid oxygen system, where subcooling is not necessary to meet performance goals. Both stages use a cryogenic helium pressurization system to enable better press authority when engines are not turned on by reducing ullage collapse. The vehicle also features an in-house developed pneumatic pusher stage separation system.
In addition to the landing legs and gimballed engines, Terran R features two near body-length aero strakes, and four printed actuating grid fins. These features among others are meant to allow the first stage architecture to have a high angle of attack reentry which reduces propellant required for reentry burns, aerodynamic design for better reentry stability and improved control authority, and a passively actuated landing leg deployment system which they describe as elegantly simple, lightweight, and highly operable for rapid reuse. An 18-foot vehicle diameter also aids vehicle stability with lower requirements on landing legs. All of which we could see in use in just a few years from now.
Conclusion
Relativity Space just completed its first static fire of Terran R’s new Aeon R engine. While short, its a great first step and an important milestone in the project’s overall timeline. We will have to wait and see how it progresses and the impact it has on the space industry.