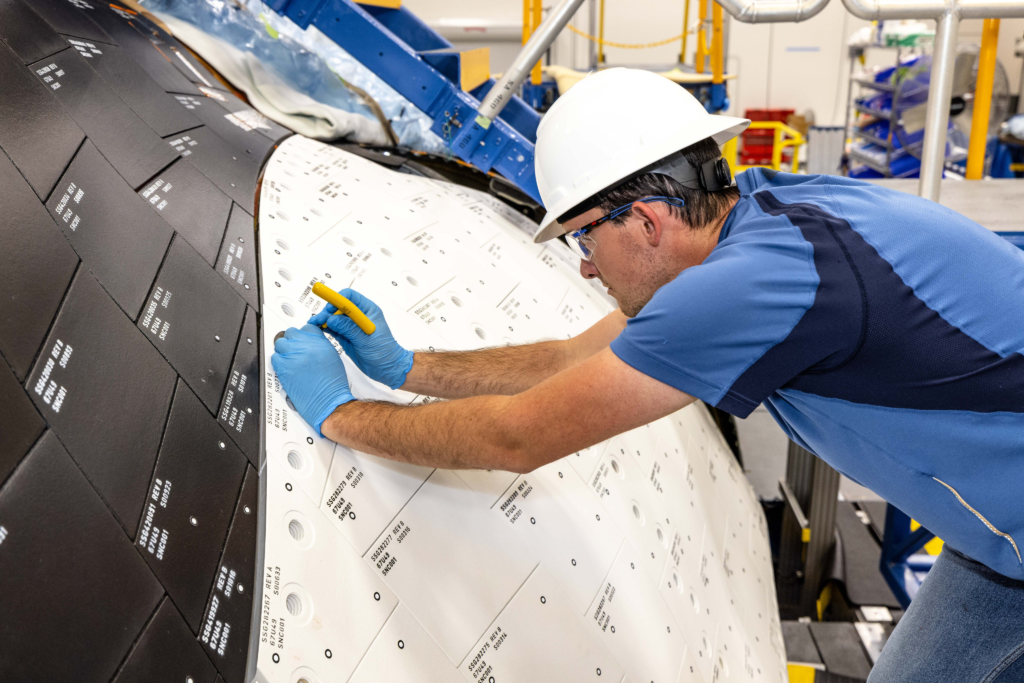
A Closer Look At The Modern Spaceplane’s Heat Shield
At this point, Dream Chaser Tenacity is set to launch for the first time in only a few months. For the last few years, this spaceplane has been undergoing testing and general manufacturing. One area in particular that has been a main focus for the company has been its intricate heat shield. Here thousands of unique tiles are positioned across the spaceplane to create a barrier from the intense forces and heat during reentry.
Looking back in time, the Space Shuttle experienced a host of issues with its heat shield which consisted of tens of thousands of tiles. These problems increased the time necessary between each mission, and jeopardized astronaut safety.
Sierra Space however is confident the tiles they are using today are a significant improvement from the technology we saw in the past. Here I will go more in-depth into the modern spaceplane heat shield, Tenacity’s first launch, improvements from past designs, and more.
Dream Chaser’s Heat Shield
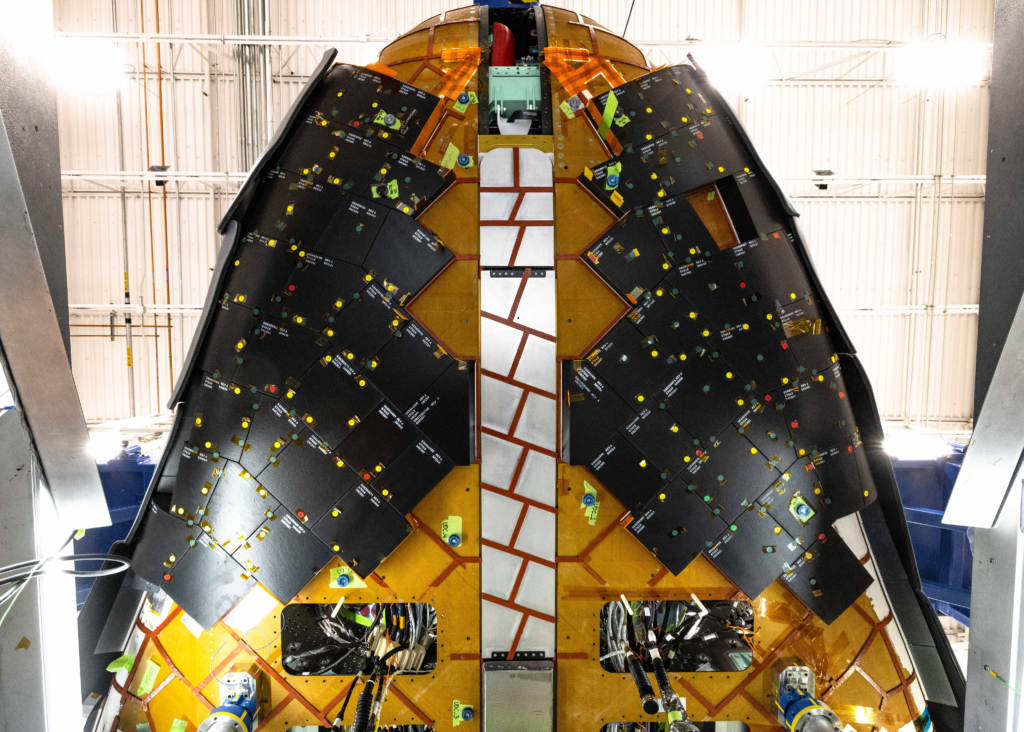
While Dream Chaser shares a few similarities to the Space Shuttle, size is not one of them. The vehicle is much smaller and as a result, has much less surface area. In total, Dream Chaser uses approximately 2,000 Thermal Protection System (TPS) tiles across its body. These wrap all along the sides of the vehicle, go around to the top, bottom, and even cover various control surfaces on the spaceplane.
Recent updated images highlight the progress and complexity of this process. For one, because of the unique shape and rounded body of Dream Chaser, each tile needs to be a perfect fit and contour the body of the spaceplane. Close-ups highlight that there is practically no space between each tile. This is very important as it only takes one tile failure or improper gap to risk the entire vehicle during reentry. On average, Dream Chaser tiles are around 10 inches by 10 inches. This larger size in comparison to the Shuttle and other spacecraft, is a big benefit as it reduces the number of tiles in total and simplifies the installation process. However, while the average tile is quite large, there are plenty of individual spots that require awkward shapes and installs. For example, along the transition between white and black tiles, you can see quite a few small triangular tiles in addition to various shapes. This among other factors is why the installation process takes so long.
To put it in perspective, tile application began nearly three years ago in June of 2020. At that time SNC, the parent company of Sierra Space tweeted saying, “Our Dream Chaser® spaceplane is starting to get the black & white color that’s seen in renderings! We’ve started bonding the Thermal Protection System tiles to the vehicle.” This process would continue over the next few years until its completion only weeks ago.
While this is the first physical test article and tile application, which would partially explain the amount of time needed to install the heat shield, it still took over two years. In reality, if Sierra Space was installing an entire shield today, it would likely be a lot faster as they now have experience. In addition, it’s possible they took their time and matched the tile installation with the general production of the test article. Whatever the case, installing 2000 plus unique tiles will always be a time-intensive process because of its complexity and importance. In addition, assuming the first launch is successful and Dream Chaser Tenacity lands on a runaway, this will give the company great insight into the time needed to refurbish the tiles. The Space Shuttle had a very slow turnaround time due to the amount of work inspecting and replacing various tiles. Something Sierra Space is trying to improve on. The company has already confirmed that each tile is unique in design, and differs in size, shape, thickness, and density, and that they plan to re-waterproof between missions similar to Shuttle.
One last important feature of Dream Chaser’s heat shield is the color of the tiles. Here, the location of the tiles relative to the spaceplane determines its color, either white or black. In this case, the white tiles reject more heat from the sun while on-orbit, which helps to keep the components within Dream Chaser cooler. They have strategically placed certain tiles on different areas of the vehicle for this exact purpose.
New Technology
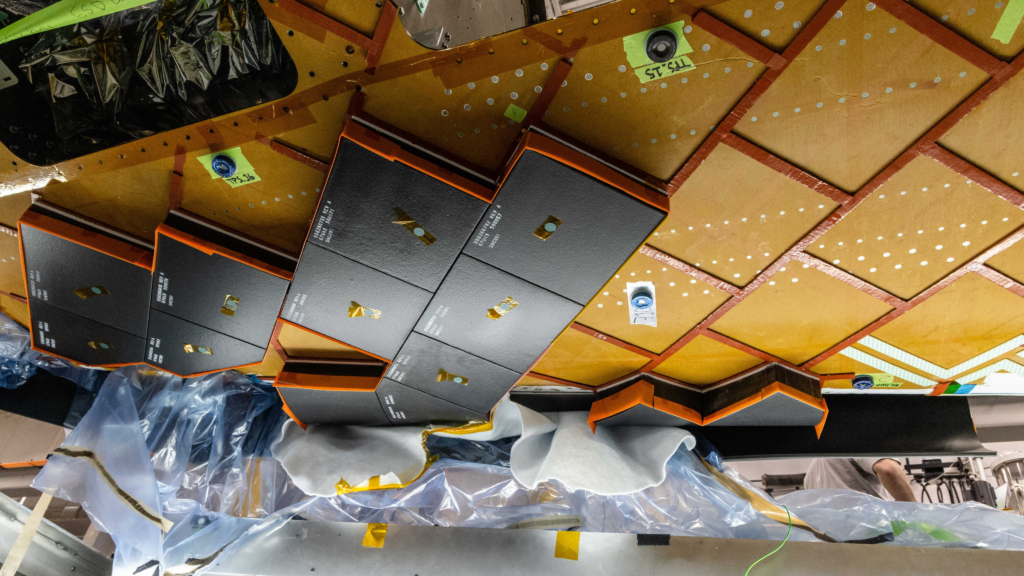
Besides the fact that Dream Chaser’s tiles are bigger and a different color than what we’ve seen in the past, they are also more advanced. The company highlighted that SNC engineers have been able to update the TPS tiles from what was used during NASA’s shuttle program with more innovation, better technology, and utilizing lessons learned. Specifically, they use more modern manufacturing techniques to increase strength and reduce cost. Not to mention, Dream Chaser tiles are stronger and lighter weight than those used during the shuttle program and meet all Micro-Meteroid Orbital Debris (MMOD) requirements to ensure safe entry, descent, and runway landings for crewed or cargo missions.
In the past, SNC also simulated re-entry environments to measure the thermal performance of new silica tile coating developed by NASA and SNC. SNC’s assessments showed that these new coatings offered the same thermal protection as previously flown tile coatings, but at a greatly reduced cost. All of which in an effort to make Dream Chaser not only capable of safely entering Earth’s atmosphere, but also to facilitate a quick and cost-effective turnaround for the next mission.
For years now, SNC has been testing these tiles to make sure they are both a capable and efficient option. Nearly a decade ago in 2015, Sierra Nevada Corporation successfully completed several significant Thermal Protection System (TPS) material development tests for its Dream Chaser spacecraft. The TPS tests were completed at NASA’s Ames Research Center and Johnson Space Center under reimbursable Space Act Agreements (SAA). The tests provided critical data needed to support the TPS subsystem Critical Design Review (CDR) and to validate Dream Chaser TPS manufacturing readiness.
As far as the tests themselves, over 100 arc jet cycles and radiant heat tests were completed at Johnson’s Radiant Heat Test Facility (RHTF) and Ames’ Aerodynamic Heating Facility (AHF). RHTF provided results supporting thermal characterization of the developmental TPS materials. The test data was then used for thermal modeling, analysis, and TPS sizing. The Ames AHF arc jet tests were performed as a second phase in the development testing to gauge the material performance in environments simulating Dream Chaser flight conditions. These arc jet test results supported SNC’s certification of the manufacturing capability of a high-temperature material called Toughened Uni-Piece Fibrous Reinforced Oxidation-Resistant Composite TUFROC. TUFROC will be used on the high-temperature nose and wing leading edges of the Dream Chaser spacecraft.
At the time, the corporate vice president of SNC’s Space Systems commented, “Safety of crew and cargo is most important to our team as we continue to mature the spacecraft design. For several years, we have worked collaboratively with Johnson and Ames, leveraging their existing infrastructure, materials, and expertise to mature and customize the TPS for our unique spacecraft. Our TPS is lighter, stronger, and more efficient than previous generations. We have met or exceeded all mission requirements. We are now prepared to enter the Critical Design Review phase for this system.”
The tiles have the job of protecting Dream Chaser from temperatures that could reach upwards of 3,000°F on entry, while keeping the vehicle itself at only 350°F. For the Space Shuttle, the vehicle’s reentry was defined as starting at an altitude of 120 km (400,000 ft), when it was traveling at approximately Mach 25. The orbiter vehicle’s reentry was controlled by the GPCs, which followed a preset angle-of-attack plan to prevent unsafe heating of the TPS. During reentry, the orbiter’s speed was regulated by altering the amount of drag produced, which was controlled by means of angle of attack, as well as bank angle. For Dream Chaser, there are a few spots on the vehicle that don’t have tiles as thrusters are in the way.
Last month, Sierra Space tweeted saying, “Dream Chaser’s forward down thrusters will experience some of the hottest temperatures on re-entry. Shown with the thermal protection system carrier plate, the thruster nozzles help guide Dream Chaser for docking with the @Space_Station.” This in addition to the tiles will be responsible for withstanding the heat and forces of re-entry.
In terms of the first launch, United Launch Alliance’s Vulcan rocket, is still on schedule to launch in less than a month on December 24th. If successful, a launch of Tenacity in early 2024 is very likely. The test article itself is about to complete its final testing and then it will be ready for flight. There, every one of these new innovations and developments will be put to the test in a real flight environment. Tenacity is only a cargo vehicle so no crew will be aboard in the case that something goes wrong. A mission we can look forward to seeing in just a few months.
Conclusion
Sierra Space has put a lot of time and effort into creating and installing a modern spaceplane heat shield, capable of protecting the vehicle and launching consistently. There are a lot of improvements that are meant to speed up this process and increase the chances of success. We will have to wait and see how it progresses and the impact it has on the space industry.